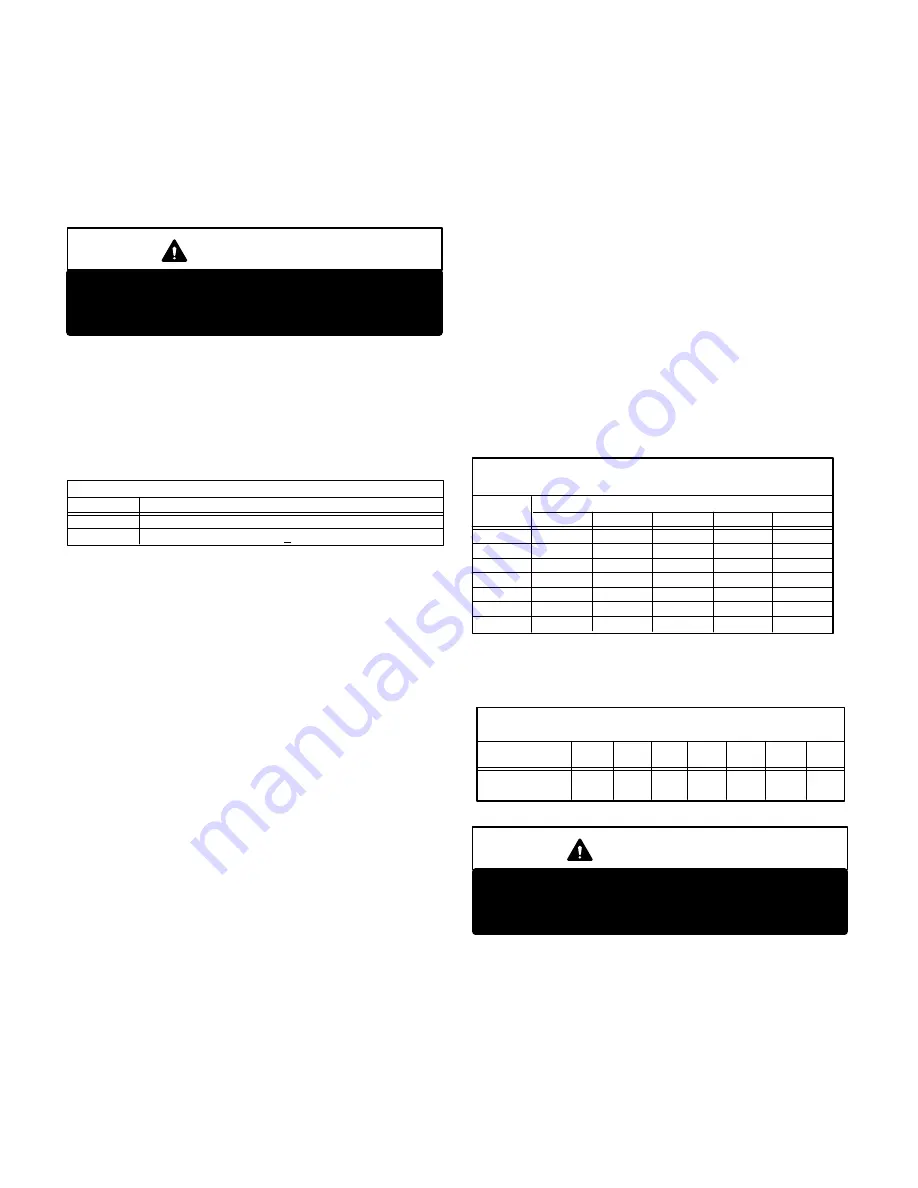
Page 8
E – Check Manifold Pressure
After line pressure has been checked and adjusted,
check manifold pressure. Move pressure gauge to out-
let pressure tap located on unit gas valve (GV1). See
figure 6 for location of pressure tap on gas valve.
IMPORTANT
For safety, connect a shut-off valve between the
manometer and the gas tap to permit shut off of
gas pressure to the manometer.
