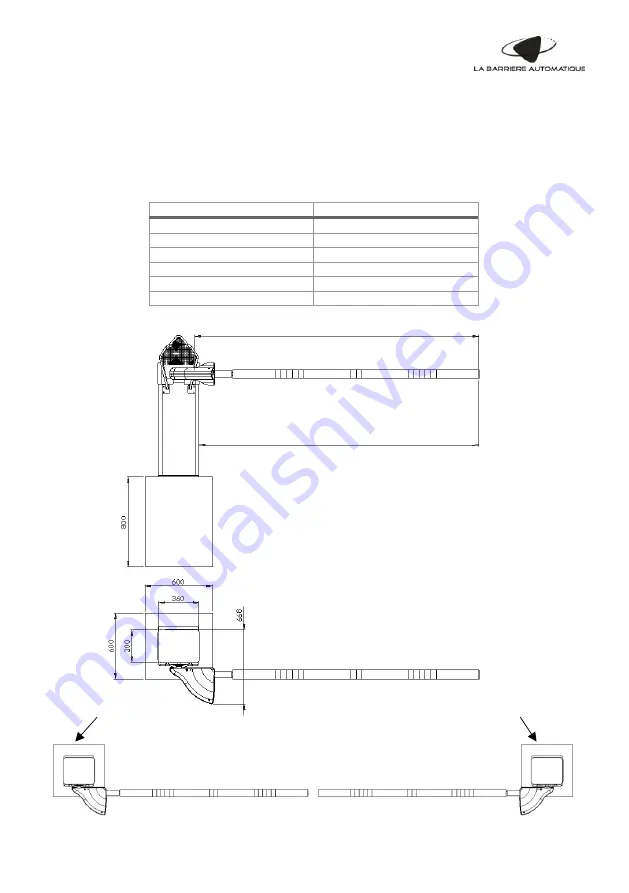
Operating Instructions
– LBA63 TOLL HIGHWAYS – 2019 Version
13
4
Technical data
4.1
Dimensions and directions
Maximum boom length: 3m50
The various possible boom lengths are as follows:
Passage length (mm)
Boom length X (mm)
1560
1700
1800
1940
2720
2860
3000
3140
3160
3300
3360
3500
Normal direction
Reverse direction
Hatch
Hatch
Boom length = X
Passage length = X - 140 mm