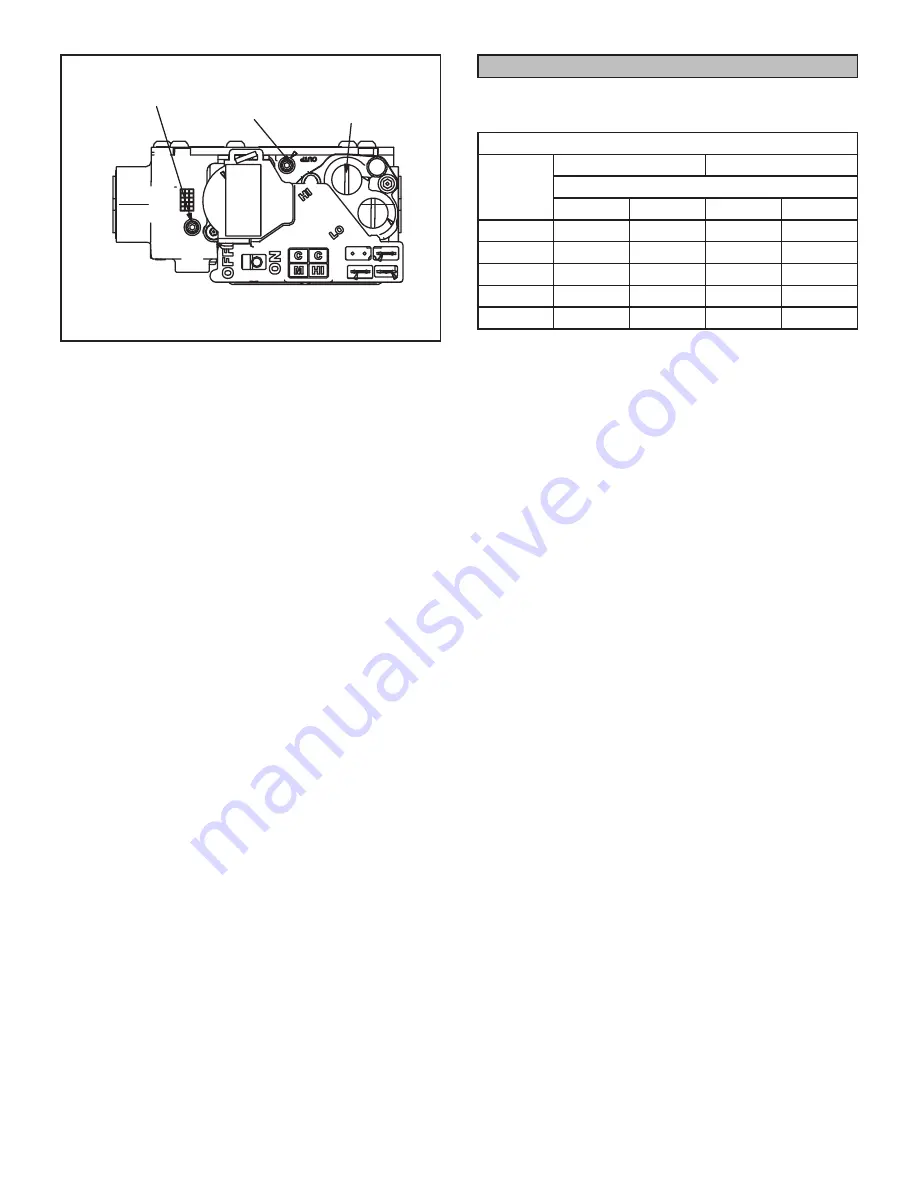
Page 30
GAS VALVE SHOWN IN ON POSITION
INLET PRESSURE POST
HIGH FIRE ADJUSTMENT
SCREW
(under cap)
MANIFOLD
PRESSURE TAP
WHITE RODGERS GAS VALVE
FIGURE 31
8 - Move switch on gas valve to ON. Do not force. See
figure 31.
