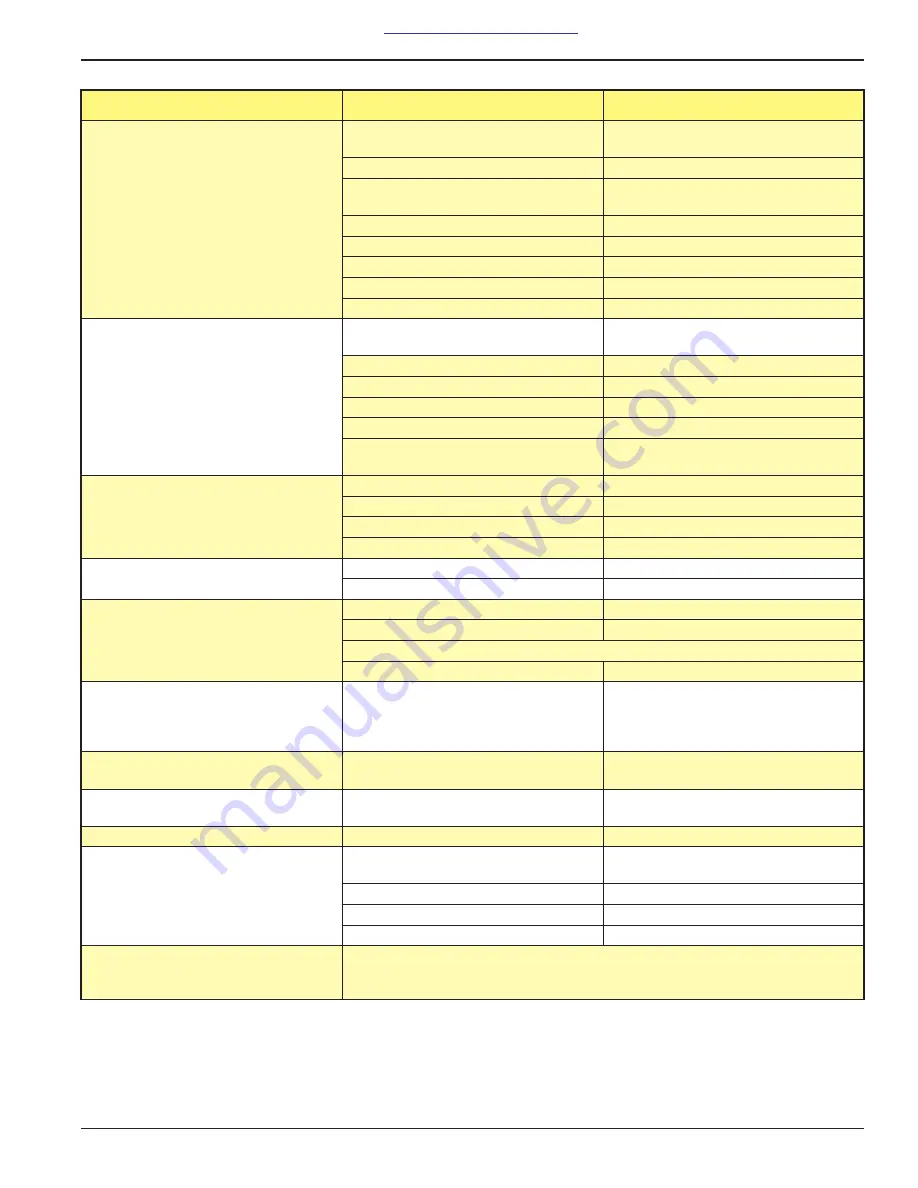
TROUBLESHOOTING GUIDE
5-5
ALL BRAKES DO NOT RELEASE
Air system improperly connected to
tractor
Tighten or adjust connections.
Brake valve on tractor is applied
Release brake
Relay emergency valve in emergency
position
Check line pressure and check valve
Restricted tubing or line
Locate restriction and remove
Defective tractor protection valve
Troubleshoot tractor air system.
Parking brakes locked
Troubleshoot air system
Moisture in air system
Check air system
Tractor pressure too low
Adjust to provide 105 psi min.
INSUFFICIENT BRAKES
Brakes need adjusting
Adjust brakes
Brakes need lubricating
Lubricate brakes
Brakes need relining
Reline brakes
Low air pressure
Troubleshoot air system.
Defective relay emergency valve
Repair or replace.
Brakes overheated
Stop and allow brakes to cool, locate
cause of overheating.
BRAKES GRABBING
Grease on brake linings
Reline brakes
Brake rigging binding
Align brakes or replace bent parts.
Defective brake valve on tractor
Repair or replace valve.
Defective relay emergency valve
Repair or replace valve.
EXCESSIVE LEAKAGE WITH BRAKES
RELEASED
Relay emergency valve leaking
Repair or replace valve
Leaking tubing or hose
Replace defective part.
EXCESSIVE LEAKAGE WITH BRAKES
APPLIED
Relay emergency valve leaking
Repair or replace valve.
Leaking brake chamber diaphragm
Replace diaphragm.
Call Factory or see qualified Trailer/Brake Technician
Leaking tubing or hose
Replace defective part.
EXCESSIVE LEAKAGE WITH
EMERGENCY SYSTEM ONLY
APPLIED - NO LEAKAGE WITH
NORMAL BRAKING
Defective relay emergency valve
Repair or replace valve.
EXCESSIVE WATER PRESENT IN
BRAKE SYSTEM
Reservoir not drained often enough
Drain reservoir daily.
EXCESSIVE OIL PRESENT IN BRAKE
SYSTEM
Compressor on tractor passing
excessive oil
Repair compressor.
BRAKE WILL NOT APPLY PROPERLY
Flat spot on cam roller or camshaft
Replace and lubricate.
BRAKES WILL NOT APPLY WHEN
EMERGENCY LINE IS
DISCONNECTED
Initial air pressure too low
Allow air system to build up to
minimum 90 PSI and stabilize.
Defective relay valve
Repair or replace valve.
Air line leak
Locate leak and repair.
Brake chamber leak
Locate leak and repair or replace.
ABS WARNING LIGHT STAYS
ON
Refer to Rockwell WABCO ABS maintenance manual supplied with semitrailer, for
system function and use of blink code diagnostics.
PROBLEM
PROBABLE CAUSE
SOLUTION