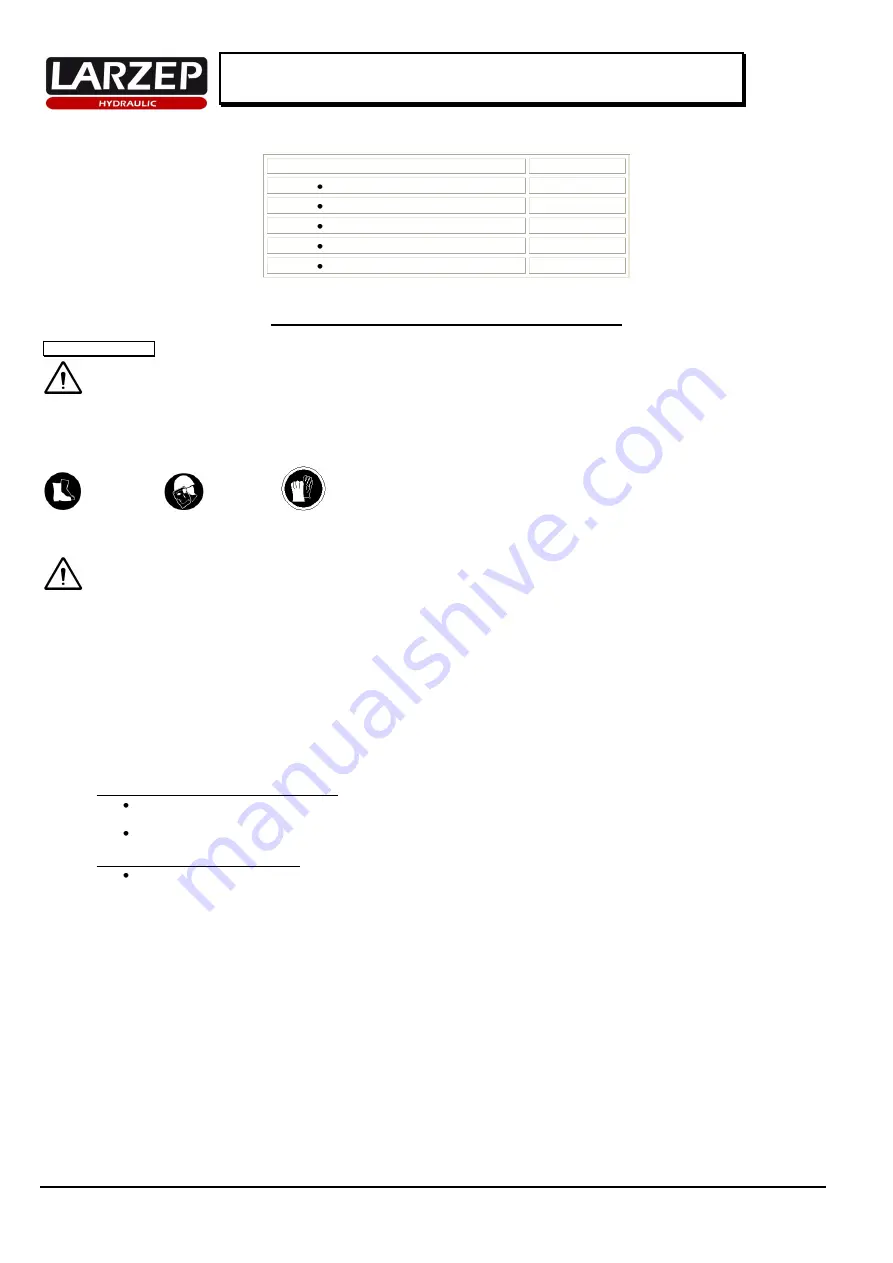
3
Instruction Manual
Column Press with Electric Pump “EE12018”
WELDED-MECHANIZED FRAME: mobile table and table’s anchorage by support in two bolts.
