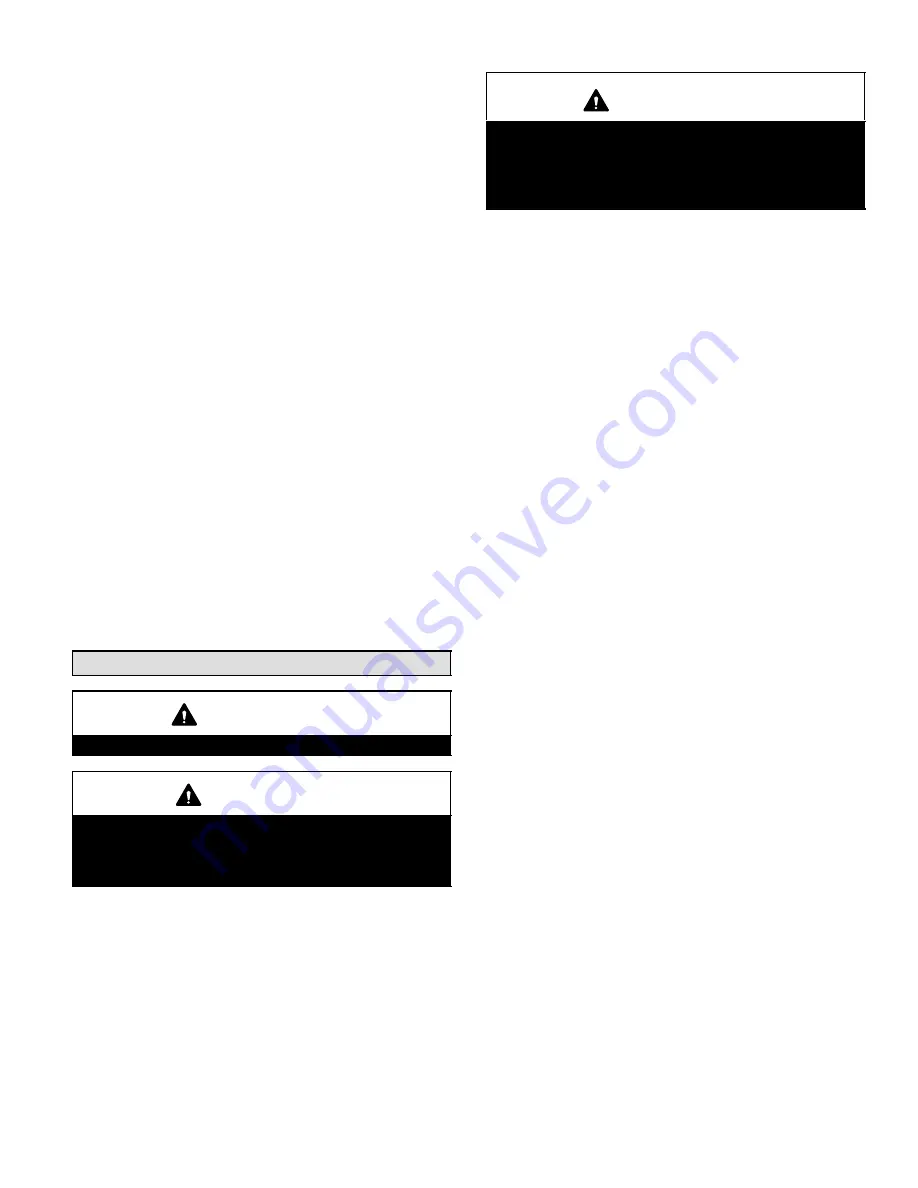
Page 29
Electronic Ignition
The SureLight
®
integrated control has an added feature of
an internal Watchguard control. The feature serves as an
automatic reset device for ignition control lockout caused
by ignition failure. After one hour of continuous thermostat
demand for heat, the Watchguard will break and remake
thermostat demand to the furnace and automatically reset
the control to begin the ignition sequence.
Flue And Chimney
1 − Check flue pipe, chimney and all connections for tight-
ness and to make sure there is no blockage.
2 − Check unit for proper draft.
3 − Is pressure switch closed? Obstructed flue will cause
unit to shut off at pressure switch. Check flue and outlet
for blockages.
4 − Reset manual flame rollout switches on burner box
cover.
Failure To Operate
If the unit fails to operate, check the following:
1 − Is the thermostat calling for heat?
2 − Are access panels securely in place?
3 − Is the main disconnect switch closed?
4 − Is there a blown fuse?
5 − Is the filter dirty or plugged? Dirty or plugged filters will
cause the limit control to shut the unit off.
6 − Is gas turned on at the meter?
7 − Is the manual main shut-off valve open?
8 − Is the internal manual shut-off valve open?
9 − Is the unit ignition system in lock out? If the unit locks out
again, inspect the unit for blockages.
Service
WARNING
Disconnect power before servicing unit.
CAUTION
Label all wires prior to disconnection when servicing
controls. Wiring errors can cause improper and dan-
gerous operation. Verify proper operation after ser-
vicing.
At the beginning of each heating season, a qualified techni-
cian should check the system as follows:
Blower
Check the blower wheel for debris and clean if necessary.
The blower motors are prelubricated for extended bearing
life. No further lubrication is needed.
WARNING
The blower access panel must be securely in place
when the blower and burners are operating. Gas
fumes, which could contain carbon monoxide, can
be drawn into living space resulting in personal inju-
ry or death.
Filters
All G50DF(X) filters are installed external to the unit. Filters
should be inspected monthly. Clean or replace the filters
when necessary to ensure that the furnace operates prop-
erly. Replacement filters must be rated for high velocity air-
flow. Table 3 lists recommended filter sizes.
Flue And Chimney
Check the flue pipe, chimney and all connections for tight-
ness and to make sure there is no blockage.
Electrical
1 − Check all wiring for loose connections.
2 − Check for the correct voltage at the furnace (furnace
operating).
3 − Check amp−draw on the blower motor.
Motor Nameplate__________Actual__________
Cleaning the Heat Exchanger and Burners
NOTE − Use papers or protective covering in front of the fur-
nace during cleaning.
Cleaning the heat exchanger requires a steel spring
snake," a reversible drill and a vacuum cleaner. The steel
spring snake may be constructed using a 4 ft. long by 1/4
inch diameter steel wire cable and a 1/4 inch diameter wire
brush. These items are available at a hardware store. In-
sert wire end of brush into the open end of the spring cable.
Crimp the cable around the brush so that the brush is se-
cured and will not come off during cleaning. Attach the oth-
er end of the cable to the reversible drill to complete the tool
for cleaning the heat exchanger.
1 − Turn off both electrical and gas supplies to the furnace.
Remove the furnace access panels.
2 − Remove the three screws that secure the vent pipe to
the flue collar. See figure 10.
3 − Remove the screw that secures the internal flue pipe to
the combustion air inducer. See figure 25.
4 − Scrape away the silicone sealant that is between the
internal flue pipe and the combustion air inducer.
5 − Pull the internal flue pipe into the chase.
6 − Label and disconnect the pressure switch wires.
7 − Remove the four screws that secure the combustion
air inducer. Carefully remove the combustion air induc-
er to avoid damaging the blower gasket. If the gasket is
damaged, it must be replaced to prevent leakage. See
figure 26.