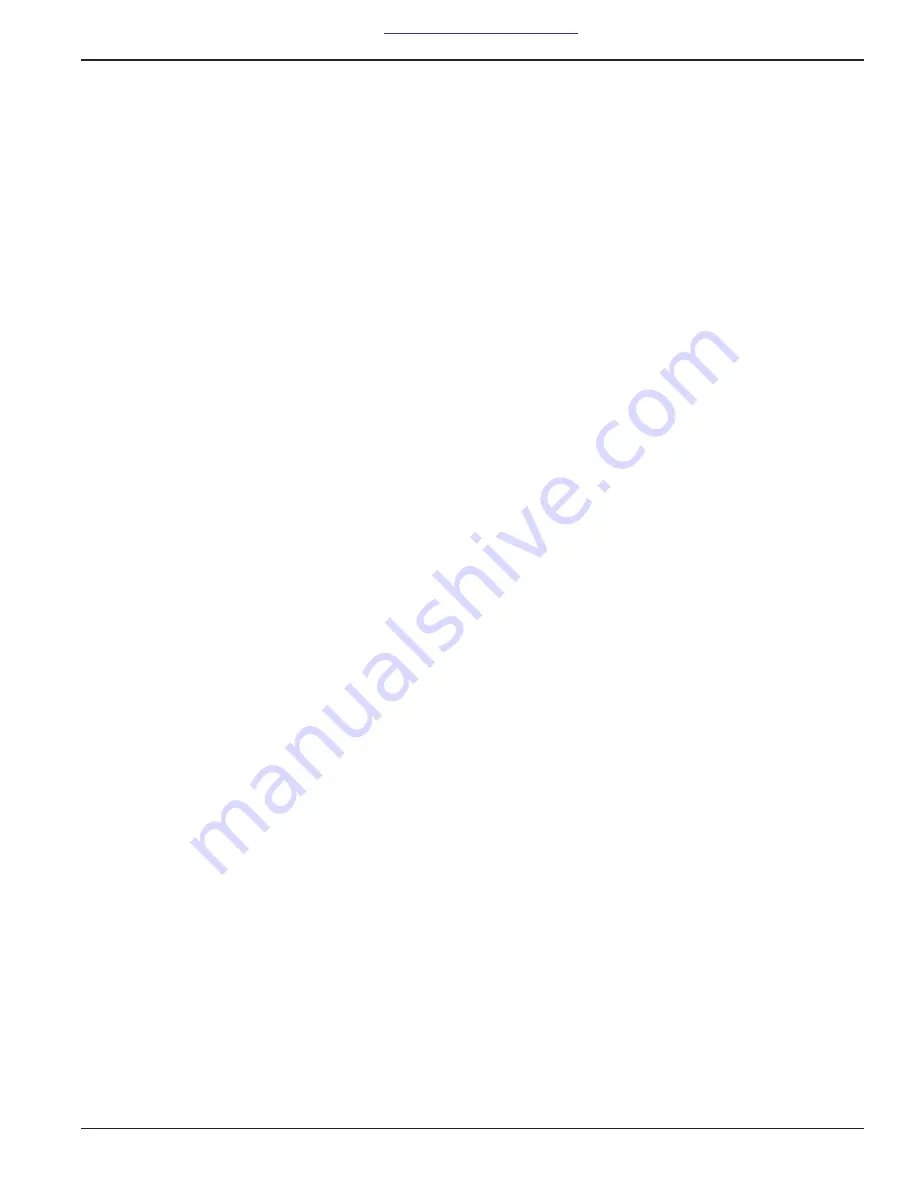
MAINTENANCE AND LUBRICATION
4-25
Rocking Upper Coupler Maintenance
The rocking upper coupler requires very little
maintenance. Primary item is to include the upper
coupler in the routine greasing portion of a normal
maintenance program. Three grease zerks are located
on the roadside of the coupler and require only a slight
amount of grease at each periodic greasing. The only
other maintenance is to ensure adequate grease is on
the surface between the coupler and the fifth wheel,
.
Gate Control Valve Service
To clean, inspect and lubricate the valve is easily
removed from the subplate by removing the three
mounting screws. It is not necessary to disconnect the
piping or to remove the subplate for most servicing
requirements.
1.
Disassemble the valve in clean and well-lit area.
Clean all metal parts in a non-flammable solvent and
wash all rubber parts in soapy water. Rinse all parts
and thoroughly dry with a low pressure air hose.
Replace damaged or worn parts. Removal of the
internal plug is not recommended unless
replacement is required.
2.
Worn parts can be replaced by removing the four
bleeding housing screws and the four operator
handle housing screws and sliding the spool out of
the valve.
3.
Reassembly the valve. No special tools are required.
When the “U” cup of the piston is replaced, ensure
the two lip seals face toward the operator handle end
of the valve.
4.
Lubricate all metal-to-metal surfaces with an
appropriate pneumatic grade lubricant.
Clamshell Gate Air System Filter
1.
Remove and clean the clamshell gate air filter
periodically by tapping on hard surface and blowing
the air filter out with an air gun.
2.
Drain the bowl at least once per work shift.
Clamshell Gate Air Lubricator
1.
Dirty oil contaminants can collect on the siphon tube
inlet filter. Clean the filter by tapping it on a hard
surface and blowing it off with an air gun.
2.
If the oil delivery rate drops below the three drops per
cycle required the lubricator should be cleaned.
Remove the variable orifice and clean the air
passage with a small wire. Check the bore the screw
threads into for contaminants and clean if necessary.
Ensure the passageway from the sight dome cavity
into the variable orifice post is open. Remove the oil
flow adjusting screw and clean the needle and seat in
the body. Inspect and clean the passage from the
needle seat into the adapter.
3.
Drain any contaminants that collect in the bottom of
the bow.