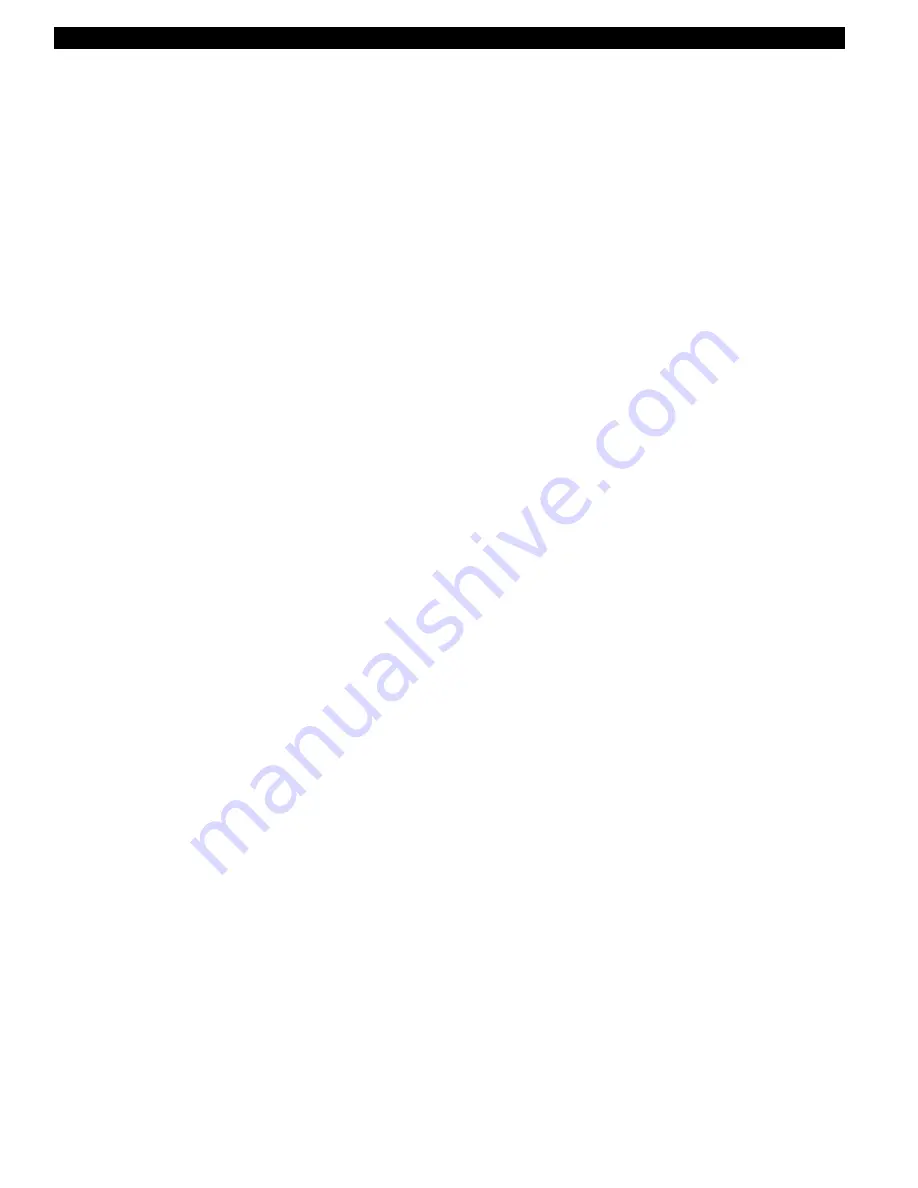
16
MAINTENANCE & SERVICE (DC-3000 & DC-4000)
SPRAY GUN:
The filter should be cleaned or replaced after each use to
minimize tip clogging problems. If the gun valve becomes
worn and begins to leak, it should be replaced. See page
25 for overhaul details.
SPRAY TIP:
The spray tip is one of the most important elements in
producing a quality spray job. It requires periodic re-
placement (every 50-200 gallons) to maintain perform-
ance and to prevent overworking the pump (see page 8
for details).
CHANGING GEAR OIL (DC-4000):
1) Turn unit off, ensure prime valve is open, and all
pressure is relieved. Unplug from electrical outlet.
2) Remove oil drain plug from underside of speed
reducer.
3) Remove oil fill/vent cap from top of speed reducer.
