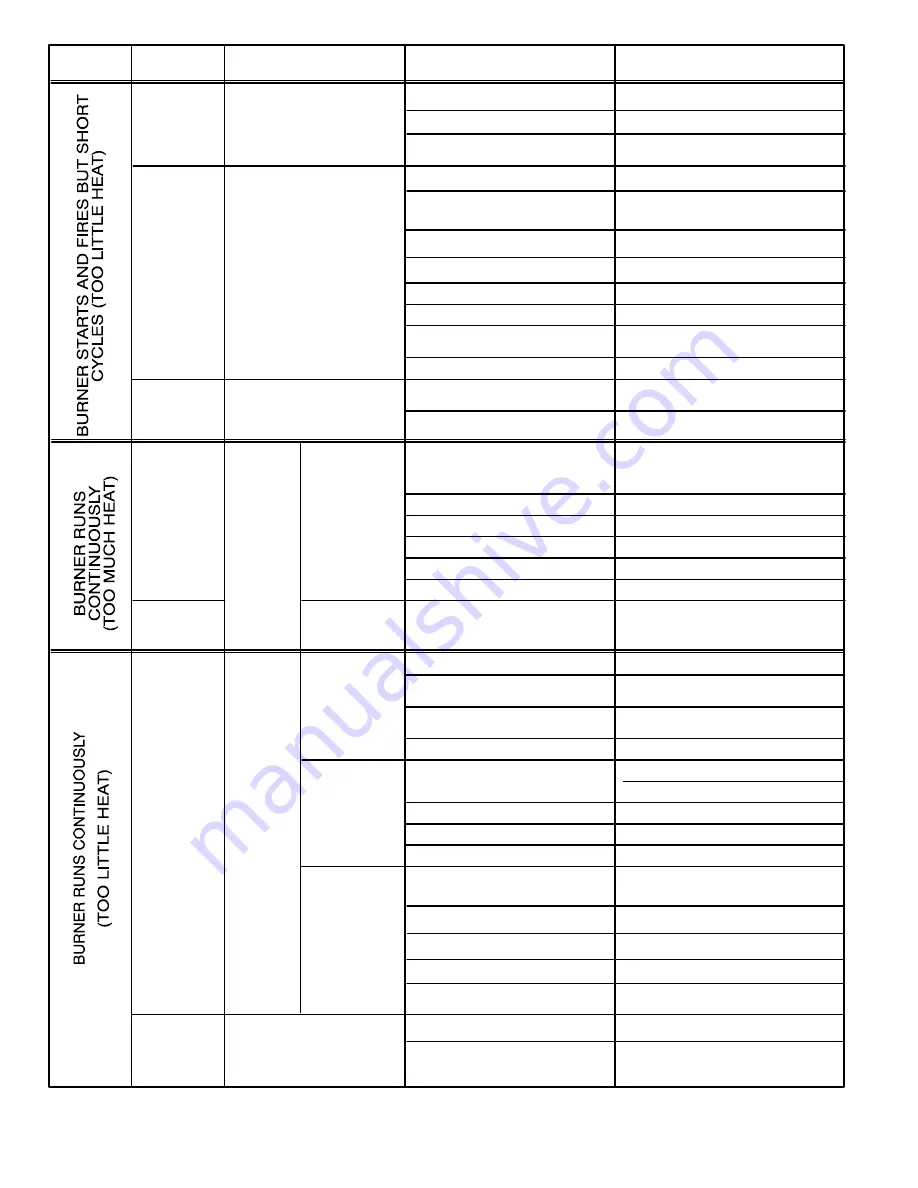
Page 28
Partially plugged or defective nozzle.
Oil pressure too low, less than
140 (965.3 kPa) psi.
Stuck thermostat bimetal.
Thermostat not level.
Shorted thermostat wires.
Thermostat out of calibration.
Thermostat in cold draft.
Defective primary control.
Too much combustion air.
Excessive draft.
Incorrect burner head adjustment.
Dirty or plugged heat exchanger.
Insufficient draft.
Incorrect burner head adjustment.
Too little combustion air.
Too little blower air.
Dirty or plugged heat exchanger.
Dirty blower wheel.
Dirty furnace air filters.
Restricted or closed registers or
dampers.
Heat anticipator set too low.
Vibration at thermostat.
Replace with properly rotating wheel.
TROUBLE SOURCE
PROCEDURE
CAUSES
CORRECTION
THERMOSTAT
LIMIT
CONTROL
POWER
PRIMARY
CONTROL
THERMOSTAT
COMBUSTION
OIL
PRESSURE
Check thermostat.
Connect voltmeter between
line voltage connections to
primary control (black & white
leads). If burner cycles due to
power interruption, it's cycling
off limit.
If voltage fluctuates, fault is in
the power source. Recheck
voltage at power source.
Disconnect
thermostat
wires at
primary
control.
If burner turns
off, fault is in
thermostat
circuit.
If burner does not
turn off, fault is in
primary control.
Check burner
combustion
for CO
2
,
stack
temperature
& smoke.
Inspect fire and check oil
pressure.
Thermostat in warm air draft.
Dirty furnace air filters.
Blower running too slow.
Blower motor seized or burned out.
Blower wheel in backwards.
Wrong motor rotation.
Restrictions in return or supply air
system.
Adjustable limit control set too low.
Correct heat anticipator setting.
Correct source of vibration.
Shield thermostat from draft or
relocate.
Clean or replace filter.
Increase blower speed to maintain
proper temp. rise.
Replace motor.
Clean blower wheel.
Reverse blower wheel.
Correct cause of restriction.
Blower wheel dirty.
Reset limt to maximum stop setting.
Loose wiring connection.
Low or fluctuating line voltage.
Locate and secure connection.
Call power company.
Shorted or welded thermostat
contacts.
Repair or replace thermostat.
Clear obstruction or replace thermostat.
Level thermostat.
Repair short or replace wires.
Replace thermostat.
Correct draft or relocate thermostat.
Replace defective primary control.
Low CO
2
less
than 10%.
High smoke
reading more
than a trace.
High stack
temperature
more than
550
F (288
C)
Net.
Reduce combustion air.
Air leaks into heat exchanger around
inspection door, etc.
Correct cause of air leak.
Adjust barometeric damper for correct
draft.
Correct burner head setting.
Clean heat exchanger.
Readjust burner.
Increase blower speed to maintain
proper temp. rise.
Increase draft.
Correct burner setting.
Increase combustion air.
Readjust registers or dampers.
Clean or replace filter.
Clean blower wheel.
Clean heat exchanger.
Replace nozzle.
Increase oil pressure to 140 psi
(965.3 kPa).