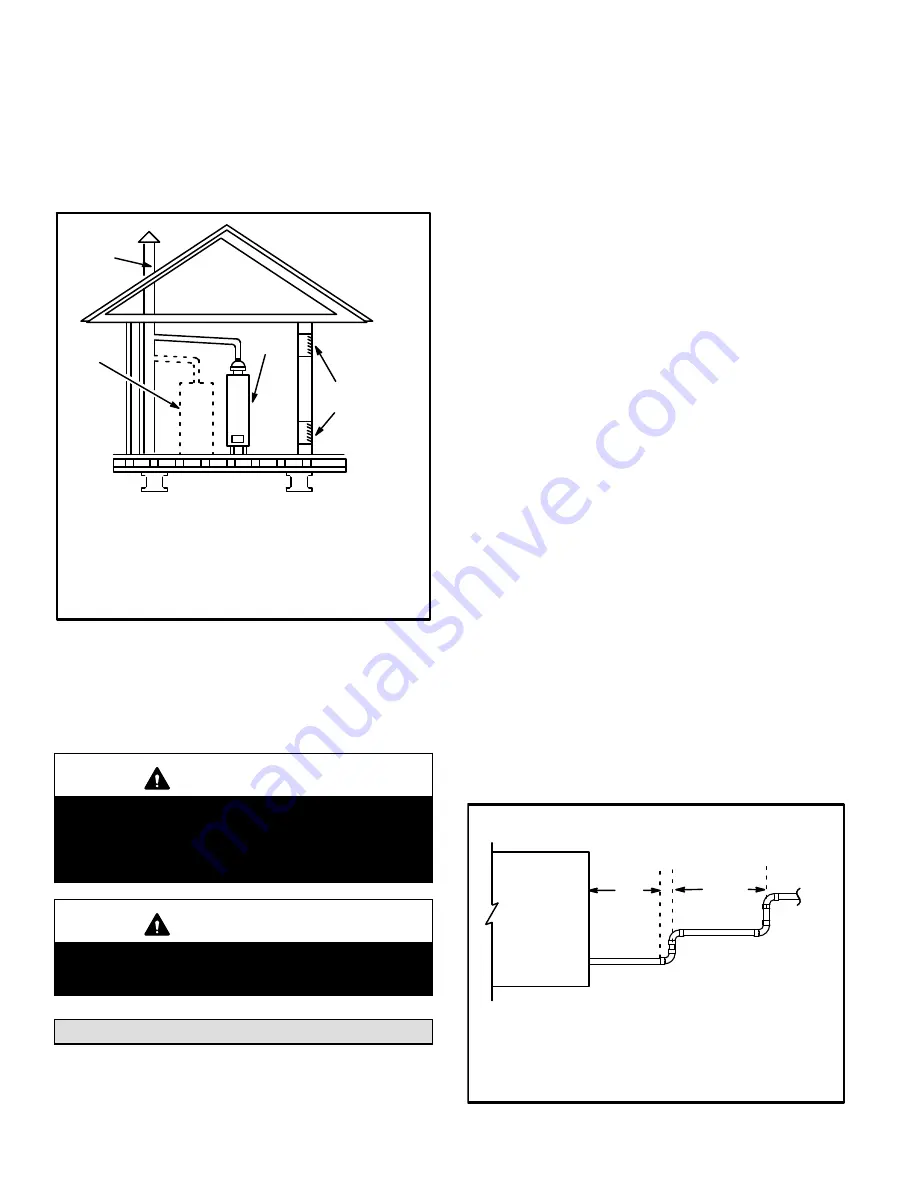
Page 24
7 - If a venting problem is found during any of the preced
ing tests, the common venting system must be modi
fied to correct the problem.
Resize the common venting system to the minimum
vent pipe size determined by using the appropriate
tables in Appendix G. (These are in the current stan
dards of the National Fuel Gas Code ANSI Z223.1.
