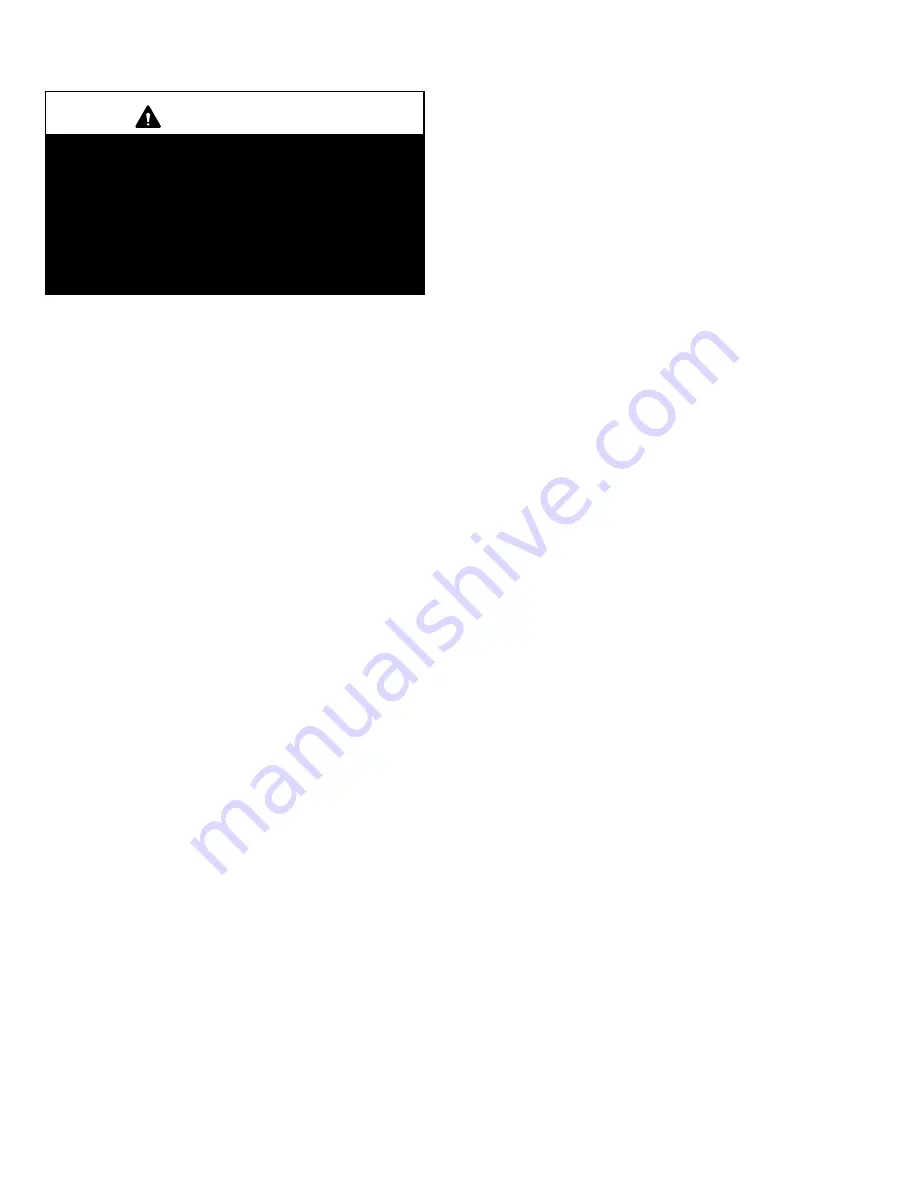
Page 18
Testing for Proper Venting and Sufficient Combustion Air
WARNING
CARBON MONOXIDE POISONING HAZARD!
Failure to follow the steps outlined below for each
appliance connected to the venting system being
placed into operation could result in carbon monox
ide poisoning or death.
The following steps shall be followed for each ap
pliance connected to the venting system being
placed into operation, while all other appliances con
nected to the venting system are not in operation.
