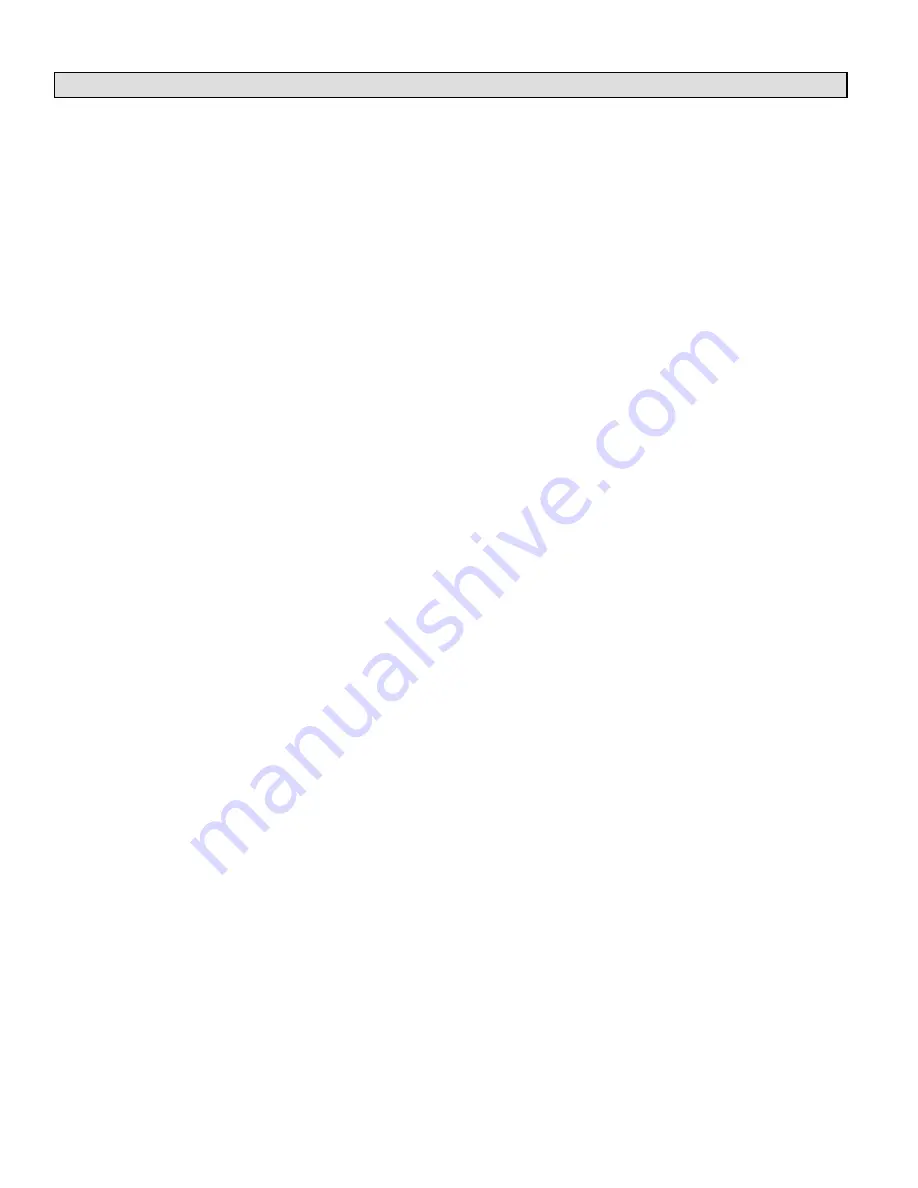
Page 56
Requirements for Commonwealth of Massachusetts
Modifications to NFPA−54, Chapter 10
Revise NFPA−54 section 10.8.3 to add the following re-
quirements:
For all side wall, horizontally vented, gas−fueled equipment
installed in every dwelling, building or structure used in
whole or in part for residential purposes, including those
owned or operated by the Commonwealth and where the
side wall exhaust vent termination is less than seven (7)
feet above the finished grade in the area of the venting, in-
cluding but not limited to decks and porches, the following
requirements shall be satisfied:
1 − INSTALLATION OF CARBON MONOXIDE DETEC-
TORS. At the time of installation of the side wall, hori-
zontally vented, gas−fueled equipment, the installing
plumber or gasfitter shall observe that a hard−wired
carbon monoxide detector with an alarm and battery
backup is installed on the floor level where the gas
equipment is to be installed. In addition, the installing
plumber or gasfitter shall observe that a battery−oper-
ated or hard−wired carbon monoxide detector with an
alarm is installed on each additional level of the dwell-
ing, building or structure served by the side wall, hori-
zontally vented, gas−fueled equipment. It shall be the
responsibility of the property owner to secure the ser-
vices of qualified licensed professionals for the instal-
lation of hard−wired carbon monoxide detectors.
