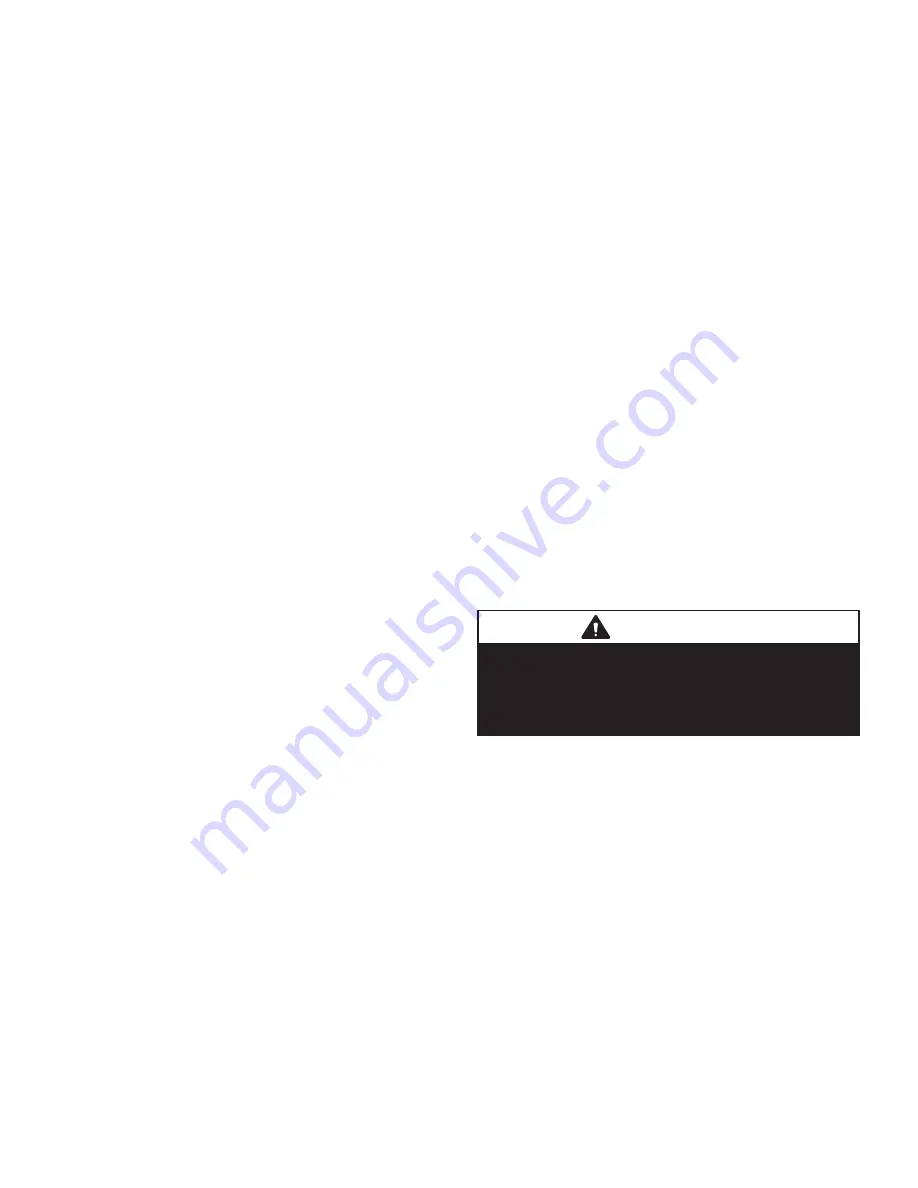
Page 27
9 -
Ensure sufficient combustion air is available to the
furnace. Fresh air grilles and louvers (on the unit
and in the room where the furnace is installed)
must be properly sized, open and unobstructed to
provide combustion air.
10 - Inspect the furnace venting system to make sure
it is in place, structurally sound, and without holes,
corrosion, or blockage. Vent system must be free
and clear of obstructions and must slope upward
away from the furnace . Vent system should be
installed per the National Fuel Gas Code
11 - Inspect the furnace return air duct connection to
ensure the duct is sealed to the furnace. Check for
air leaks on supply and return ducts and seal where
necessary.
12 - Check the condition of the furnace cabinet insulation
and repair if necessary.
13 - Perform a complete combustion analysis during the
furnace inspection to ensure proper combustion
and operation. Consult Service Literature for proper
combustion values.
14 -
Verify operation of CO detectors and replace
batteries as required.
Perform a general system test. Turn on the furnace to
check operating functions such as the start-up and shut-
off operation.
1 - Check the operation of the ignition system, inspect
and clean flame sensor. Check microamps before
and after. Check controls and safety devices (gas
valve, flame sensor, temperature limits). Consult
Service Manual for proper operating range. Thermal
Limits should be checked by restricting airflow and
not disconnecting the indoor blower. For additional
details, please see Service and Application Note
H049.
2 -
Verify that system total static pressure and airflow
settings are within specific operating parameters.
3 - Clock gas meter to ensure that the unit is operating
at the specified firing rate. Check the supply
pressure and the manifold pressure. On two-stage
gas furnaces check the manifold pressure on high
fire and low fire. If manifold pressure adjustment is
necessary, consult the Service Literature for unit
specific information on adjusting gas pressure.
Not all gas valves are adjustable. Verify correct
temperature rise.
Cleaning the Burners
NOTE -
Use papers or protective covering in front of the
furnace
during cleaning.
1 - Turn off both electrical and gas power supplies to
furnace.
2 - Label the wires from gas valve, rollout switches,
primary limit switch and make-up box then
disconnect them.
3 - Disconnect gas supply piping. Remove the four
screws securing the burner manifold assembly to
the vestibule panel and remove the assembly from
the unit.
4 - Remove 4 screws securing burner box and remove
burner box.
5 - To clean burners, run a vacuum cleaner with a soft
brush attachment over the face of burners. Visually
inspect inside the burners and crossovers for any
blockage caused by foreign matter. Remove any
blockage. Figure 25 shows burner detail.
6 - Reinstall burner box, manifold assembly and burner
box cover.
7 - Reconnect all wires.
8 - Reconnect gas supply piping.
9 - Turn on power and gas supply to unit.
10 - Set thermostat and check for proper operation.
11 -
Check all piping connections, factory and field, for
gas leaks. Use a leak detecting solution or other
preferred means.
CAUTION
Some soaps used for leak detection are corrosive to
certain metals. Carefully rinse piping thoroughly after
leak test has been completed. Do not use matches,
candles, flame or other sources of ignition to check for
gas leaks.
12 - If a leak is detected, shut gas and electricity off and
repair leak.
13 - Repeat steps 12 and 13 until no leaks are detected.
14 - Replace access panel.