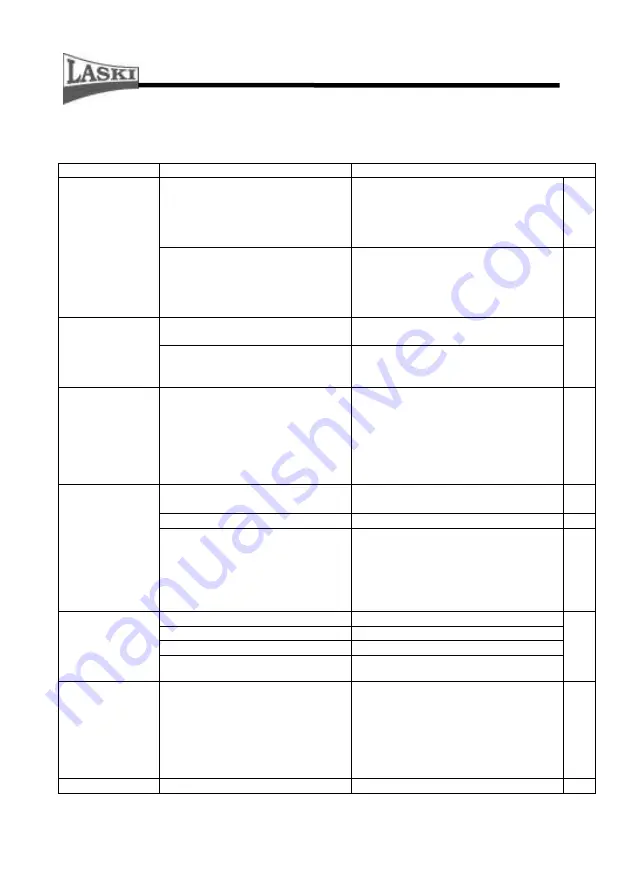
Trencher TR 120 H
40
Failures and Troubleshooting
Failure
Cause
Remedy
Engine does not
start however it is
possible to crank
it by starter
Lack of fuel in fuel tank
Refill
Check up the entire fuel system:
- fuel supply line
- primary fuel filter
- fuel filter
Insufficient compression stroke:
- wrong valve clearance
- wear of valves
- wear of cylinders and/or piston
rings
Check valve clearance and adjust it if
needed
Problematic
starting at low
temperatures
Too low speed at starting
Change engine oil and refer to its proper
viscosity
SE
RVI
CE
- solid oil
- battery insufficiently charged
- use recommended oil sorts only
- recharge battery
- resp. contact authorised service point
Starter does not
turn on, resp.
engine does not
crank
Failure of electric equipment:
- loose connection of battery and/or
wiring
- oxidized contacts
- discharged or faulty battery
- starter failure
- failure of relay or controls
Check up electric equipment and
particular components
SE
RVI
CE
Engine roars to
life but does not
run after starter
disconnection
Speed regulator lever not sufficiently
in START position
Set the lever to START
Fuel filter fouled
Change
- fuel supply line broken
- error indication in connection with
automatic controls
- low oil pressure
- fouled filter
- faulty alternator
- check up entire fuel system
- check up oil level
- check up filter and clean or replace it as
needed
- see Engine Manual
SE
RVI
CE
Engine turns off
Lack of fuel
Refill
SE
RVI
CE
Fuel pre-filter or fuel filter fouled
Check and replace as needed
Belt on cooling fan broken
Change
Mechanical failure
Check and remedy
Insufficient
engine power
Insufficient fuel supply:
- lack of fuel
- fuel filter fouled
- insufficient fuel tank venting
- fuel line leakage
- speed regulator lever does not
remain in required position
- refill
- change filter
- check and remedy
- check and remedy
- unblock
Insufficient
Air filter fouled
Clean filter or replace it as needed
Summary of Contents for TRENCHER TR 120H
Page 1: ... Version 10 2019 1 z 48 OPERATING INSTRUCTIONS TRENCHER TR 120 Model TR 120H ...
Page 5: ...Trencher TR 120 H 5 ...
Page 6: ...Trencher TR 120 H 6 ...
Page 42: ...Trencher TR 120 H 42 ELECTRIC CIRCUITRY ...
Page 43: ...Trencher TR 120 H 43 HYDRAULICS ...
Page 45: ...Trencher TR 120 H 45 Service Report ...
Page 46: ...Trencher TR 120 H 46 Service Report ...