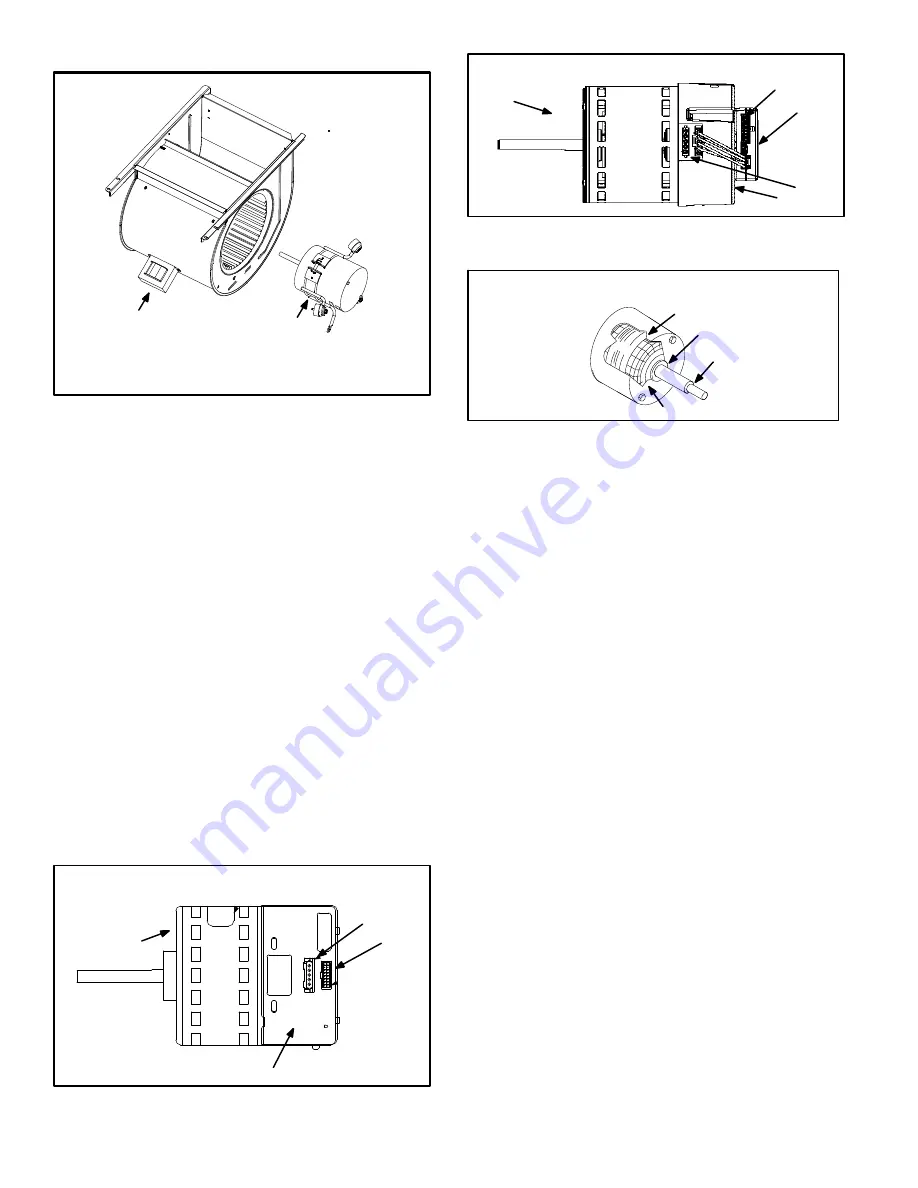
Page 12
B- Indoor Blower Motor
FIGURE 4
Power Choke
(5 Ton Only)
Blower Motor
(B3)
To Remove Blower From Unit: Remove Bolts and
Wiring Jackplugs. Then Slide Out Front of Unit.
Blower Motor (B3)
Blower motors are manufactured by GenTeq and Nidec. See
figures 5 and 6. Motors operate the same and are only differ
ent in physical appearance. They are both three‐phase, elec
tronically controlled DC brushless motors (controller converts
single-phase AC to three-phase DC), with a permanent mag
net type rotor (figure 5). Because these motors have a per
manent magnet rotor it does not need brushes like conven
tional DC motors.
Internal components for both manufactured motors are simi
lar and shown in figure 7. The stator windings are split into
three poles which are electrically connected to the controller.
This arrangement allows motor windings to turn on and off
in sequence by the controller.
A solid‐state controller is attached to the motor. The
controller is primarily an AC to DC converter. Converted
DC power is used to drive the motor. The controller con
tains a microprocessor which monitors varying condi
tions inside the motor (such as motor workload). The
controller on the Emerson motor includes the 16X4W
control with three LED's PW, RX and TX located on the
face for troubleshooting. Figure 6 shows the location of
the 16X4W and table 5 the LED codes.
FIGURE 5
GenTeq BLOWER MOTOR B3
MOTOR
CONTROLLER
J49
J48
NIDEC BLOWER MOTOR B3
FIGURE 6
MOTOR
CONTROLLER
16X4W
J48
J49
BLOWER MOTOR COMPONENTS
FIGURE 7
STATOR
(WINDINGS)
OUTPUT
SHAFT
BEARING
ROTOR
The controller uses sensing devices to sense what position
the rotor is in at any given time. By sensing the position of the
rotor and then switching the motor windings on and off in se
quence, the rotor shaft turns the blower.
All blower motors use single phase power. An external
run capacitor is not used. The motor uses permanently
lubricated ball‐type bearings.
Internal Operation
Each time the controller switches a stator winding (figure 7) on
and off, it is called a “pulse.” The length of time each pulse
stays on is called the “pulse width.” By varying the pulse width
(figure 10), the controller varies motor speed (called “pulse‐
width modulation”). This allows for precise control of motor
speed and allows the motor to compensate for varying load
conditions as sensed by the controller. In this case, the control
ler monitors the static workload on the motor and varies motor
rpm in order to maintain constant airflow (cfm).
The motor controller is driven by the Two-stage Variable
Speed Integrated control board. The board receives its
demand (PWM signal or fixed 24 VAC or VDC signal) from
optional controls such as the Harmony III
t
zoning system,
SignatureStat
t
, Efficiency Plus Humidity Control (CCB1) or a
conventional thermostat.