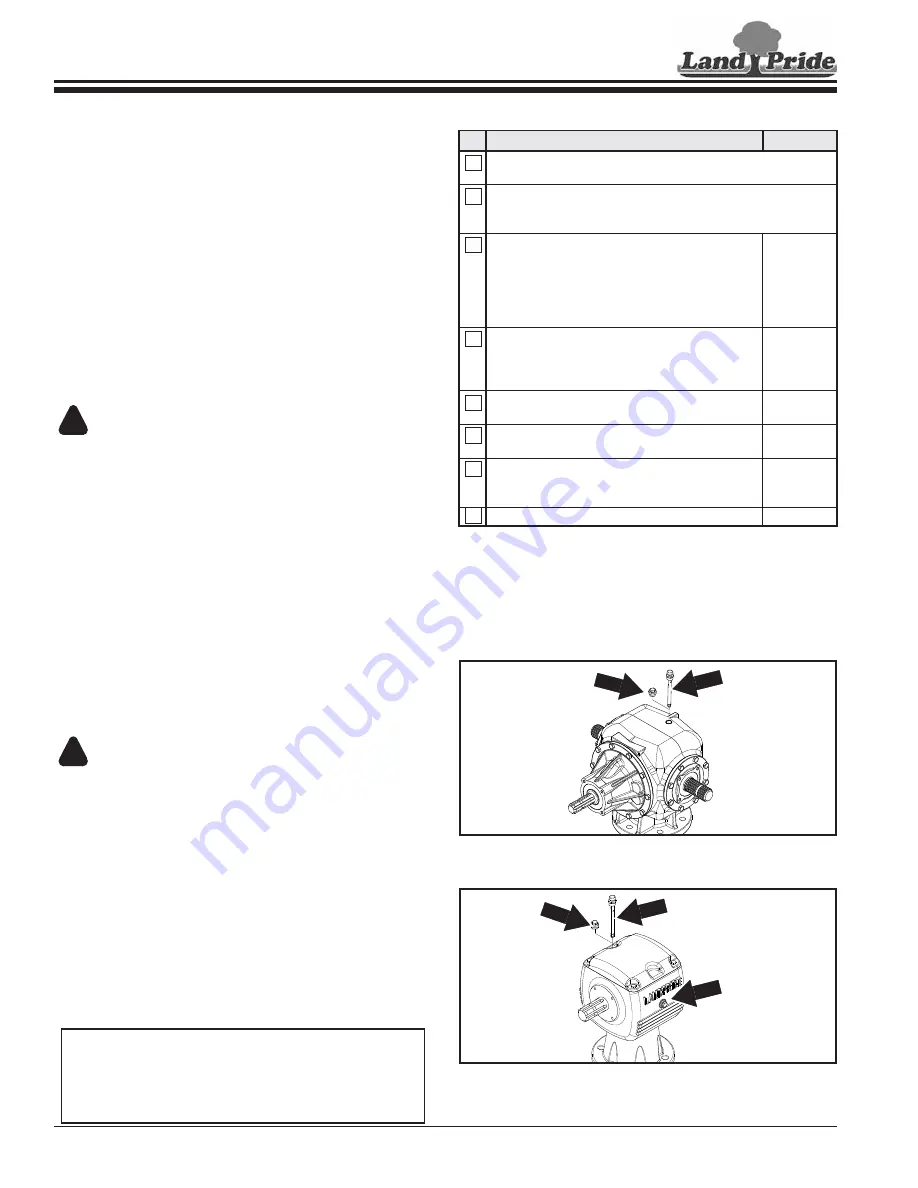
Section 1: Assembly & Set-Up
RCFM4014 Rotary Cutter 326-730M
8/11/14
12
Section 1:
Assembly & Set-Up
Tractor Requirements
Tractor horsepower, hitch category, and weight must be
capable of controlling the cutter under all operating
conditions. Tractors outside the horsepower range must
not be used.
Horsepower rating . . . . . . . . . . . . . . . Minimum 80 hp
Hitch category . . . . . . . . . . . . . . . . . . . . . . Cat. ll or lll
Rear power take-off Speed . . . . . . . . . . . . . .1000 rpm
Power take-off Shaft type:
Optional. . . . . . . . . . . . . . . . . . . . . 1 3/8"-21 Spline
Optional. . . . . . . . . . . . . . . . . . . . . 1 3/4"-20 Spline
Tractor weight . . . . . . . . . . . . . . . 12,000 lbs. Minimum
The lower 3-point arms of the 3-point hitch must be
stabilized to prevent side-to-side movement. Most
tractors have sway blocks or adjustable chains for this
purpose.
WARNING
!
To avoid serious injury or death:
•
Do not use a tractor that is too small. Small tractors can be
pushed around and flipped over by the weight of the
•
Lightweight tractors with rear attached implements may
need weights added to the front to maintain steering control.
Consult your tractor Operator’s Manual to determine
proper weight requirements and maximum weight
Torque Requirements
Refer to
“Torque Values Chart”
determine correct torque values for common bolts. See
at bottom of chart for
exceptions to standard torque values.
Dealer Preparations
WARNING
!
To avoid serious injury or death:
Always secure cutter with an overhead crane, fork lift, or
other suitable lifting device before removing hardware bags,
shipping components, bands, lag screws, or hitch pins. The
Read and understand this Operator’s Manual. An
understanding of how this cutter works will aid in its
assembly and setup.
It is best to go through the
Pre-Assembly Checklist
before assembling the cutter. Speed up your assembly
task and make the job safer by having all the needed
parts and equipment readily at hand.
Gearbox Vented Dipsticks
IMPORTANT:
Gearboxes are shipped with solid
Refer to Figure 1-1 & Figure 1-2:
Vented dipsticks are shipped loose and packaged with
the Operator’s Manual. See your nearest Land Pride
dealer if dipstick is missing. Remove temporary solid plug
from top of each gearbox and replace with supplied
dipsticks.
Splitter/Center Spindle Gearbox
Figure 1-1
Outside Spindle Gearboxes
Figure 1-2
Pre-Assembly Checklist
Check
Ref.
Have a minimum of two people available during
assembly.
Have a fork lift or loader along with chains and safety
stands that are sized for the job ready for the assembly
task.
Location of fasteners and pins.
NOTE:
All hardware from the factory has
been installed in the location where it will be
used. If a part is temporarily removed for
assembly reasons, remember where it goes.
Keep parts separated.
Operator’s
and Parts
Manual
Be sure parts get used in the correct
location. Double check to lessen the chance
of using a bolt incorrectly that may be
needed later.
Operator’s
and Parts
Manual
Make sure safety labels are correctly
located and legible. Replace if damaged.
Make sure all grease fittings are in place and
lubricated.
Make sure red, amber, and orange reflectors
are correctly located and visible when cutter
is in the transport position.
Tighten wheel bolts to specified torque.
37155
Install Vented
Dipstick
Remove T-box
Solid Plug
30216
Oil Level Plug
DO NOT
OVERFILL!
Remove
Solid Plug
Install
Vented Dipstick