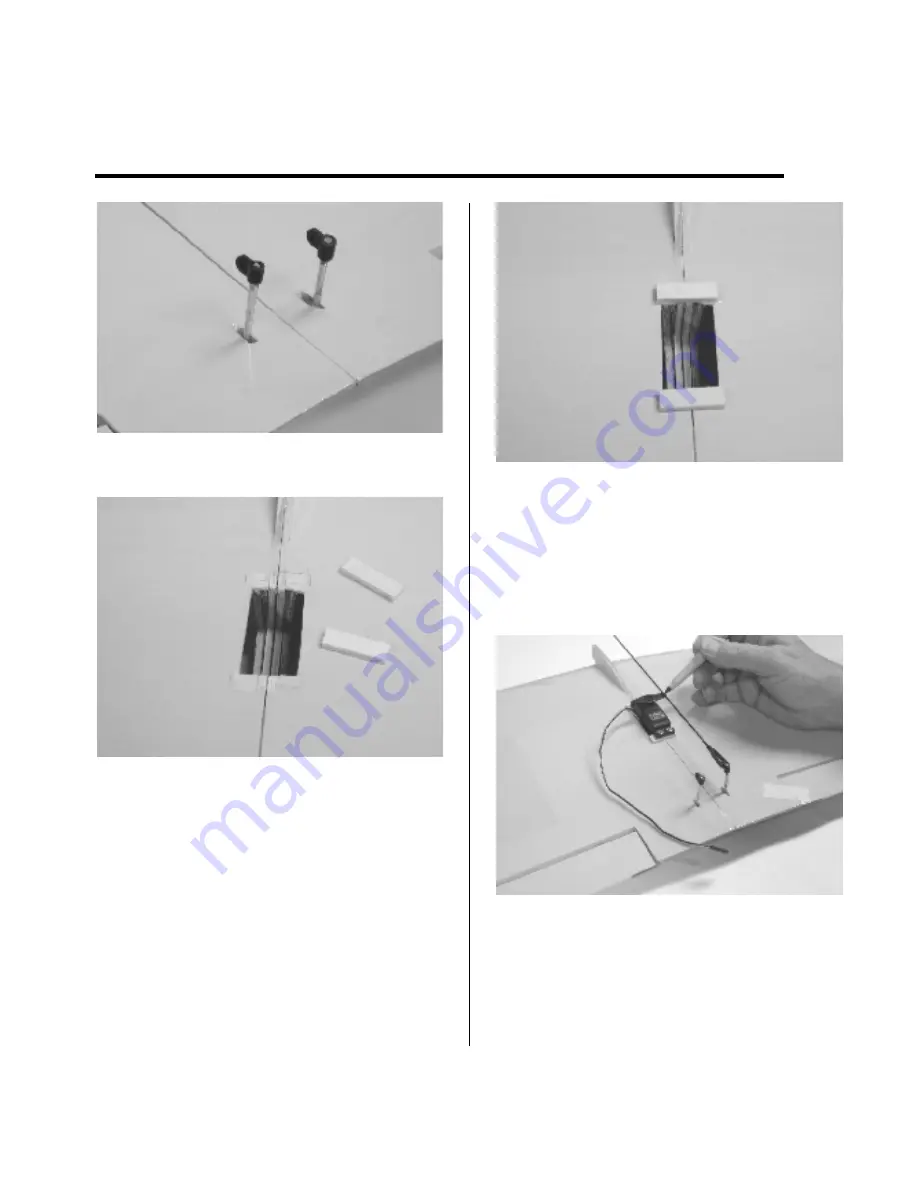
LANIER R/C
EXPLORER 40
ASSEMBLY
INSTRUCTIONS
4
12. Find the two pieces of wood, 1/8” x
5/16” x 1”. Lay one flush with the servo
well end and draw a line around it. Now
remove the covering within the lines. Do
the other end as well. Using thick CA, glue
the pieces in place, flush with the ends of
the servo well. When the servo is
mounted, the plywood pieces will add
material for the screws to anchor.
13. Locate the two aileron pushrods and
screw a clevis on each approx. half of the
exposed thread. Attach the clevis on one
to the control horn laying the end over the
servo output arm. Tape the ailerons in
neutral position.
14. Mark the length of the pushrod at the
hole in the servo output arm. Once
determined, bend the wire 90 degrees.
Trim off leaving a ¼” length after the
bend.