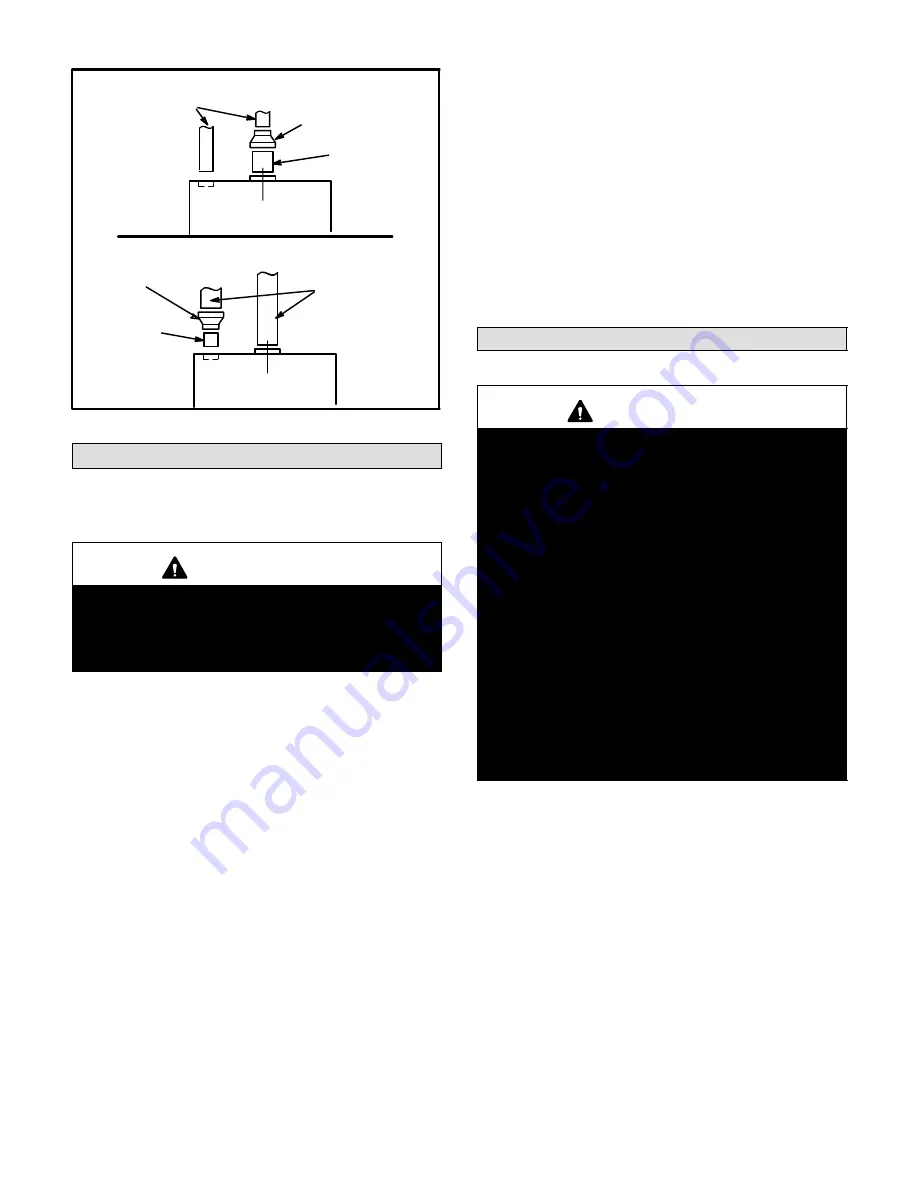
Page 9
FIGURE 7
G32V-100 OR -125 WITH 2 IN. VENTING
G32V-100 OR -125 WITH 3 IN. VENTING
3 IN.
IN
2 IN.
OUT
3 IN. FIELD
PROVIDED
NIPPLE
3 IN. X 2 IN.
REDUCER
2 IN. VENT PIPE
3 IN.
IN
2 IN.
OUT
3 IN. VENT PIPE
3 IN. X 2 IN. REDUCER
2 IN. FIELD
PROVIDED
NIPPLE
Joint Cementing Procedure
All cementing of joints should be done according to the
specifications outlined in ASTM D 2855.
WARNING
DANGER OF EXPLOSION! Fumes from PVC glue
may ignite during system check. Disconnect wire
from pressure switch terminal before 115 volt powĆ
er is applied to unit. Reconnect wire after two minĆ
utes of combustion air blower operation.
1 - Measure and cut vent pipe to desired length.
2 - Debur and chamfer end of pipe, removing any ridges
or rough edges. If end is not chamfered, edge of pipe
may remove cement from fitting socket and result in
a leaking joint.
3 - Clean and dry surfaces to be joined.
4 - Test fit joint and mark depth of fitting on outside of
pipe.
5 - Uniformly apply liberal coat of PVC primer for PVC or
ABS cleaner for ABS to inside socket surface of fitĆ
ting and male end of pipe to depth of fitting socket.
6 - Promptly apply solvent cement to end of pipe and inĆ
side socket surface of fitting. Cement should be apĆ
plied lightly but uniformly to inside of socket. Take
care to keep excess cement out of socket. Apply
second coat to end of pipe.
NOTE - Time is critical at this stage. Do not allow
primer to dry before applying cement.
7 - Immediately after applying last coat of cement to
pipe, and while both inside socket surface and end of
pipe are wet with cement, forcefully insert end of pipe
into socket until it bottoms out. Turn pipe 1/4 turn durĆ
ing assembly (but not after pipe is fully inserted) to
distribute cement evenly.
NOTE - Assembly should be completed within 20 seĆ
conds after last application of cement. Hammer
blows should not be used when inserting pipe.
8 - After assembly, wipe excess cement from pipe at
end of fitting socket. A properly made joint will show a
bead around its entire perimeter. Any gaps may indiĆ
cate a defective assembly due to insufficient sol-
vent.
9 - Handle joints carefully until completely set.
Venting Practices
WARNING
Insufficient combustion air can cause headaches,
nausea, dizziness or asphyxiation. It will also
cause excess water in the heat exchanger resulting
in rusting and premature heat exchanger failure.
Excessive exposure to contaminated combustion
air will result in safety and performance related
problems. Avoid exposure to the following subĆ
stances in the combustion air supply:
Permanent wave solutions
Chlorinated waxes and cleaners
Chlorine base swimming pool chemicals
Water softening chemicals
De-icing salts or chemicals
Carbon tetrachloride
Halogen type refrigerants
Cleaning solvents (such as perchloroethylene)
Printing inks, paint removers, varnishes, etc.
Hydrochloric acid
Cements and glues
Antistatic fabric softeners for clothes dryers
Masonry acid washing materials
The thickness of construction through which vent/air inĆ
take pipes may be installed is a minimum of 3 inches (76
mm) and a maximum of 24 inches (610 mm). If a G32V
furnace replaces a furnace which was commonly vented
with another gas appliance, the size of the existing vent
pipe for that gas appliance must be checked. Without the
heat of the original furnace flue products, the existing vent
pipe is probably oversized for the single water heater or
other appliance. The vent should be checked for proper
draw with the remaining appliance.
Intake Piping
1 - Cement intake piping in slip connector located at top
of unit.
2 - Route piping to outside of structure. Continue with
installation following instructions given in exhaust
and intake piping termination section.