9 - Replace the upper access panel.
10 - Turn on all electrical power to to the unit.
11 - Set the thermostat to desired setting.
NOTE -
When unit is initially started, steps 1 through 11
may need to be repeated to purge air from gas line.
12 -
If the appliance will not operate, follow the
instructions “Turning Off Gas to Unit” and call your
service technician or gas supplier.
Turning Off Gas to Unit
1 - Set the thermostat to the lowest setting.
2 - Turn off all electrical power to the unit if service is to
be performed.
3 - Remove the upper access panel.
4 - Move switch on gas valve to OFF. Do not force.
5 - Replace the upper access panel.
Failure To Operate
If the unit fails to operate, check the following:
1 - Is the thermostat calling for heat?
2 - Are access panels securely in place?
3 - Is the main disconnect switch closed?
4 - Is there a blown fuse or tripped circuit breaker?
5 -
Is the filter dirty or plugged? Dirty or plugged filters
will cause the limit control to shut the unit off.
6 - Is gas turned on at the meter?
7 - Is the manual main shut-off valve open?
8 - Is the gas valve ON/OFF switch in the ON position?
9 - Is the unit ignition system in lock out? If the unit locks
out again, call the service technician to inspect the
unit for blockages.
10 -
Is pressure switch closed? Obstructed flue will
cause unit to shut off at pressure switch. Check flue
and outlet for blockages.
11 -
Are flame rollout switches tripped? If flame rollout
switches are tripped, call the service technician for
inspection.
Gas Pressure Adjustment
Gas Flow (Approximate)
TABLE 9
GAS METERING CLOCKING CHART
EL280
Unit
Natural 1000 btu/cu ft
LP 2500 btu cu/cu ft
Seconds For One Revolution
1 cu ft dial 2 cu fr dial 1 cu ft Dial 2 cu ft Dial
-045
80
160
200
400
-070
55
110
136
272
-090
41
82
102
204
-110
33
66
82
164
-135
27
54
68
136
Furnace should operate at least 5 minutes before check-
ing gas flow. Determine time in seconds for two revolu
-
tions of gas through the meter. (Two revolutions assures
a more accurate time.) Divide by two and compare to time
in table 9 below. If manifold pressure matches table 11
and rate is incorrect, check gas orifices for proper size and
restriction. Remove temporary gas meter if installed.
NOTE -
To obtain accurate reading, shut off all other gas
appliances connected to meter.
Supply Pressure Measurement
An inlet post located on the gas valve provides access
to the supply pressure. See figure 31. Back out the 3/32”
hex screw one turn, connect a piece of 5/16” tubing and
connect to a manometer to measure supply pressure. See
table 11 for supply line pressure.
Manifold Pressure
A manifold pressure post located on the gas valve pro-
vides access to the manifold pressure. See figure 3
1.
Back out the 3/32 hex screw one turn, connect a piece
of 5/16” tubing and connect to a manometer to measure
manifold pressure.
NOTE -
Pressure test adapter kit (10L34) is available from
Lennox to facilitate manifold pressure measurement.
1 -
Connect test gauge to manifold pressure post
(figure 31) gas valve.
2 -
Ignite unit on high fire and let run for 5 minutes to
allow for steady state conditions.
3 -
After allowing unit to stabilize for 5 minutes, record
manifold pressure and compare to value given in table
11.
4 - If necessary, make adjustments. Figure 31 shows
location of high fire adjustment screw.
5 -
If an adjustment is made on high fire, re-check
manifold pressure on low fire. Do not adjust low fire
manifold pressure. If low fire manifold pressure is
more than 1/2” above or below value specified in
table 11, replace valve.
6 - soon as an accurate reading has been obtained.
Turn the supply and manifold 3/32” hex screw one
revolution back into the gas valve.
7 - Start unit and perform leak check. Seal leaks if
found.