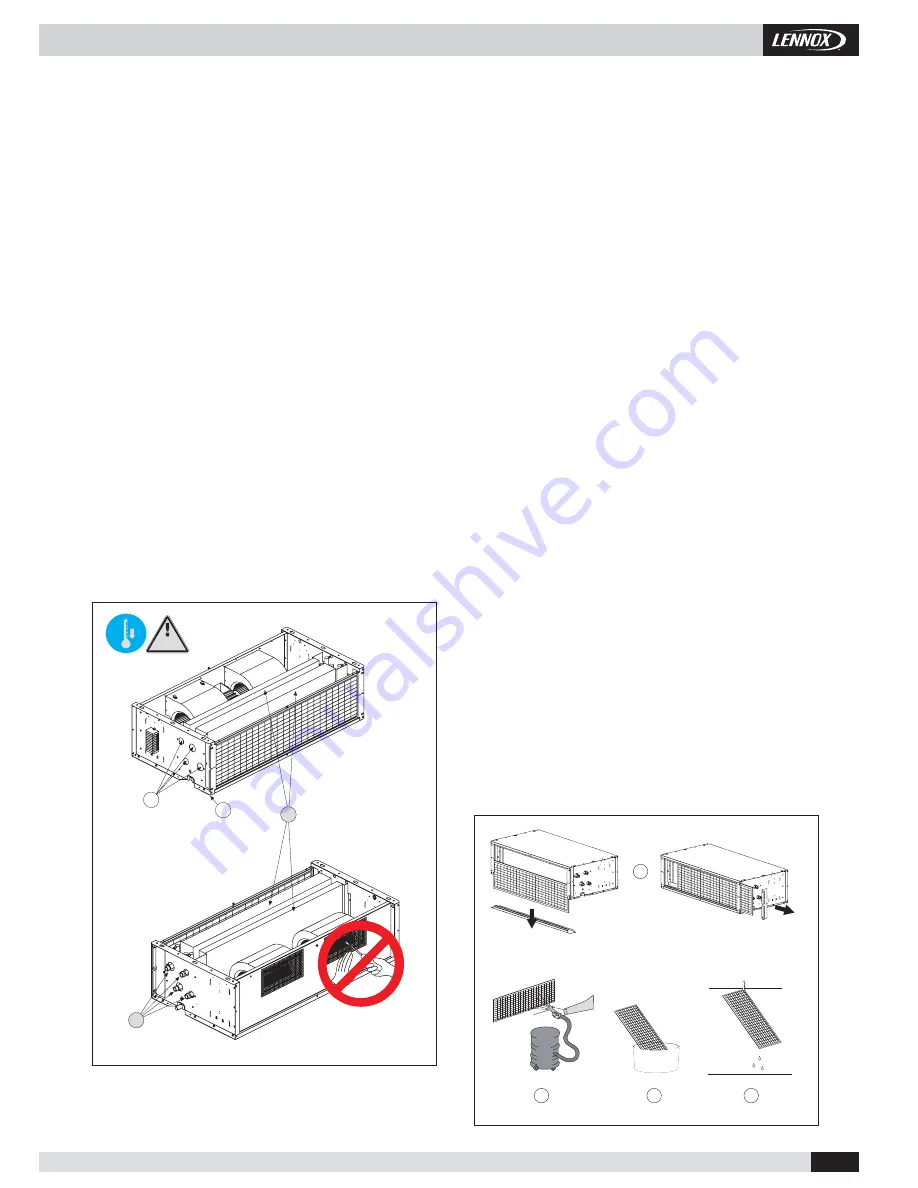
• 29 •
1
2
3
4
P=8
bar max
0
°
6
0
°
1
4
3
2
Installation, operation and maintenance /
INALTO-IOM-1809-E
TURNING THE COIL
CAUTION
The fan wheels may reach the speed of 1,000 rpm. Do not insert objects
into the electric fan and certainly not hands. The motor becomes hot during
operation; wait for it to cool before touching it. During the heating mode of
operation the exchanger and the connecting pipes may become very hot
(80°C). Wait for the exchanger to cool before touching it or protect hands
with suitable gloves. The heat exchange water coils are suitable for work-
ing up to a maximum pressure of 8 bar.
To turn the coil, proceed as follows:
1. Disconnect the terminal board (6) from the side of the unit.
2. Remove the condensate collecting tray (2).
3. Remove the coil
fi
xing screws (5).
4. Take out the coil (3), being careful not to be cut by the
fi
ns and not to
damage them.
5. Remove the knockouts (1) on the opposite side of the unit (using a
screwdriver) to allow the coil connections to pass through.
6. Position the coil, turning it without tipping it upside down, so that the
fi
ttings are in line with the holes left by the knockouts.
7. Fix the coil using the previously removed screws (5).
8. Shift the terminal board (
fi
xing it to the side opposite the water
fi
t-
tings) and the motor cables,
fi
xing them with their clamps. Ensure
that the cables pass through the hole in the side of the unit, protecting
them with the relative grommet. If it proves easier to carry out this
operation by separating the wires from the terminal board, mark the
positions of the wires to avoid making mistakes when reconnecting.
9. Reconnect the wires to the relative terminal board (6), taking care
that they are correctly positioned.
10. Replace the condensate collecting tray (2).
Pic. 41
CLEANING AND MAINTENANCE
CAUTION
Before carrying out any cleaning or maintenance work, disconnect
the unit from the mains electricity supply!
ROUTINE MAINTENANCE
The user is duty bound to have all maintenance operations carried out by
trained and quali
fi
ed personnel only. If the unit has to be dismantled, pro-
tect hands with work gloves.
Monthly checks:
- Ensure that the fan impellers are clean. If they are dirty, clean them by
suction so as not to damage them.
- Check the whole of the electrical part and in particular that the electrical
connections are tight.
Yearly checks:
- Check the whole of the electrical part and in particular that the electrical
connections are tight.
- Check the tightness of all the bolts, nuts and whatever else may be
loosened by the constant vibrations of the unit.
- Check the motor for dust, dirt or other impurities. Periodically check that
the motor works without unusual vibrations or noise and that the fan
inlet is not obstructed, which could otherwise leading to overheating of
the windings.
- Check the fans for dirt or any foreign matter.
CLEANING THE AIR FILTER
The unit is
fi
tted with an air
fi
lter on the fan inlet. During normal operation
the
fi
lter holds back impurities in the air.
The
fi
lter should be cleaned periodically to keep its
fi
ltering properties and
the air
fl
ow to the fan unchanged.
It is advisable to clean the
fi
lter at least once a month, proceeding as fol-
lows.
1. Take out the
fi
lter.
2. Place the
fi
lter on a
fl
at, dry surface and remove the accumulated dust
with a vacuum cleaner.
3. Wash the
fi
lter with water and detergent (no solvents).
4. Leave the
fi
lter to dry in a ventilated place in the sun.
5. Replace the
fi
lter when it is perfectly dry.
Please clean the air fi lter every working season of the unit or more
frequently considering the unit activity.
NOTE: the fi lter may also be taken out from the side or from the top.
Pic. 42