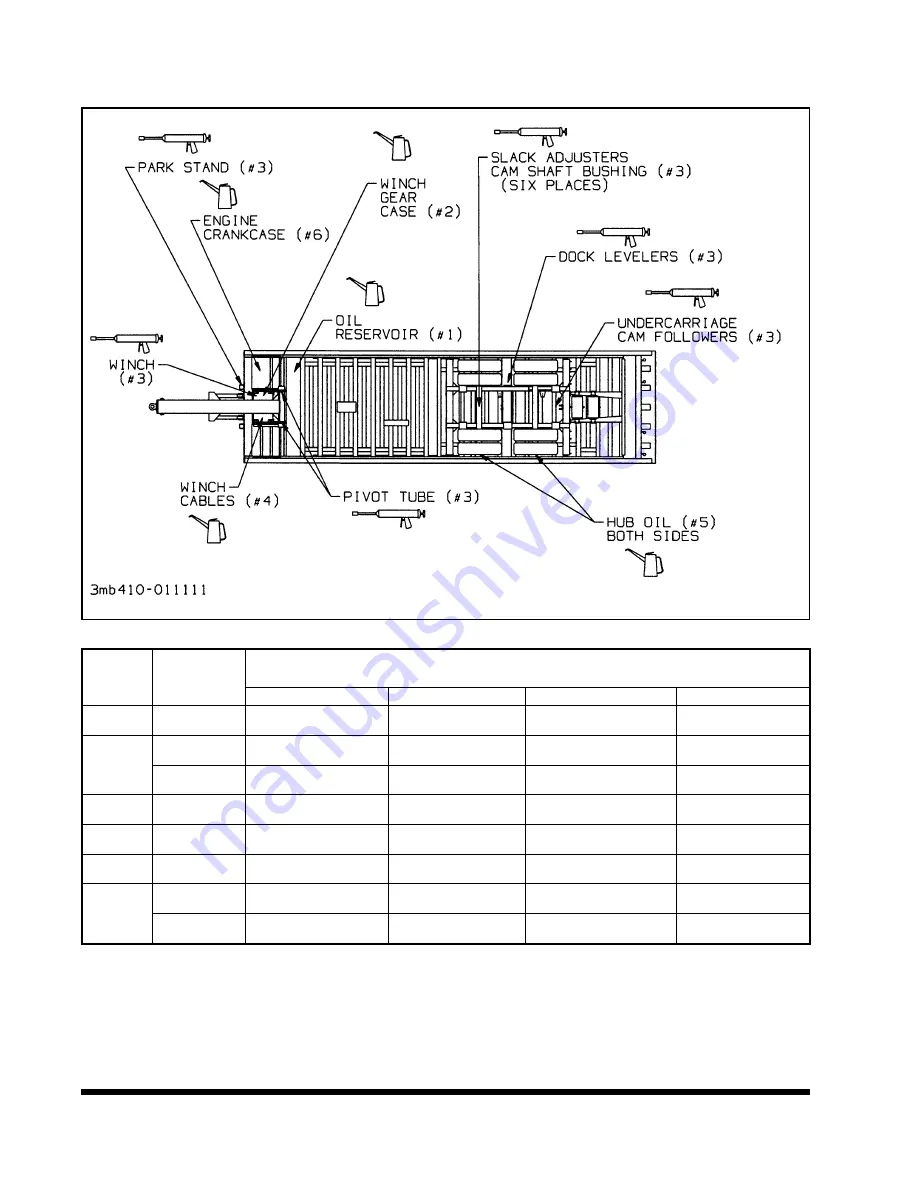
2
LUBE
SEASON
BRAND AND PRODUCT
(WEIGHT AND/OR TYPE)
AMOCO
EXXON
PHILLIPS
TEXACO
1
ALL YEAR
Rycon MV
HDX Plus 10W
Mangus Oil
A KV 5W-20
Rando HD-AZ
2
SUMMER
Permagear EP 460
SAE 140
Spartan 460
SAE 140
Phil Gear Lube 460
SAE 140
Meropa 460
SAE 140
WINTER
Permagear EP 220
SAE 90
Spartan 220
SAE 90
Phil Gear Lube 220
SAE 90
Meropa 220
SAE 90
3
ALL YEAR
Lit-Multi-purpose
Grease
Ronex Multi-purpose
Grease
Phil Lube M.W. Grease MarFax All Purpose
4
ALL YEAR
Industrial
Oil 32
Estic 32
Condor 32 or
Magnus 32
Regal Oil
R&O 32
5
ALL YEAR
Gear Lube
SAE 80W-90
Gear Oil GX
SAE 80W-90
Superior MP Gear Oil
SAE 80W-90
Multi-gear EP SAE
80W-90
6
ABOVE
0
o
F
Ultimate Gold
10W-30, 10W-40
SuperFlow
10W-30, 10W-40
Tropartic
10W-30, 10W-40
Havoline
10W-30, 10W-40
BELOW
32
o
F
Ultimate Gold 5W-20,
5W-30
SuperFlow
5W-20, 5W-30
Tropartic
5W-20, 5W-30
Havoline
5W-20, 5W-30
Table 4-1 Lubrication Specifications
Figure 4-1 Lubrication Points
Summary of Contents for 345B
Page 3: ...MODEL 345B TRAILER OPERATOR S MANUAL PURCHASED FROM DATE ADDRESS PHONE NO SERIAL NO ...
Page 8: ......
Page 12: ......
Page 22: ...3 10 Figure 3 4 Steps for Loading and Unloading ...
Page 26: ...3 14 Figure 3 7 Rear Impact Guard and Antilock Brake System ...
Page 30: ......
Page 35: ...4 5 Figure 4 2 345B Wiring Diagram ...
Page 36: ...4 6 Figure 4 3 Remote Wiring Diagram ...
Page 41: ...4 11 Figure 4 5 Examples of Camber Figure 4 6 Checking Axle for Bend ...
Page 46: ...4 16 Figure 4 10 Axle and Brake Assembly ...
Page 50: ...4 20 Figure 4 13 Outboard Mount Hub and Drum Figure 4 14 Inboard Mount Hub and Drum ...
Page 54: ...4 24 Figure 4 18 Mounting Tires and Wheels Figure 4 19 Stud Tightening Sequence ...
Page 65: ...5 9 NOTES ...