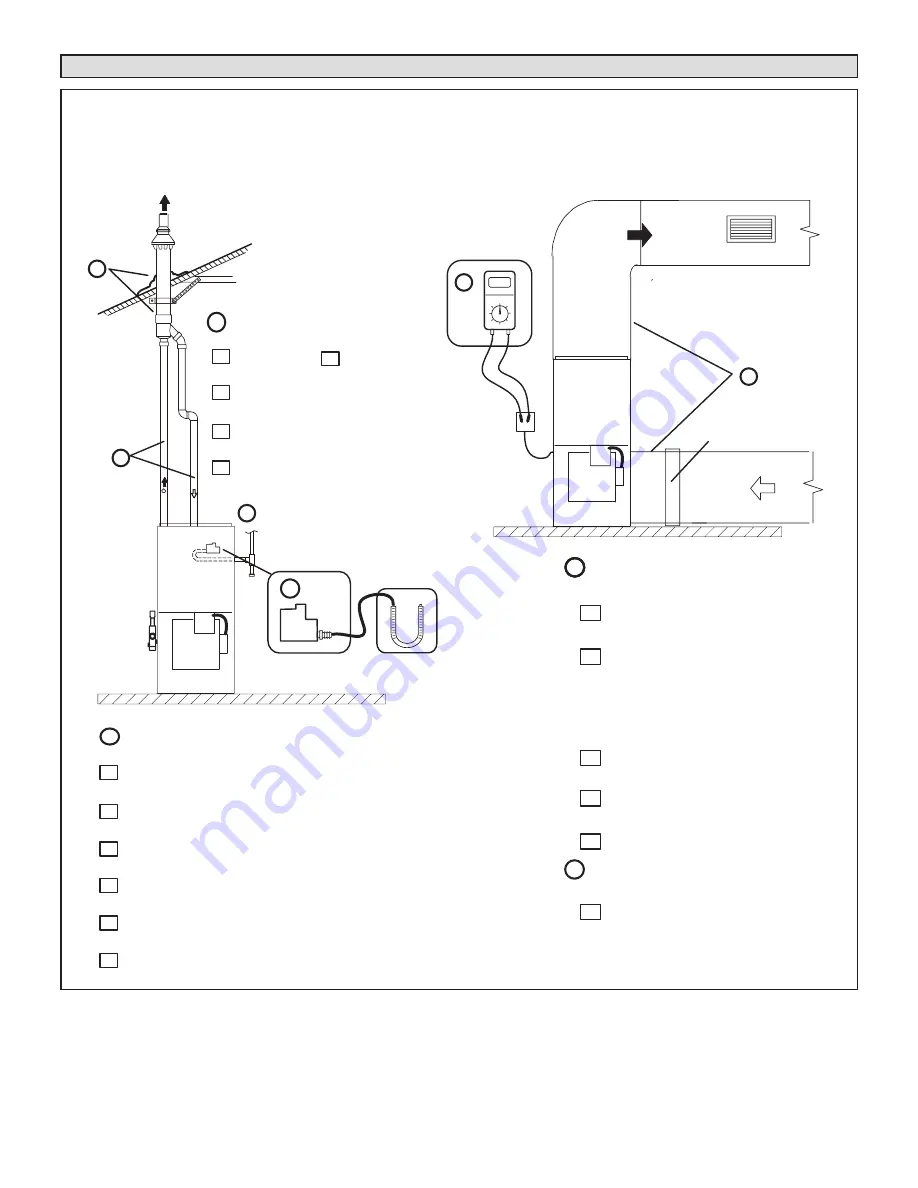
Page 48
Start-Up & Performance Check List
Gas Supply Pressure
SUPPLY
AIR
Line Voltage
GAS SUPPLY
Natural Gas
LP Propane Gas
Piping Connections Tight
Leak Tested
Supply Line Pressure “W.C.________
1
INTAKE / EXHAUST PIPE
All Joints Primed and Glued
Terminations Installed Properly
Pipes Supported
Condensate Trap Primed / Line Sloped
Heat Cable Installed and Operable (if applicable)
2
2
2
1
Horizontal Pipes Sloped (if applicable)
UNIT SET UP
3
4
Flter
RETURN AIR
Furnace:
Model Number_______________
Serial Number_________________
3
DUCT SYSTEM
SUPPLY AIR DUCT
Sealed
Insulated (if necessary)
RETURN DUCT
Sealed
Filter Installed and Clean
Grilles Unobstructed
4
VOLTAGE CHECK
Supply Voltage _____
Electrical Connections Tight
1