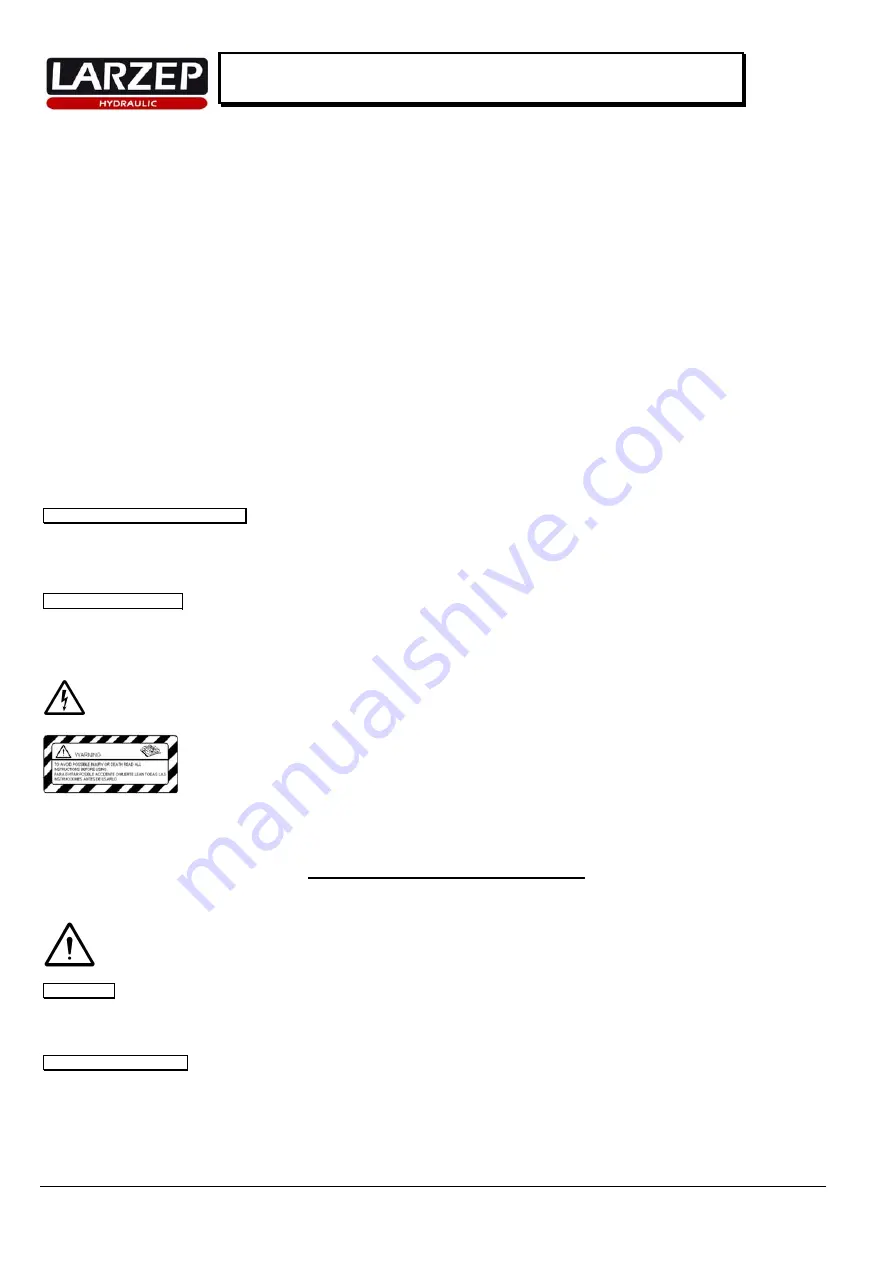
4
INSTRUCTION MANUAL
Column Press with Electrical Pump "EE25030-CE"
3.2 COMANDS
The electrical motor stop and start up devices, are done by means of a green button located in the electric cabinet.
The electrical cabinet it is provided with a general selector (1-0) in the lateral, and with an emergency red stop device, easily identifiable and operable.
The motor starts when we push the green button of the electrical cabinet.
The other commands are acting manually from de distributor valve located in the power pack.