The gas valve is factory set and should not require ad-
justment. All gas valves are factory regulated. See
table 5 . See tables 6 and 7 for derated manifold pres-
sure values in high altitude application for natural and
LP gases.
Operating Pressure (outlet) in. W.C.
TABLE 5
GAS VALVE REGULATION
3.5 +0 –0.3
Natural
L.P.
9.5 + 0.5
Unit (Fuel)
Manifold Adjustment Procedure:
1 – Connect a test gauge to outlet pressure tap on gas
valve. Start unit and allow 5 minutes for unit to
reach high fire steady state.
2 – While waiting for the unit to stabilize, notice the
flame. Flame should be stable and should not lift
from burner. Natural gas should burn blue. L.P. gas
should burn mostly blue with some orange
streaks.
3 – After allowing unit to stabilize for 5 minutes, re-
cord manifold pressure and compare to values
given in table 5.
NOTE– Disconnect heating demand as soon as an
accurate reading has been obtained.
F – Proper Gas Flow
To check for proper gas flow to combustion chamber,
determine Btuh input from unit rating plate or table or
the specifications tables on pages 1 and 2. Divide input
rating by Btuh per cubic foot of available gas. Result is
the number of cubic feet per hour required. Determine
flow of gas through gas meter for two minutes . Multi-
ply by 30 to get hourly flow of gas to burner.
NOTE– To obtain accurate reading, shut off all other
gas appliances connected to meter.
G – High Altitude Derate
C.G.A. certified units used in high altitude applications
are factory equipped with modifications that eliminate
the need for manifold pressure adjustment to obtain
proper heat input. Check the unit rating plate to make
sure unit is a high altitude unit.
A.G.A. certified units must be derated when installed at
an elevation of 2,000 ft. (610 m) or more above sea lev-
el. Tables 6 and 7 show the derated manifold pressure
for high altitude operation with both natural and LP/
Propane gas. Operating this appliance at the manifold
pressure specified on the tables will ensure proper unit
heat input at high altitude. Consult your gas utility for
the local natural gas heating value.
NOTE–This is the only permissible field derate for
this appliance.
2.25” wc
Altitude
*Heating Value (Btu/Ft
#
)
(Ft.)
900
950
1000
1050
1100
0
1000
2000
3000
4000
5000
6000
4.32” wc
4.32” wc
3.65” wc
3.35” wc
3.05” wc
2.77” wc
2.50” wc
3.88” wc
3.88” wc
3.30” wc
3.00” wc
2.75” wc
2.48” wc
3.50” wc
3.50” wc
2.95” wc
2.70” wc
2.45” wc
2.25” wc
3.17” wc
3.17” wc
2.70” wc
2.45” wc
2.25” wc
2.89” wc
2.89” wc
2.45” wc
2.25” wc
HIGH ALTITUDE MANIFOLD PRESSURE
DERATE FOR NATURAL GAS UNITS
*Heating value based on atmospheric pressure of 30” mercury
and temperature of 60
°
F (16
°
C).
TABLE 6
_ _
_ _
_ _
_ _
_ _
_ _
ALTITUDE
(Ft.)
MANIFOLD
PRESSURE
HIGH ALTITUDE MANIFOLD PRESSURE
DERATE FOR LP/PROPANE GAS UNITS
0
1000
2000
3000
4000
5000
6000
9.5”
w.c.
8.0”
w.c.
7.2”
w.c.
6.5”
w.c.
5.9”
w.c.
5.3”
w.c.
TABLE 7
9.5”
w.c.
IMPORTANT
For safety, shut unit off and remove manometer as
soon as an accurate reading has been obtained.
Take care to replace pressure tap plug.
H – Flame Signal
Flame signal or microamp is an electrical current which
passes from the ignition control through the sensor
electrode during unit operation. Current passes from
the sensor through the flame to ground to complete a
safety circuit. A 50 microamp DC meter is needed to
check flame signal on the primary ignition control.