After the G41UF vent system has been completed, the fol
lowing test should be conducted to ensure proper venting
and sufficient combustion air has been provided to the
G41UF, as well as to other gasfired appliances which are
separately vented. The test should be conducted while all
appliances (both in operation and those not in operation)
are connected to the venting system being tested. If the
venting system has been installed improperly, or if provi
sions have not been made for sufficient amounts of com
bustion air, corrections must be made as outlined in the
previous section.
1 − Seal any unused openings in the venting system.
2 − Visually inspect the venting system for proper size and
horizontal pitch. Determine there is no blockage or re
striction, leakage, corrosion, or other deficiencies
which could cause an unsafe condition.
3 − To the extent that it is practical, close all building doors
and windows and all doors between the space in which
the appliances connected to the venting system are lo
cated and other spaces of the building.
4 − Close fireplace dampers.
5 − Turn on clothes dryers and any appliances not con
nected to the venting system. Turn on any exhaust
fans, such as range hoods and bathroom exhausts, so
they will operate at maximum speed. Do not operate a
summer exhaust fan.
6 − Follow the lighting instruction to place the G41UF or
other appliance being inspected into operation. Adjust
thermostat so appliance will operate continuously.
7 − Test for spillage of flue gases at the draft hood relief
opening after 5 minutes of main burner operation. Use
the flame of match or candle, or smoke from a ciga
rette, cigar.
8 − If improper venting is observed during any of the
above tests, the venting system must be corrected or
sufficient combustion/makeup air must be provided.
The venting system should be resized to approach
the minimum size as determined by using the ap
propriate tables in appendix G in the current standards
of the National Fuel Gas Code ANSI−Z223.1/NPFA 54
in the U.S.A., and the appropriate Natural Gas and
Propane appliances venting sizing tables in the cur
rent standard of the CSA−B149.1 Natural Gas and
Propane Installation Code in Canada.
9 − After determining that each appliance remaining
connected to the common venting system properly
vents when tested as indicated in step 3, return
doors, windows, exhaust fans, fireplace dampers
and any other gasburning appliance to their previous
condition of use.
General Guidelines for Vent Terminations for NonDirect
Vent Installations.
In NonDirect Vent installations combustion air is taken
from indoors and the flue gases are discharged to the out
doors. The G41UF is then classified as a nondirect vent,
Category IV gas furnace. In NonDirect Vent installations
the vent termination is limited by local building codes. In
the absence of local codes, refer to the current National
Fuel Gas Code ANSI Z223−1/NFPA 54 in U.S.A., and cur
rent standards CSA−B149.1 of the Natural Gas and Pro
pane Installation Codes in Canada for details.
Position termination ends according to locations given in
figure 19. In addition, position termination ends so they are
free from any obstructions and above the level of snow ac
cumulation (where applicable). The termination should be
at least 12 inches (305mm) from any opening through
which flue products could enter the building.
At vent termination, care must be taken to maintain
protective coatings over building materials (prolonged
exposure to exhaust condensate can destroy protective
coatings). It is recommended that the exhaust outlet not be
located within 6 feet (1.8m) of a condensing unit because
the condensate can damage the painted coating.
NOTE − If winter design temperature is below 32°F (0°C),
exhaust piping should be insulated with 1/2" (13mm), Ar
maflex or equivalent when run through unheated space.
Do not leave any surface area of exhaust pipe open to out
side air; exterior exhaust pipe should be insulated with 1/2"
(13mm) Armaflex or equivalent. In extreme cold climate
areas, 3/4" (19mm) Armaflex or equivalent may be neces
sary. Insulation on outside runs of exhaust pipe must be
painted or wrapped to protect insulation from deterioration.
Exhaust pipe insulation may not be necessary in some
specific applications.
NOTE − During extremely cold temperatures, below
approximately 20°F (6.7°C), units with long runs of vent
pipe through unconditioned space, even when insulated,
may form ice in the exhaust termination that prevents the
unit from operating properly. Longer run times of at least 5
minutes will alleviate most icing problems. Also, a heating
cable may be installed on exhaust piping and termination to
prevent freeze−ups. Heating cable installation kit is avail
able from Lennox. See Condensate Piping section for part
numbers.