a − In the event that the side wall, horizontally vented,
gas−fueled equipment is installed in a crawl space
or an attic, the hard−wired carbon monoxide detec-
tor with alarm and battery back−up may be installed
on the next adjacent floor level.
b − In the event that the requirements of this subdivi-
sion cannot be met at the time of completion of
installation, the owner shall have a period of thirty
(30) days to comply with the above requirements;
provided, however, that during said thirty (30) day
period, a battery−operated carbon monoxide detec-
tor with an alarm shall be installed.
2 − APPROVED CARBON MONOXIDE DETECTORS.
Each carbon monoxide detector as required in accor-
dance with the above provisions shall comply with
NFPA 720 and be ANSI/UL 2034 listed and IAS certi-
fied.
3 − SIGNAGE. A metal or plastic identification plate shall
be permanently mounted to the exterior of the building
at a minimum height of eight (8) feet above grade di-
rectly in line with the exhaust vent terminal for the hori-
zontally vented, gas−fueled heating appliance or
equipment. The sign shall read, in print size no less
than one−half (1/2) inch in size, GAS VENT DIRECT-
LY BELOW. KEEP CLEAR OF ALL OBSTRUC-
TIONS."
4 − INSPECTION. The state or local gas inspector of the
side wall, horizontally vented, gas−fueled equipment
shall not approve the installation unless, upon inspec-
tion, the inspector observes carbon monoxide detec-
tors and signage installed in accordance with the pro-
visions of 248 CMR 5.08(2)(a) 1 through 4.
EXEMPTIONS: The following equipment is exempt
from 24 CMR 5.08(2)(a) 1 through 4:
1 − The equipment listed in Chapter 10 entitled Equip-
ment Not Required to Be Vented" in the most current
edition of NFPA 54 as adopted by the Board; and
2 − Product Approved side wall, horizontally vented, gas−
fueled equipment installed in a room or structure sepa-
rate from the dwelling, building or structure used in
whole or in part for residential purposes.
MANUFACTURER REQUIREMENTS −
GAS EQUIPMENT VENTING SYSTEM PROVIDED.
When the manufacturer of Product Approved side wall,
horizontally vented, gas−fueled equipment provides a vent-
ing system design or venting system components with the
equipment, the instructions provided by the manufacturer
for installation of the equipment and the venting system
shall include:
1 − Detailed instructions for the installation of the venting
system design or the venting system components:
and
2 − A complete parts list for the venting system design or
venting system.
MANUFACTURER REQUIREMENTS −
GAS EQUIPMENT VENTING SYSTEM NOT PROVIDED.
When the manufacturer of Product Approved side wall,
horizontally vented, gas−fueled equipment does not pro-
vide the parts for venting the flue gases, but identifies spe-
cial venting systems," the following requirements shall be
satisfied by the manufacturer:
1 − The referenced special venting system" instructions
shall be included with the appliance or equipment
installation instructions; and
2 The special venting systems" shall be Product Ap-
proved by the Board, and the instructions for that sys-
tem shall include a parts list and detailed installation
instructions.
A copy of all installation instructions for all Product
Approved side wall, horizontally vented, gas−fueled
equipment, all venting instructions, all parts lists for
venting instructions, and/or all venting design instruc-
tions shall remain with the appliance or equipment at
the completion of the installation.