CHIMNEY
OR GAS
VENT
(Check sizing
for water
heater only)
FURNACE
(Replaced
by EL296)
WATER
HEATER
OPENINGS
(To Adjacent
Room)
If an ML296UHV furnace replaces a furnace which was
commonly vented with another gas appliance, the size of
the existing vent pipe for that gas appliance must be
checked. Without the heat of the original furnace flue prod
ucts, the existing vent pipe is probably oversized for the
single water heater or other appliance. The vent should be
checked for proper draw with the remaining appliance.
FIGURE 16
REPLACING FURNACE THAT
WAS PART OF A COMMON
VENT SYSTEM
Exhaust Piping (Figures 17, 19 and 20)
Route piping to outside of structure. Continue with installa
tion following instructions given in piping termination sec
tion.
CAUTION
Do not discharge exhaust into an existing stack or
stack that also serves another gas appliance. If verti
cal discharge through an existing unused stack is re
quired, insert PVC pipe inside the stack until the end
is even with the top or outlet end of the metal stack.
CAUTION
The exhaust vent pipe operates under positive pres
sure and must be completely sealed to prevent leak
age of combustion products into the living space.
Vent Piping Guidelines
NOTE -
Lennox has approved the use of DuraVent
®
and
Centrotherm manufactured vent pipe and terminations as
an option to PVC. When using the PolyPro
®
by DuraVent or
InnoFlue
®
by Centrotherm venting system the vent pipe re
quirements stated in the unit installation instruction – min
imum & maximum vent lengths, termination clearances,
etc. – apply and must be followed. Follow the instructions
provided with
PoyPro by DuraVent and InnoFlue by Cen
trotherm venting system for assembly or if requirements
are more restrictive. The PolyPro by Duravent and In
noFlue by Centrotherm venting system must also follow
the uninsulated and unconditioned space criteria listed in
table 16.
The ML296UHV can be installed as either a Non-Direct
Vent or a Direct Vent gas central furnace.
NOTE
- In Non‐Direct Vent installations, combustion air is
taken from indoors or ventilated attic or crawlspace and flue
gases are discharged outdoors. In Direct Vent installations,
combustion air is taken from outdoors and flue gases are
discharged outdoors.
Intake and exhaust pipe sizing --
Size pipe according to
. Count all elbows inside and outside the
home. Table 13 lists the
minimum
vent pipe lengths per
mitted. Table
lists the
maximum
pipe lengths permitted.
Regardless of the diameter of pipe used, the standard roof
and wall terminations described in section
Exhaust Piping
Terminations
should be used. Exhaust vent termination
pipe is sized to optimize the velocity of the exhaust gas as
it exits the termination. Refer to table 17.
In some applications which permit the use of several differ
ent sizes of vent pipe, a combination vent pipe may be
used. Contact Lennox' Application Department for assis
tance in sizing vent pipe in these applications.
NOTE
- The exhaust collar on all models is sized to ac
commodate 2” Schedule 40 vent pipe. In horizontal ap
plications, any transition to exhaust pipe larger than 2”
must be made in vertical runs of the pipe. Therefore a 2”
elbow must be added before the pipe is transitioned to
any size larger than 2”. This elbow must be added to the
elbow count used to determine acceptable vent lengths.
Contact the Application Department for more information
concerning sizing of vent systems which include multiple
pipe sizes.
FIGURE 17
Horizontal Installation Offset Requirements
NOTE
- Exhaust pipe MUST be glued to furnace exhaust fittings.
NOTE -
All horizontal runs of exhaust pipe must slope back to
ward unit. A minimum of 1/4” (6mm) drop for each 12” (305mm)
of horizontal run is mandatory for drainage.
NOTE
- Exhaust piping should be checked carefully to make
sure there are no sags or low spots.
Exhaust Pipe
Horizontal
Gas Furnace
12” Min.
12” Max.