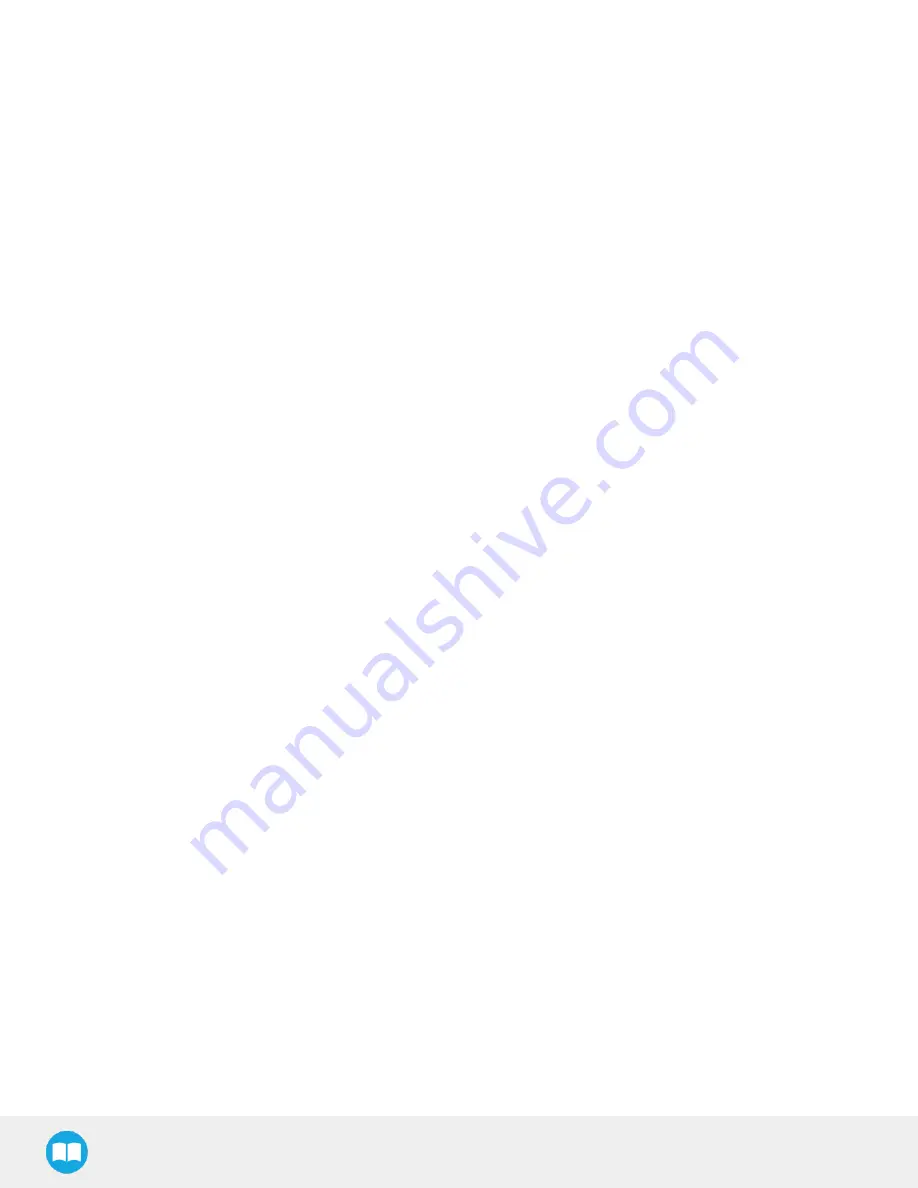
2F-85 & 2F-140 - Instruction Manual
Robotiq shall not be liable for damages resulting from the use of the Robotiq 2-Finger Adaptive Robot Gripper, nor shall Robotiq be
responsible for any failure in the performance of other items to which the 2-Finger Adaptive Robot Gripper is connected or the
operation of any system of which the Gripper may be a part.
9.1. I/O Coupling Warranty
Robotiq warrants the I/O Coupling against defects in material and workmanship for a period of one year from the date of reception
when utilized as intended. Robotiq also warrants that this equipment will meet applicable specifications under normal use.
146