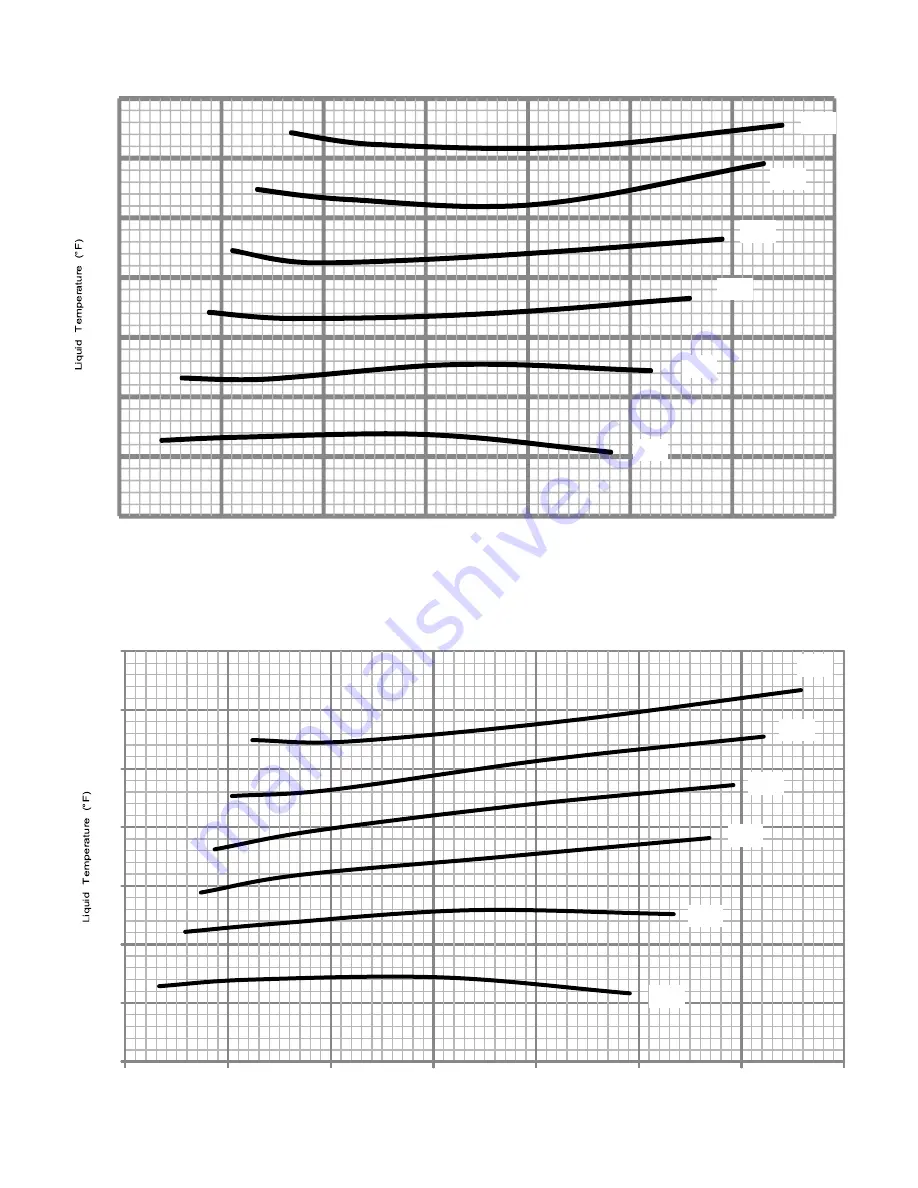
Page 33
LGH/LCH036, 048, 060, 072
LGH/LCH060S CHARGING CURVE - ALL-ALUMINUM COIL
60
70
80
90
100
110
120
130
110
120
130
140
150
160
Outdoor Temperature (°F)
170
180
Suction Pressure (psig)
105°
95°
115°
85°
75°
65°
60
70
80
90
100
110
120
130
110
120
130
140
150
160
Outdoor Temperature (°F)
170
180
Suction Pressure (psig)
105°
95°
115°
85°
75°
65°
LGH/LCH060H CHARGING CURVE - ALL-ALUMINUM COIL