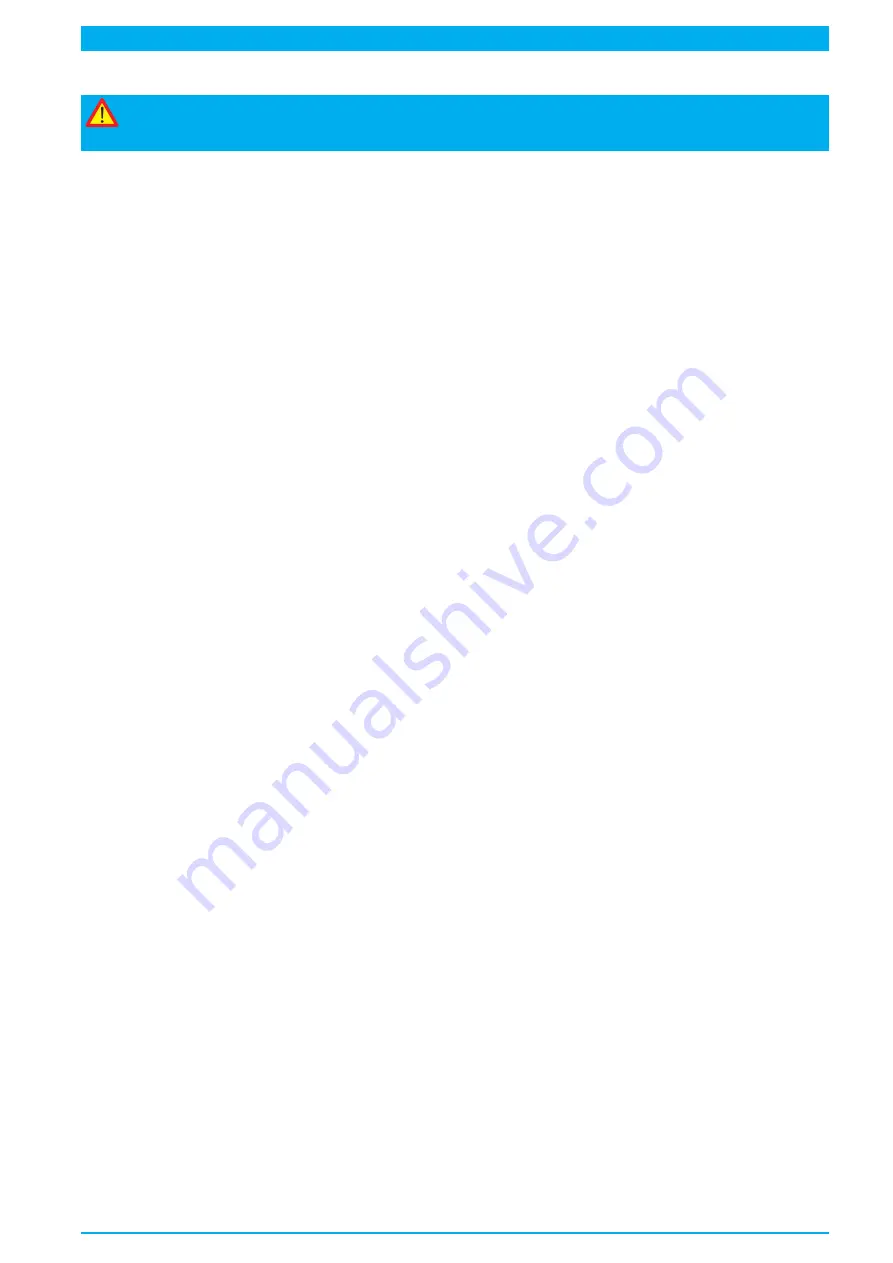
Page 11
Transportation
Accident prevention!
The equipment may only be transported with sufficient means of transportation.
It must be fixed securely during transportation. Avoid knocks to the equipment.
The equipment can be moved on a pallet to in-plant transport via an elevating platform truck or forklift truck.
When moving the equipment mind the weight to prevent it from tipping or rolling.
• When moving the equipment keep the lifting height as low as possible.
• When moving the equipment pay attention that all electrical and pneumatic connections (also to the wiring
harness and if required, reserve air storage tank) are disconnected.
• Observe the safety regulations for handling the elevating platform truck or forklift truck when moving equip-
ment.
Storage
General information on storage
• If the equipment is not installed and started up immediately, it must be stored under appropriate storage
conditions in a dry, dust and frost-free indoor area, protected from sunlight.
• The equipment should be wrapped in plastic or foil packaging.
• The storage time should not exceed one year.
Functionality of pressurization system RTS 1000
The compressors draw in external air and compress this to approx. 6 bar. Then the compressed air is
channelled in the air dryer, alternatively by two drying agent containers, in which the air is dehumidified. In
doing so, the air is only dried in one drying agent container, while at the same time in another drying agent
container the existing drying agent is regenerated by a branch current of the already dried air. The humid rege-
neration air blows out through the diffuser.
The air dried in this way is stored in the air storage tank with a pressure between 3.0 and 5.0 bar. A pressure
monitor ensures sufficient compressed air in the air storage tank, in which it switches the compressors on and
off. The existing air pressure in the air storage tank can be read on the "high pressure" manometer. A built-in
air regulator reduces the stored compressed air from the air storage tank to the required cable pressure. This
can be read on the "cable pressure" manometer.
This pressure-reduced air reaches the distribution device of the connected cable network via an shut-off valve
and an injector. In order to guarantee proper operation the dried compressed air is constantly checked for its
humidity content in the MFR unit. If the relative air humidity rises over approx. 4%, the compressor is switched
off.
The pressure in the air storage tank is constantly monitored. If this rises to 7.0 bar, the pressure is blown off
via a safety valve.
The equipment runs fully automatically after startup. Operational upsets are displayed on the mulit functional
relay (MFR) and the ACS unit at the instrument panel. In addition these fault signals are relayed to an external
control centre.
The MFR distributes the drying and regenerating processes evenly to both drying containers by means of the
solenoid valves. So none of them will be flooded, when only little amounts of air are produced. The solenoid
valves also allow for unpressurised compressor starts.
Summary of Contents for RTS 1000
Page 15: ...Page 15 39 35 37 36 36 23 42 28 27 24 6 33 38 40 41 32 22 29 25 8...
Page 21: ...Page 21...
Page 47: ...Page 47 7 16 14 15 15 18 17 13 20 24 8 23 10 6 9 4 22 21 19 8...
Page 51: ...Page 51 Pneumatics diagram Nr 074891 000...
Page 53: ...Page 53 Circuit diagram Nr 074880 000...