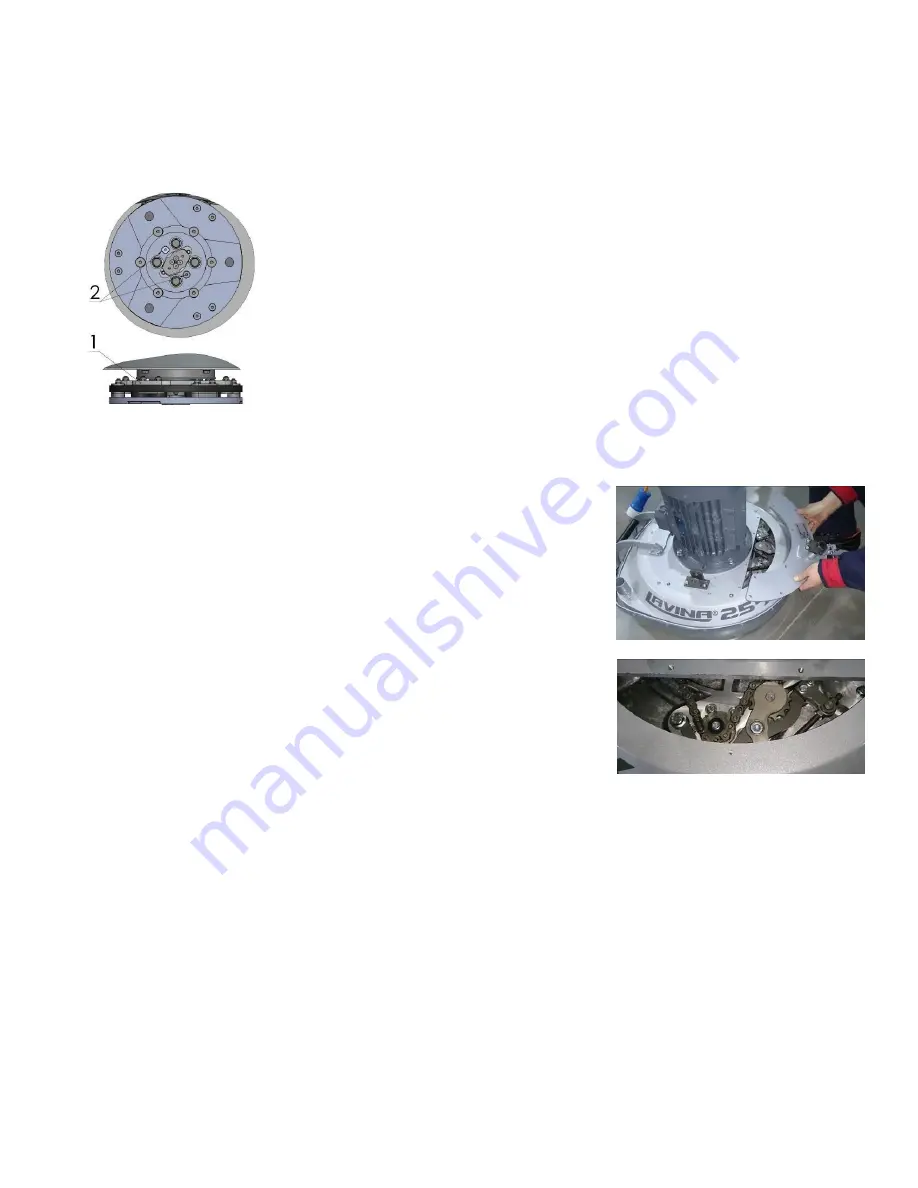
Superabrasive
User Manual
Original Language
Lavina® 25-X
9/2018
13
7. MAINTENANCE AND INSPECTION
CLEANING
Keep your machine clean. Cleaning the machine on a regular basis will help detect and solve potential problems before they can cause
damage to the machine. Most importantly, check and clean the tool plate connections, power cords, plugs, vacuum hoses, and water
tank.
CHECK DAILY
After operating the Lavina®X machine, the operator should conduct a visual inspection of the
machine. Any defect should be solved immediately. Pay attention to power cords, plugs, vacuum
hoses, loose bolts or screws.
Tool holders: Buffers and elastic element are consumables and must be visually checked on a daily
basis and replaced if necessary. Make sure the flanges or discs are securely locked in place. The key
lock holders (butterflies) should also be checked.
Check the rubber buffers and make sure the holders are secure. The flange holding the buffers
(Fig.7.1‐1) has to be firmly secured to the unit. If there is a gap seen here, that means the screws
securing the holder are loose. The screws have to be tightened immediately to safely operate the
machine. Working with loose screws could cause serious damage to the machine. The tightening force
of the screws has to be 22‐25N.m (16‐18ft∙lbf).
It is very important to regularly check the screws that secure the “QuickChange” holder to the
Figure
7.1
safety part (Fig.7.1‐ 2), so that the holder will not fly away if the buffers get damaged. The
“QuickChange” should also be cleaned.
.
CHECK EVERY 200 WORKING HOURS
Every 200 working hours, the operator should inspect all parts of the machine carefully.
Most importantly, inspect and clean the tool plate connections, power cord plugs,
vacuum hoses and water tank/filter. Also, check the water flow of the pump. Check the
guard assembly. Ensure the wheels are clean and rotate properly. Inspect the control
buttons. If there are defective control parts, they should be replaced immediately.
Replace any worn vacuum or water hoses.
Open the service cover on the motor base (Fig 7.2) (Fig 7.3) to check the
planetary chain. Lubricate the chain with chain lubricant and correct the sag if needed.
(For sagging correction see TROUBLESHOOTING 8.4)
Dismount the tool holders (See TROUBLESHOOTING) and replace any parts
(elastic element, buffers, sealer caps, “O” rings) showing any damage.
CHECK EVERY 400 WORKING HOURS
In addition to checks made every 200 working hours, replace sealer and V‐rings as described in chapter “TROUBLESHOOTING ‐
DISMOUNTING TOOL HOLDERS TO CHANGING V‐RINGS AND FELT‐RINGS.
VACUUM
As stated previously, frequently check hoses and other parts for clogging.
WATER LEAKS
Leaking parts should be replaced immediately because the water could damage your machine.
.
MECHANICAL PARTS
Parts such as the belts, seal rings, cap rings, spiders, buffers and guard assembly are subject to wear and must be replaced as needed.
ELECTRICAL SYSTEM
Dust should not enter the control box, as it will destroy the controls. Remove (blow out) any dust present.
Figure 7.1
Figure 7.3
Figure 7.2