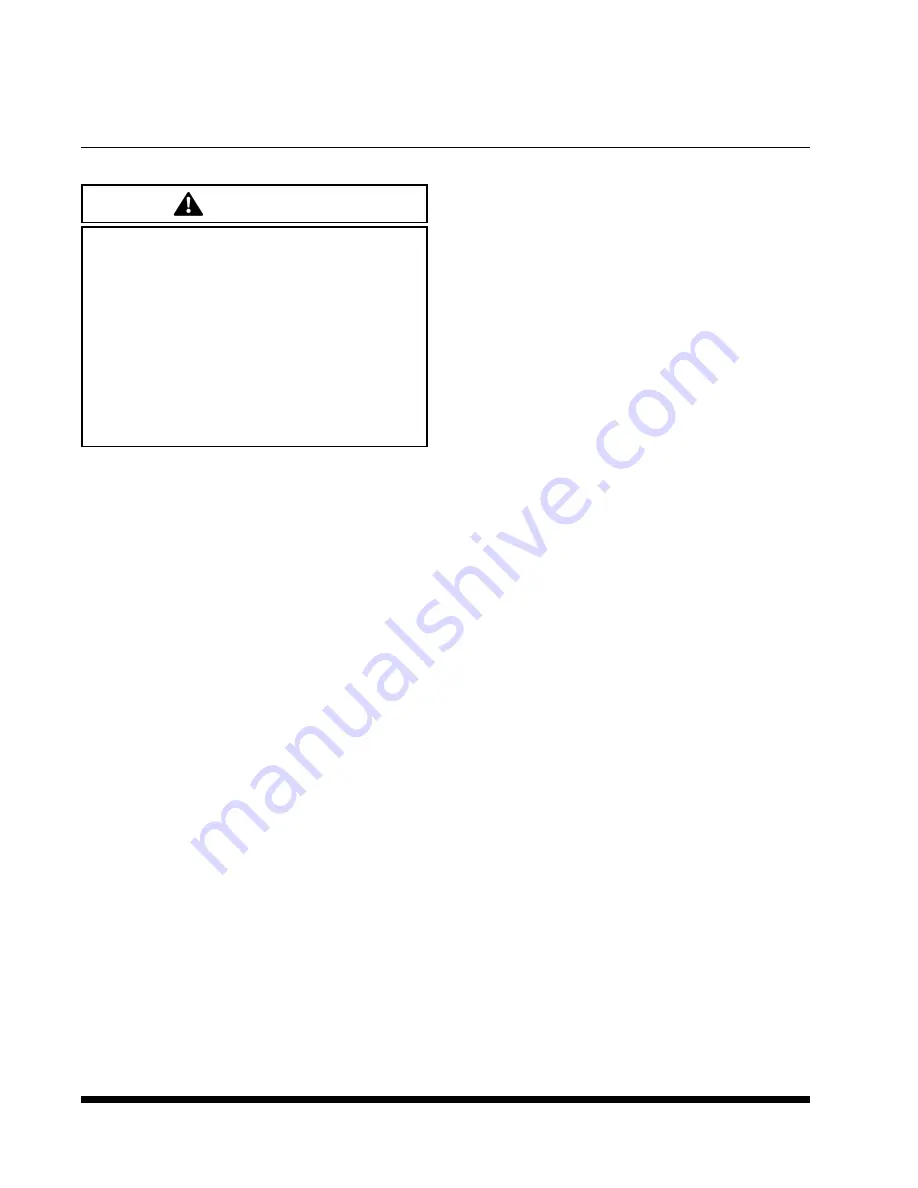
4-14 AIR SYSTEM FILTER AND LUBRICATOR
WARNING
CERTAIN COMPRESSOR OILS, CHEMI-
CALS, HOUSEHOLD CLEANERS, SOL-
VENTS, PAINTS, AND FUMES WILL AT-
TACK PLASTIC BOWLS AND CAN
CAUSE BOWL FAILURE. DO NOT USE
NEAR THESE MATERIALS. IMMEDI-
ATELY REPLACE ANY CRAZED,
CRACKED, DAMAGED, OR DETERIO-
RATED PLASTIC BOWL WITH A NEW
PLASTIC BOWL AND METAL BOWL
GUARD.
