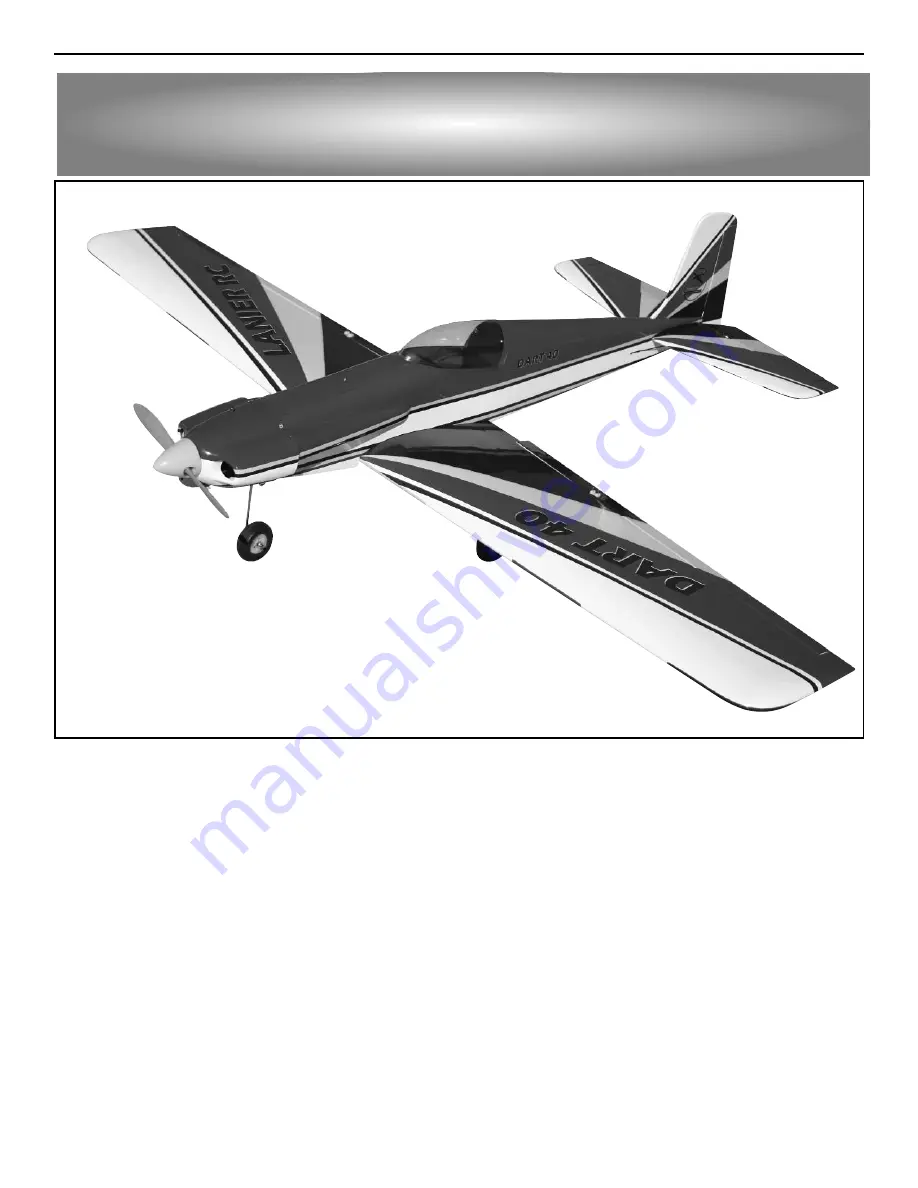
Dart ARF
Lanier R/C, INC. P.O. Box 458 Oakwood, Ga. 30566 PH 770 532 6401 ©copyright 1989 Lanier R/C, Inc.
1
1
Thank you for purchasing the Lanier R/C Dart. We are sure you
will be happy with the quality of the kit and happy with the flying
characteristics of the Dart. Because of it’s light weight,the Dart will
fly exceptionally well on a standard .40 size motor. This makes the
Dart a perfect “first time” low wing airplane. The gentle flying char-
acteristics and good aerobatic ability make is a joy to fly.