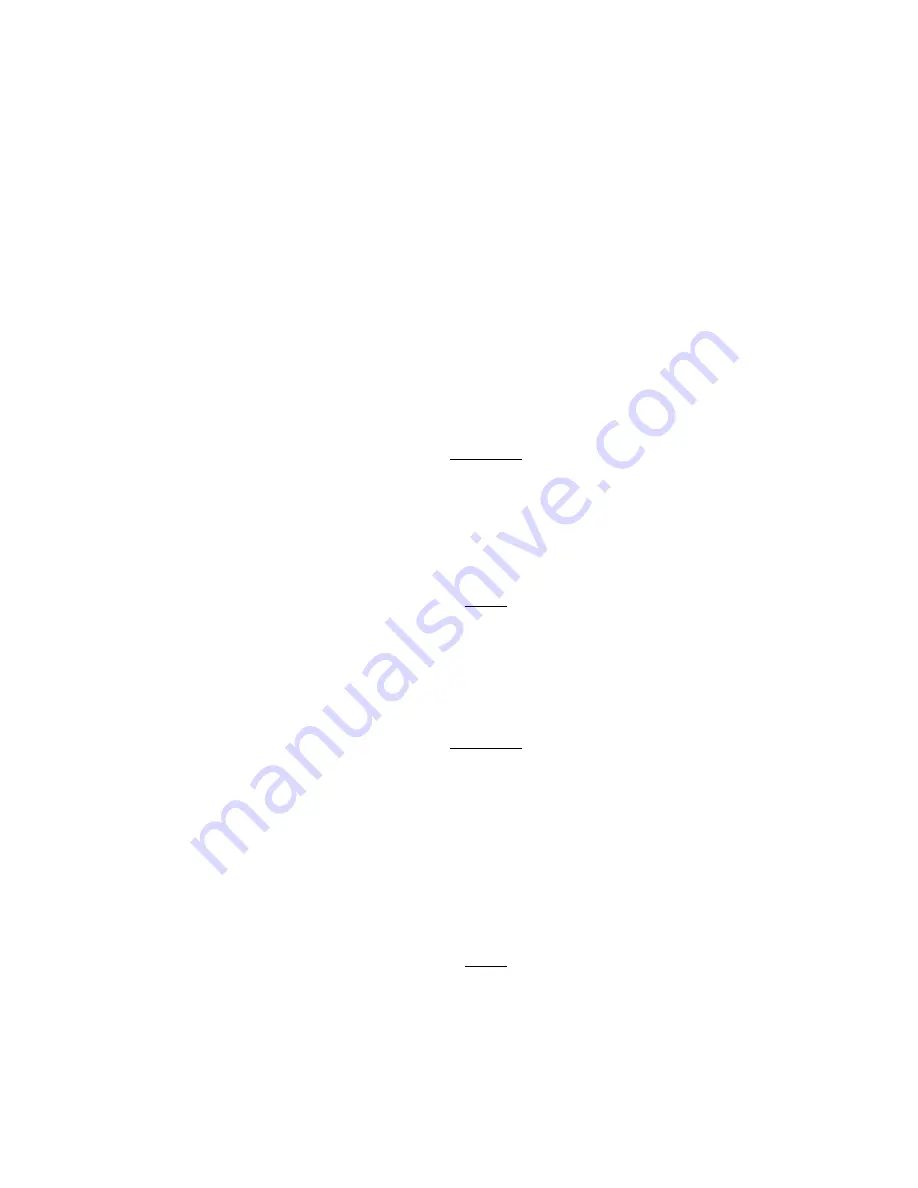
4
2.5
YEARLY
A. Clean water bath interior, including evaporator coils and refrigeration components.
B. Clean the entire exterior of the unit.
C. Sanitize syrup lines.
3. DISPENSER CLEANING AND SANITIZING
3.1
AMBIENT PROCESS
A. The ambient process is the most common method for cleaning and sanitizing dispenser
equipment. The detergent should be caustic-based and the sanitizer should be low pH (7.0)
chloride solution.
B. Disconnect syrup containers and remove product from tubing by purging with carbon dioxide.
C. Rinse the lines and fittings with clean room temperature water to remove all traces of residual
product.
D. Fill lines with a caustic-based (low-sudsing, non-perfumed, and easily rinsed) detergent solution.
The solution should be prepared in accordance with the manufacturer’s recommendations, but
should be at least two (2) percent sodium hydroxide. Make sure the lines are completely filled
and allow to stand for at least 10 minutes.
E. Flush the detergent solution from the lines with clean water. Continue rinsing until
phenolphthalein test indicates the rinse water is free of residual detergent.
WARNING
REMOVE SANITIZING SOLUTION FROM DISPENSER AS INSTRUCTED. RESIDUAL
SANITIZING SOLUTION LEFT IN SYSTEM COULD CREATE HEALTH HAZARD.
F. Fill the lines with a low pH (7.0) chlorine solution containing at least 50 PPM (50 mg/L) chlorine.
Make sure that lines are completely filled and allow to stand for 10 minutes.
G. Reconnect syrup containers and ready Unit for operation.
H. Draw drinks to refill lines and flush the chlorine solution from the dispenser.
NOTE
Please note that a fresh water rinse cannot follow sanitization of equipment. Purge only with the
end use product.
This is an NSF requirement.
I.
Taste the beverage to verify that there is no off taste.
3.2
VALVES
A. Valves may be cleaned and sanitized in the same manner
WARNING
REMOVE SANITIZING SOLUTION FROM VALVES AS INSTRUCTED. RESIDUAL
SANITIZING SOLUTION LEFT IN SYSTEM COULD CREATE HEALTH HAZARD.
I . Remove cover and disconnect power so not to activate the valve while cleaning. Remove
nozzle and diffuser. Wash these parts in cleaning solution, then immerse them in a bath of
sanitizing solution for 15 minutes.
2. Visually inspect around nozzle area for syrup residue. This area may be cleaned with warm
water and cloth or with the nozzle brush supplied. Wipe off dispensing lever.
3. Wearing sanitary gloves, remove, drain and air dry the nozzle and diffuser.
4. Wearing sanitary gloves, replace diffuser and twist nozzle into place.
5. Draw drinks to flush the chlorine solution from the valves.
NOTE
Please note that a fresh water rinse cannot follow sanitization of equipment. Purge only with
the end use product.
This is an NSF requirement.
6. Taste the beverage to verify that there is no off taste.
7. Connect power and replace cover. Valve is ready for operation.