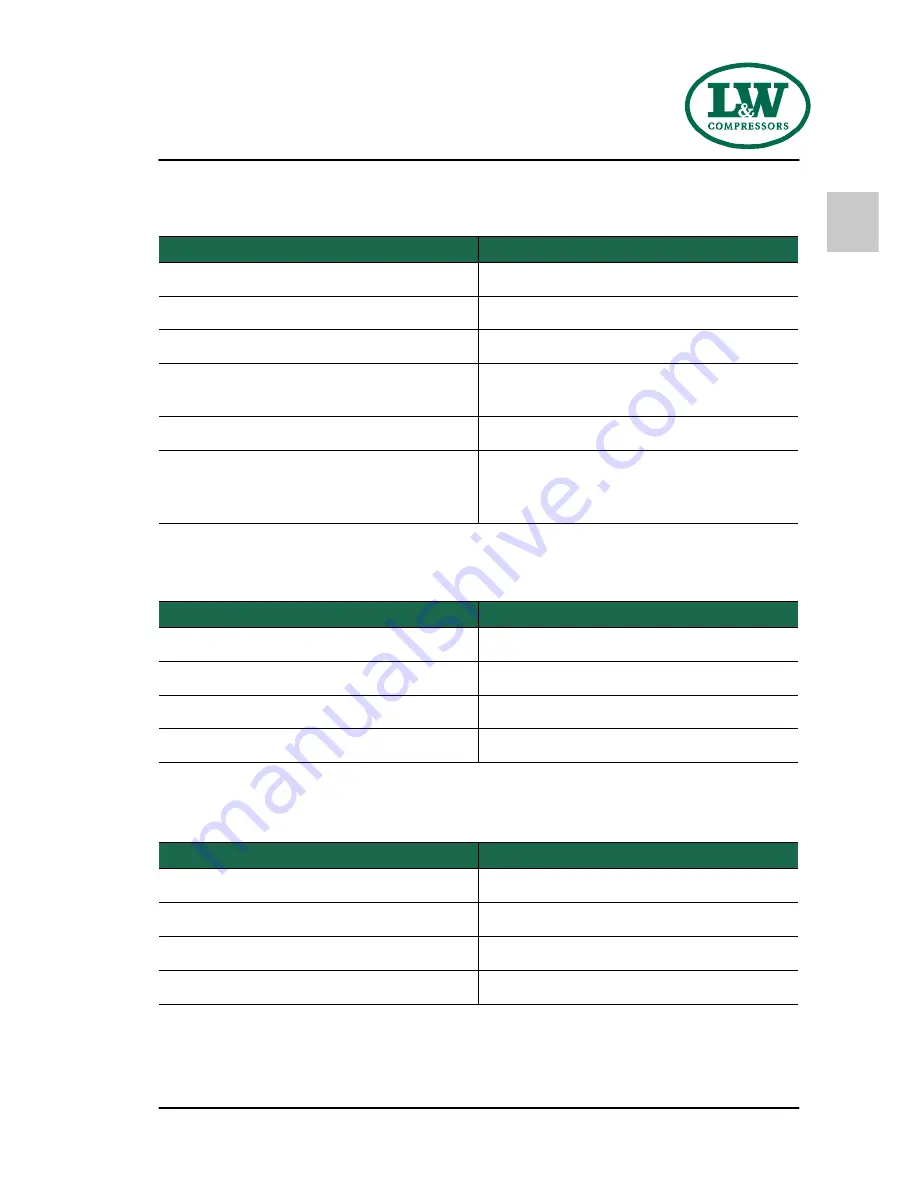
Page A - 38
A
LW 225 E / LW 245 B
Version: 19.11.2015
R E M E D Y I N G F A U L T S
Final pressure can not be reached
Strong compressor vibration
Cause of fault
Remedy
V-belt tension too loose
Tension V-belt
Drive motor / Compressor unit loosely
Retighten mounting screws
Anti vibration mounts used up
Replace
Ground not levelled
Ensure a solid and level ground
Cause of fault
Remedy
Connections leaky
Retighten or clean/replace if necessary
Final pressure safety valve leaky
Replace
Pipes / heat exchanger broken
Replace
Condensate drain valves leaky
Unscrew valves, check sealing surfaces, clean,
replace if necessary
Final pressure switch stop unit
Verify settings, replace if necessary
Piston of pneumatic condensate valve sticks
Clean pneumatic condensate valve and restore
function, check/replace o-rings, replace valve
completely if necessary
Air supply too low
Cause of fault
Remedy
Inlet and outlet valves contaminated / defective
Clean, replace if necessary
Cylinder(s), piston(s) or piston ring(s) used up
Replace
V-belt slips
Tension V-belt
See chapter "Final pressure can not be reached" See chapter "Final pressure can not be reached"
Summary of Contents for LW 225 E
Page 3: ...A Operating Instructions Breathing Air Compressor LW 225 E LW 245 B Version 02 14 E ...
Page 15: ...A S A F E T Y P R E C A U T I O N S ...
Page 22: ...A I N S TA L L AT I O N ...
Page 31: ...A O P E R AT I O N ...
Page 39: ...A R E M E D Y I N G FA U LT S ...
Page 44: ...A M A I N T E N A N C E A N D S E R V I C E ...
Page 73: ...A M A I N T E N A N C E R E C O R D S ...
Page 82: ...B ERSATZTEILLISTEN SPARE PARTS LISTS DETAILANSICHTEN DETAILED VIEWS ...
Page 111: ...C O P T I O N S Version 11 12 D ...
Page 113: ...C A U T O S H U T D O W N D 2 LW 225 E 245 B ...
Page 116: ...C A U T O M A T I C C O N D E N S AT I O N D R A I N D 5 LW 225 E 245 B ...
Page 118: ...C S W I T C H O V E R D E V I C E 2 0 0 3 0 0 B A R D 7 LW 225 E 245 B ...
Page 121: ...C A D D I T I O N A L F I L L I N G H O S E D 10 LW 225 E 245 B ...