The tension, not only the start device but also the emergency stop device, is 24 V.
3.3 SAFETY PREVENTIVE ACTIONS AGAINST MECHANICAL RISKS
The construction of machine has been calculated to bear without any breaking under conditions of foreseen utilization and for the whole life of the machine.
The hydraulic components have been designed and calculated in compliance with the ANSI B30.1, and have been proved to 875Kg./cm
²
of pressing.
The frame of the machine does not cause to be dangerous in that sense.
The hydraulic pump is equipped with an internal security valve in the tank, out of operator’s control and rated at 700 Kg./ cm
²
. The hydraulic cylinder is
also furnisher with a pressure relief valve, rated at 400 Kg./ cm
²
, which prevents the retraction chamber of the cylinder from overpressures in case of
obstruction of the return way.
Also, in the pump’s metal lid, there is a pressure regulation valve rated on factory at 700 Kg./ cm
²
and it could be rated by the operator, as we explained in
the start up chapter, from 0 till 700 Kg./ cm
²
.
3.4 MAINTENANCE
All the maintenance operations must be performed while the machine is stopped avoiding this way any potentially dangerous situation. A poor maintenance
program of the press does not increase the risk, but obviously will revert in a lower performance.
The hydraulic pump is mounted out of the frame and access is very easy. To disassemble the pump unscrews the bolts in the tap cover. In order to
disassemble the cylinder it is required first to disassemble the hoses. Support the cylinder with a crane, by means of an eye bolt, and unscrew the joints of
the lid.
ISOLATION OF THE POWER SUPPLY
Release the cables of the terminal, to disconnect the electrical source, first disconnect the stud.
3.5 INDICATIONS
INFORMATION DEVICES
There are different positions of the distributor lever, it is labelled:
“A”: For the cylinder advance movement.
“C”: The piston does not advance, but the reached pressure is maintained.
“B”: The piston returns.
The labels of protection, and the label of risk of electrical current.
and advice of reading instructions
The press, the cylinder and the pump have their corresponding serial numbers marked on them. In addition to it, you can find a sticker label showing the commercial
reference, capacity, working pressure, name and address of the manufacturer.
4. TRANSPORT AND ERECTION.
The machine is delivered properly packed in a wooden ballet. For it’s handling, it is recommended to use a forklift truck or a crane. In the last case, it is necessary to
use the eye bolt threaded in the cylinder’s head. When doing this operation, you should be cautious and prevent the flexible hoses and couplings from any damage.
OIL FILLING
Usually, the equipment is provided with filled tank. In case that the tank was empty, it must be filled, checking the level of the oil by means of the filling plug.
Approximately 65 Litres to complete the tank.
INSTALLING THE GAUGE
1-Replace the threaded tap in the right column by the gauge, which is supplied separately.
2-Tighten the gauge cone to the gauge adaptor seat by using a flan wrench size 22.
3-Hold the gauge screen by hand during threading process and after reaching a comfortable reading position set the gauge screen free so that it turns the last quarter
solidarily with the thread.
4- The hydraulic system also includes a gauge adaptor with 3/8 “ BSP thread.
The machine is stable enough to operate without fixing, but if is placed in an area commonly operated by mobile machinery (cranes,
lifting equipment…) it is strongly recommended to fix it to the desired place by drilling the supporting plates.
Summary of Contents for EE25030-CE
Page 7: ...7 INSTRUCTION MANUAL Column Press with Electrical Pump EE25030 CE 8 DECLARATION OF CONFORMITY ...
Page 8: ...8 INSTRUCTION MANUAL Column Press with Electrical Pump EE25030 CE ...
Page 9: ...9 INSTRUCTION MANUAL Column Press with Electrical Pump EE25030 CE ...
Page 10: ...10 INSTRUCTION MANUAL Column Press with Electrical Pump EE25030 CE ...
Page 11: ...11 INSTRUCTION MANUAL Column Press with Electrical Pump EE25030 CE ...
Page 12: ...12 INSTRUCTION MANUAL Column Press with Electrical Pump EE25030 CE ...
Page 13: ...13 INSTRUCTION MANUAL Column Press with Electrical Pump EE25030 CE ...