MODEL
EE12018
Working height maximum (mm)
910 mm
Working height minimum (mm)
80 mm
Displacement of the table (mm)
165 mm
Working Width (mm)
880 mm
Total weight (Kg)
750 Kg
3. ESSENTIAL SAFETY REQUIREMENTS.
DANGEROUS AREA
Due to the
FUNCTIONAL REASONS
it is considered to be the space between the columns, the bed and the hydraulic cylinder piston.
Due to the
MATERIAL PRESSED
it is supposed to be surrounding area to the machine in case of metal parts being ejected during pressing.
The speed of the hydraulic cylinder during its extension is less than 30 mm/second. Therefore then machine should be considered by the application of ANNEX V of
the Declaration of CE Conformity.
Operators standing in the dangerous area around the machine should protect their feet, faces and hands from metal pieces being ejected during pressing.
Feet protection
Face protection
Hands protection
Used materials and components are not for the health and safety of operators. The hand pump contains LARZEP hydraulic oil ISO: HV46.
HIDRAULIC OIL IS TOXIC IF IT ENTERS THE BLOODS STREAM. NEVER PLACE A FINGER OVER ANY ORIFICE OR LEAK, WHICH COULD
BE PRESSURIZED, SUCH AS THE HYDRAULIC LINE, AS THIS COULD CAUSE OIL TO BE INJECTED INTO BLOOD STREAM.
The start and stop devices are made by means of the commands located in the electric cabinet IP55.
The advance and return of the cylinder are made by means of a manual command located in the pump. The command acts over a directional valve.
The command is NOT maintaining drive, because due to the type of applications of the machine, the operator must put the hands over the material to be
treated, so the exposed personnel must know the machine’s function and the inherent risk of the equipment.
The electrical cabinet is provided with stopping and starting switches.
Only the starting switch, locate din the electrical cabinet, allows the feeding of the machine’s electrical organs.
To make its components movements, it will be necessary to act over the directional valve’s command.
The machine is provided with a red switch, locate din the electrical cabinet, that allows the total stop of the machine in safety conditions.
For a new start, it will be necessary to act the start switch, locate din the same electrical cabinet.
The stop of the cylinder is produce putting the command of the directional valve in position “C”.
The construction of machine has been calculated to bear without any breaking under conditions of foreseen utilization and for the whole life of the machine.
The hydraulic components have been designed and calculated in compliance with the ANSI B30.1, and have been proved to 875Kg./cm
of pressing.
The frame of the machine does not cause to be dangerous in that sense.
Mobile elements during the preparation phase:
The table can be displaced between the different points of anchorage. The table’s weight is 21,5 Kg. The personnel exposed will be protected
with safety shoes.
The EE12018 model is provided with a towing winch to displace the table. The frame is provided with two pins in the inferior angles of the
columns, which avoid the table’s fall to the ground in case of break of the towing winch’s cable.
Mobile elements during working phase:
The exposed personnel must put the directional valve’s command in position “C” or push the red switch of the electrical cabinet to stop the
advance of the hydraulic cylinder’s piston.
The machine is provided with a protective device for a motor in accordance to the rules: IEC 947-1, 947-2, 947-4-1.
The hydraulic pump is equipped with an internal security valve in the tank, out of operator’s control and rated at 700 Kg./ cm
.
Also, in the pump’s metal lid, there is a pressure regulation valve rated on factory at 700 Kg./ cm
and it could be rated by the operator, as we explained in
the start up chapter, from 0 till 700 Kg./ cm
.
All the maintenance operations must be performed while the machine is stopped avoiding this way any potentially dangerous situation. A poor maintenance
program of the press does not increase the risk, but obviously will revert in a lower performance.
The hydraulic pump is mounted out of the frame and access is very easy. To disassemble the pump unscrews the bolts in the tap cover. In order to
disassemble the cylinder it is required first to disassemble the hoses. Support the cylinder with a crane, by means of an eye bolt, and unscrew the joints of
the lid.
Release the cables of the terminal, to disconnect the electrical source, first disconnect the stud.
There are different positions of the distributor lever, it is labelled:
“A”: For the cylinder advance movement.
“C”: The piston does not advance, but the reached pressure is maintained.
“B”: The piston returns.