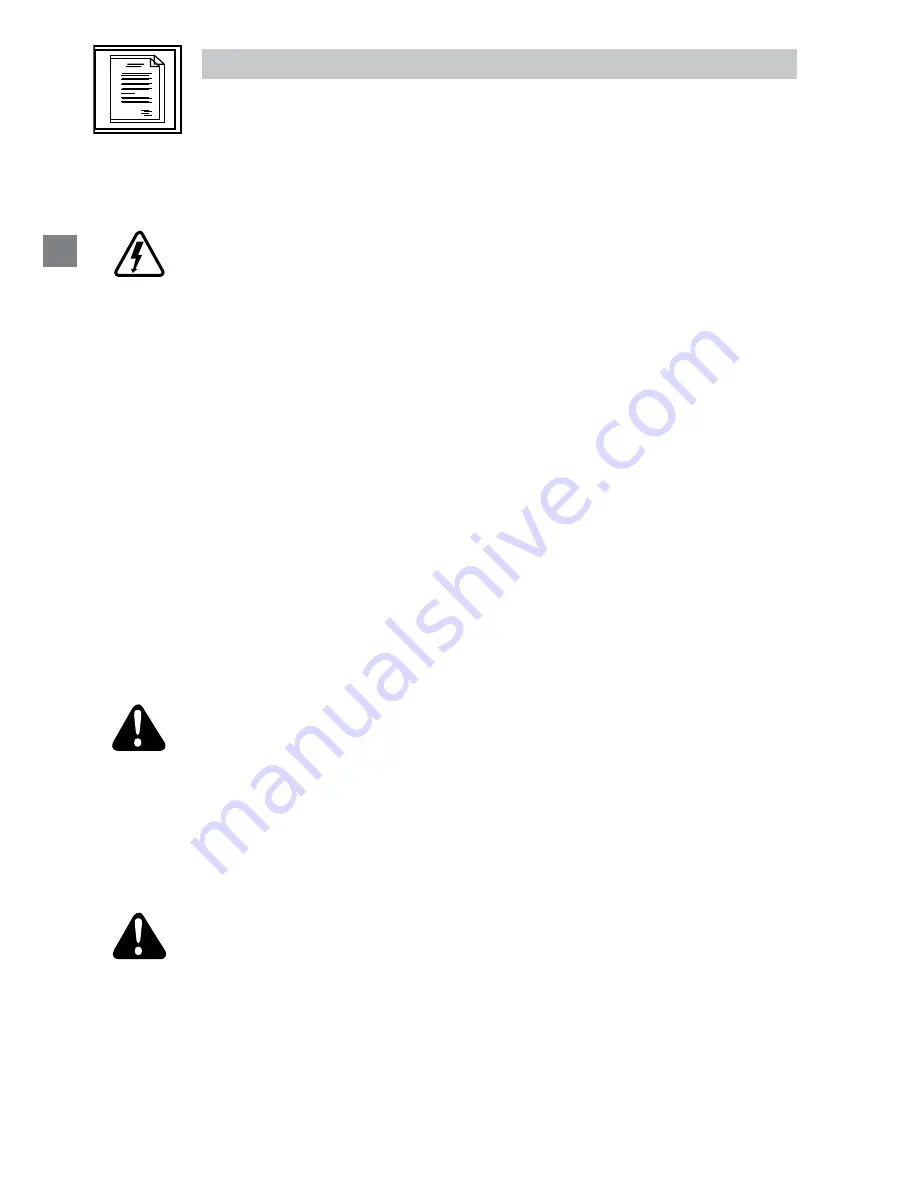
1
Safety information
General
DANGER!
Some parts of LEESON controllers can be electrically live and some surfaces
can be hot.
Non-authorized removal of the required cover, inappropriate use, and incorrect installation or
operation creates the risk of serious injury to personnel or damage to equipment.
All operations concerning transport, installation, and commissioning as well as maintenance must be
carried out by qualified, skilled personnel who are familiar with the installation, assembly, commissioning,
and operation of variable frequency drives and the application for which it is being used.
Installation
Ensure proper handling and avoid excessive mechanical stress. Do not bend any components and
do not change any insulation distances during transport, handling, installation or maintenance.
Do not touch any electronic components or contacts. This drive contains electrostatically sensitive
components, which can easily be damaged by inappropriate handling. Static control precautions
must be adhered to during installation, testing, service and repair of this drive and associated
options. Component damage may result if proper procedures are not followed.
This drive has been tested by Underwriters Laboratory (UL) and is an approved component in
compliance with UL508 Safety Standard.
This drive must be installed and configured in accordance with both national and international
standards. Local codes and regulations take precedence over recommendations provided in this
and other LEESON documentation.
The SM2 and SM4 Vector drive is considered a component for integration into a machine or process.
It is neither a machine nor a device ready for use in accordance with European directives (reference
machinery directive and electromagnetic compatibility directive).
It is the responsibility of the end
user to ensure that the machine meets the applicable standards.
Electrical connection
WARNING!
When working on live drive controllers, applicable national safety regulations must
be observed.
The electrical installation must be carried out according to the appropriate regulations (e.g.
cable cross-sections, fuses, protective earth [PE] connection). While this document makes
recommendations in regard to these items, national and local codes must be adhered to.
The documentation contains information about installation in compliance with EMC (shielding,
grounding, filters and cables). These notes must also be observed for CE-marked controllers.
The manufacturer of the system or machine is responsible for compliance with the required limit
values demanded by EMC legislation.
Application
WARNING!
The drive must not be used as a safety device for machines where there is a
risk of personal injury or material damage. Emergency Stops, over-speed
protection, acceleration and deceleration limits, etc. must be made by other
devices to ensure operation under all conditions.
The drive features many protection devices which are aimed at protecting the drive and the driven
equipment by generating a fault and shutting the drive and motor down by removing power. Mains
power variances can also result in shutdown of the drive. When the fault condition disappears or is
cleared, the drive can be configured to automatically restart.
It is the responsibility of the user and/
or OEM and/or integrator to ensure that the drive is configured for safe operation.
4
Safety information
CALL NOW 800-985-6929
http://www.automatedpt.com
Email: charles@automatedpt.com
CALL NOW 800-985-6929
http://www.automatedpt.com
Email: charles@automatedpt.com