4.
Allow old oil to drain. Replace drain plug.
5) Fill unit with 200 ml of EP 90 gear oil, part no. L034-
124. Do not overfill!
6) Replace vent cap. Unit is now ready for use.
Repeat each 500 hr or at each packing replacement.
GREASE CENTRAL BODY (DC-4000):
1) Turn unit off, ensure prime valve is open, and all
pressure is relieved.
2) Using a grease gun with normal automotive grease,
pump 2-5 strokes into nipple on front of central body.
Some guns may require removal of pail hook using
5mm allen key.
3) Repeat every 100-200 hour and at each packing
change.
CLEAN COOLING FAN (DC-4000):
1) Turn unit off, ensure prime valve is open, and all
pressure is relieved. Unplug from electrical outlet.
2) Remove the 3 x screw from fan cover.
3) Scrape fan, back of motor and inside of cover clean.
Clean exterior of motor with wire brush or scraping.
4) Replace cover and screws.
This is to be done “on condition” ie; if fan and motor look
dirty, it is time for cleaning. A clean fan and motor run
cooler and last longer!
BRUSH INSPECTION AND REPLACEMENT (DC-4000):
NOTE: Check every 500 hr or at packing replace-
ment. Failure to replace worn brushes will reduce
unit performance and drastically shorten motor life.
1) Turn unit off, ensure prime valve is open, and all
pressure is relieved. Unplug from electrical outlet.
2) Remove brush caps from side of motor and remove
brushes. Keep note of which side of motor and which
side up brushes are.
3) Measure length of rectangular part of brush. If 15mm
or longer, brush is in near new condition. If 13-15mm,
replacement should be seriously considered. If 13mm
or shorter, brushes MUST be replaced or motor
damage may occur.
4) Blow out motor through brush holes with compressed
air.
5) Install brushes. If re-using old brushes, put back on
same side of motor, same way up as before to reduce
break-in time.
6) Install brush caps.
DO NOT OVERTIGHTEN, AS
BRUSH CAPS ARE BAKELITE AND WILL BREAK!
7) Put unit in solvent, open prime valve, and run unit at
low priming speed for approximately 5 minutes to
break in brushes.
LOWER PACKINGS:
No regular service required.
The lower packings of this unit are stationary, so that the
only wearing part is the piston. Costly replacing of the
pump cylinder is eliminated. The packings are self adjust-
ing, and will generally outlast the upper packings. Both
sets are included in the packing kit, and should be
changed together for best reliability and performance.
UPPER PACKINGS:
Lubricate daily with L034-125 oil.
The upper packings are adjusted manually, by turning the
brass packing nut to the left, ie; clockwise as viewed from
the top. Keep guard in place during operation.
IMPORTANT NOTE: The packings should never be
over tightened, as this greatly reduces packing and
piston life. Never tighten packings with pressure in
unit, as a false indication of adjustment will result. A
bit of gummy buildup around the packing nut is
normal and should be periodically removed with a
brush and solvent. This allows lubricant oil to reach
packings.
NOTE: Do not adjust packing while unit is running.
Fingers, tools, etc. can be trapped between plunger
and packing nut. Loss of finger or serious injury
could result.
TO TIGHTEN UPPER PACKINGS:
1) Turn unit off, ensure prime valve is open, and all
pressure is relieved. Unplug from electrical outlet.
2) Remove all buildup from around packing nut.
3) Using a hammer and srewdriver, turn packing nut
clockwise a maximum of 1/8 turn. Packings should be
only tightened just enough to stop leakage. See
notice above. Gentle tightening is normally sufficient.
4) Lubricate packings using L034-125 oil.
5) Replace safety shield over packing area.
NOTE: When no further adjustment of packings is
possible, the nut will be difficult to turn with reason-
able effort. Packings should be replaced.
CHECK VALVES:
These pumps has two valves, the footvalve at the paint inlet,
and the shaft valve in the center of the piston. Both are of
stainless steel ball, tungsten seat construction. This means that
inexpensive, easily replaced balls are the normal wear point. If
the unit will not draw up paint, the footvalve may be stuck.
Simply tapping on the side of the footvalve with a wrench will
usually suffice. Should this not work, the following steps will
show you how to remove and clean the footvalve and check
the shaft valve. For shaftvalve disassembly, please see steps
1-12, 16, 17 of packing instructions for the DC-4000.