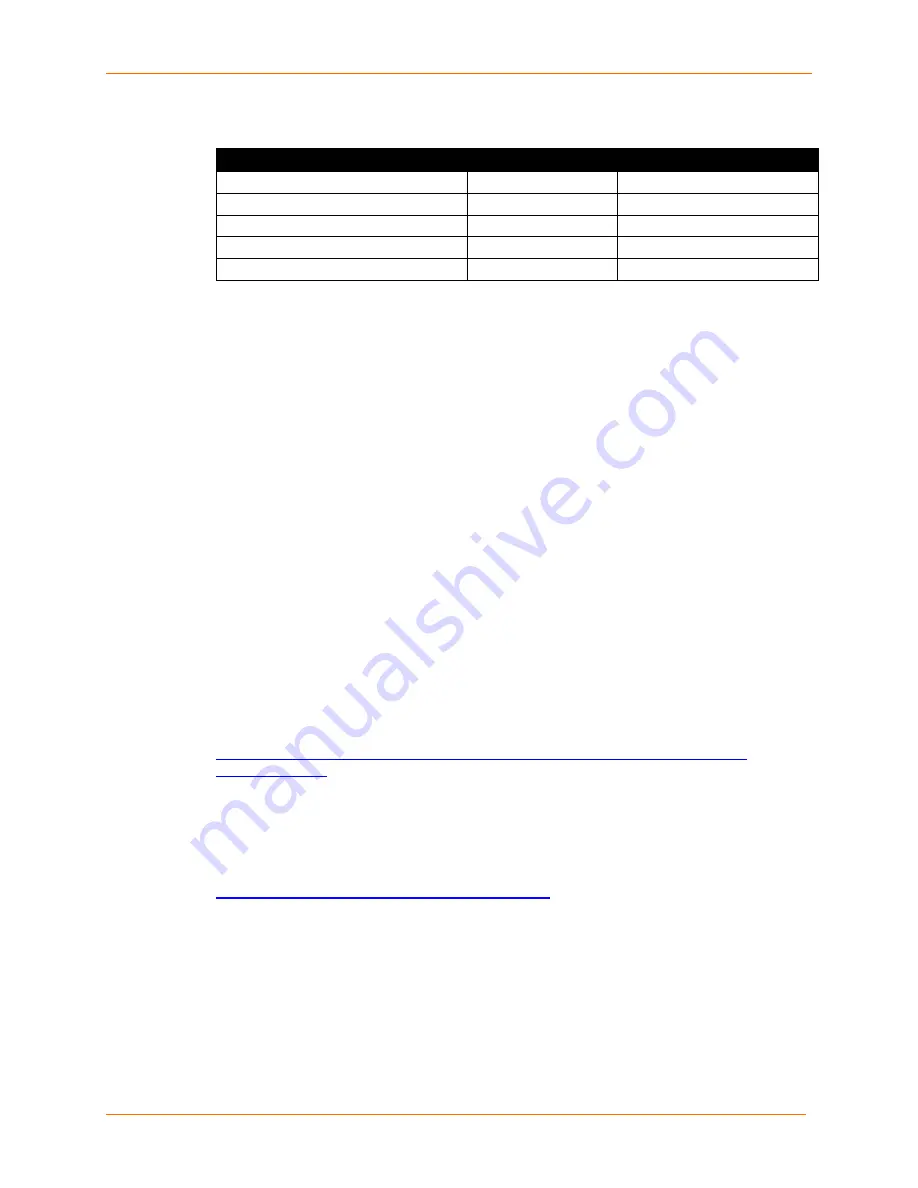
2: Functional Description
xPico® Embedded Device Server Integration Guide
22
Table 2-7 Recommended Magnetic Modules
and Combo RJ45/Magnetic Module Connectors
Type
Manufacturer
Part Number
Magnetic only (requires RJ45) BI-Tech
HS91-011-80LFTR
Magnetic only (requires RJ45)
Mingtek
HN0013SG
Combination RJ45/Magnetic
Belfuse
08B0-1D1T-06-F
Combination RJ45/Magnetic
Midcom
MIC2411D-0117T-LF3
Magnetic for POE
PULSE
HX2019
The Ethernet differential pair signals, ERX-/ERX+ and ETX-/ETX+ should be routed as
100-ohm differential pairs on a layer next to the signal ground plane. The use of vias on
these signals should be minimized. The center tap signal connections between the
magnetic and xPico (wired) module are required. Center tap signals RCT and TCT
should be routed with at least 20 mil trace thickness. The area between the magnetic
module and RJ45 jack, including the area under both, should be voided of all signals and
planes, except for the signals connecting to both. The signals connecting between the
RJ45 and magnetic are required to be isolated by 1500Vrms from all other signals and
planes, including chassis and signal ground. The connector shield should be connected
to chassis. It is recommended that 1206 resistor pads from chassis ground to signal
ground be placed next to each of the shield tabs. The resistor pads allow for 0 ohm
jumper, ferrite beads, or decoupling caps to be installed as needed for EMI/EMC
improvement.
The Ethernet LED signals should be routed to discrete LEDs or to the LED pins on the
RJ45 through 220 ohm or larger resistors. The LED signals are active low. The Ethernet
LED signals should be isolated from the signals that connect between the RJ45 and
magnetic module.
Also shown in the reference schematic is a recommended TVS array that can be used to
improve ESD and EFT in harsh environments. The device shown is Semtec
RCIamp0502A. This device features route through pin assignments allowing for the
Ethernet differential signal pairs to be routed without altering the trace impedance or
adding vias. Due to this routing, the device could be installed or depopulated as needed.
See the Lantronix app note
, How to Connect a Lantronix Embedded Module to a
Wired Ethernet Port
for more details on Ethernet connection and routing,
http://www.lantronix.com/pdf/appnotes/Connect-LTRX-Embed-Module-to-Wired-
Ethernet_AN.pdf.
The xPico module can also be powered from POE using a POE magnetic and POE
powered device controller. Lantronix uses the Silabs, Si3402 POE controller to power
the xPico development board via POE. If using POE the Ethernet magnetic module
should be changed to a POE compatible module such as Pulse HX2019.
Refer to the evaluation board schematic in the xPico-DevKit_UG for an example circuit.
http://www.lantronix.com/pdf/xPico-DevKit_UG.pdf
Refer to the SiLabs data sheet for Si3402 for more information on using the SiLabs POE
controller.