4-14.1
Cleaning the Air System Filter
a.
Drain the bowl at least once per work shift.
b.
Remove and clean the filter periodically by
tapping on a hard surface.
c.
If necessary remove dirt from the inside of
the bowl by wiping it with a clean, dry cloth.
This requires the air pressure in the line to be
completely exhausted and the bowl to be re-
moved form the body.
d.
Do not attempt to clean the bowl with a sol-
vent.
4-14.2
Lubrication
a.
Under average service conditions, the lubri-
cator bowl should be kept filled above the
level of the bottom of the siphon tube with a
petroleum based oil. Preference of oil is an
SAE-5 or SAE-10 motor oil or hydraulic oil.
b.
In colder weather, or under more severe
service conditions, an automobile automatic
transmission fluid should provide better per-
formance.
c.
In damp, below freezing conditions, freezing
water in the air lines can cause air system
problems. Lubricating oil should be replaced
with Kil-Frost, available through parts dealers.
d.
The unit may be filled (or cleaned) under
pressure by first removing the fill plug, then
removing the bowl.
e.
Do not replace the fill plug until the bowl and
guard are in position and the clamp ring is
locked into place.
IMPORTANT
DO NOT USE A SYNTHETIC BASED OIL.
4-14.3
Cleaning the Lubricator
a.
Dirty oil contaminants can collect on the si-
phon tube inlet filter. Clean it by tapping it on
a hard surface.
b.
If the oil delivery rate drops, the lubricator
should be cleaned. Remove the variable ori-
fice and clean its air passage with a small
wire. Check the bore that the screw fits into
for contaminants and clean, if needed. Be
sure that the passageway from the sight
dome cavity into the variable orifice post is
open. Remove the oil flow adjusting screw
and clean the needle and seat in the body. In-
spect and clean the passage from the needle
seat down into the adapter.
c.
Drain and clean the lubricator bowl when-
ever contaminants collect over 1/4" deep in
the bottom of the bowl. The bowl may be re-
moved with the air system pressurized. It
should be wiped clean with a clean, dry cloth.
d.
Do not attempt to clean the bowl with a sol-
vent.
4-14.4
Oil Rate Delivery Adjustment
a.
The rate of oil delivery from the lubricator
should be set at one drop for each three (3)
complete cycles(open and close) of the air
valve.
b.
The rate of oil delivery is controlled by turn-
ing the adjusting screw counterclockwise
(ccw), for increased flow, and clockwise (cw)
for decreased flow.
c.
To gain access to the drip rate adjusting
screw, the tamper resistant cap must be re-
moved.
4-26
Summary of Contents for 336C
Page 3: ...MODEL 336C CAR CARRIER OPERATOR S MANUAL PURCHASED FROM DATE ADDRESS PHONE NO SERIAL NO...
Page 8: ......
Page 24: ...3 12 Figure 3 7 Lining Up the Over the Cab Deck Figure 3 8 Loading the Over the Cab Deck...
Page 28: ...3 16 Figure 3 11 Loading the Lower Deck...
Page 32: ...3 20 Figure 3 13 Rear Impact Guard and Antilock Brake System...
Page 40: ...4 6 Figure 4 3 336C Wiring Diagram...
Page 45: ...4 11 Figure 4 7 Checking Axle for Bend Figure 4 8 Examples of Camber...
Page 50: ...4 16 Figure 4 12 Axle and Brake Assembly...
Page 54: ...4 20 Figure 4 14 Outboard Mount Hub and Drum Figure 4 15 Inboard Mount Hub and Drum...
Page 59: ...4 25 Figure 4 19 Mounting Tires and Wheels Figure 4 20 Stud Tightening Sequence...
Page 70: ...NOTES 5 10...