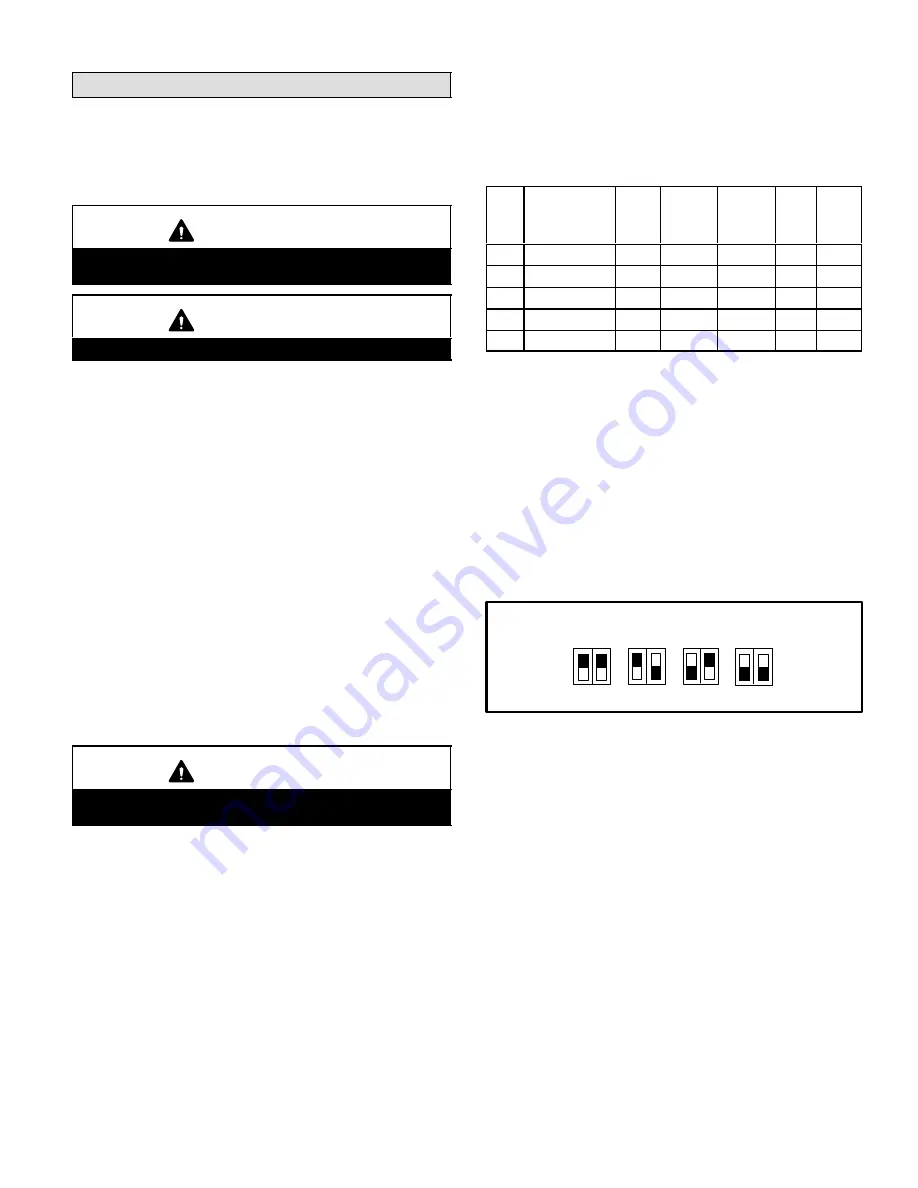
Page 16
Unit Start−Up & Adjustments
Before starting unit, make sure the oil tank is adequately
filled with clean No. 1 or No. 2 furnace oil.
NOTE − Water, rust or other contaminants in oil supply sys-
tem will cause malfunction and failure of the internal parts
of the fuel pump.
CAUTION
Never burn garbage or paper in the heating system.
Never leave papers near or around the unit.
CAUTION
Blower door must be in place before start−up.
1− Set thermostat for heating demand and turn on electri-
cal supply to unit.
2− Check initial air adjustment. All units are equipped with
an air adjustment dial on the right side of the burner.
See burner parts arrangement illustration.
3− Turn unit on. Place a can or container under the bleed
port located on the fuel pump. Loosen nut on bleed port
to release air and oil mixture from fuel line. Allow mix-
ture to escape until a steady stream of oil is emitted
from the port. Drain at least 1/2 pint of oil from the
pump. Retighten the nut on bleed port. If lockout oc-
curs, press reset button and continue with bleed proce-
dure.
NOTE − A two−pipe fuel system will normally bleed itself
by forcing air back to the tank through the return line.
This type of bleeding procedure is not necessary.
4− If burner fails to start, push reset button on primary
safety control and the burner motor reset button. See
part arrangement illustration.
CAUTION
Do not push the reset button on the primary control
more than one time.
5− If the burner fails to light again, refer to the trouble-
shooting section in this manual.
A − Fuel Pump Pressure
Measure fuel pump pressure with unit off. Attach pressure
gauge to pump outlet. Turn unit on and check pressure and
compare to table 6. Adjust if necessary.
B − Temperature Rise
To measure temperature rise, place plenum thermometers
in warm air and return air plenums. Locate thermometer in
warm air plenum where thermometer will not see" the heat
exchanger to prevent it from picking up radiant heat. Set
thermostat to its highest setting to start unit. After plenum
thermometers have reached their highest and steadiest
readings, subtract the readings. The difference in tempera-
tures in the supply and return air plenums should approxi-
mate the temperature rise range listed in table 6 and the ap-
pliance rating plate. If not, adjust the blower motor pulley to
adjust the blower speed.
Table 6
O23
Unit
nozzle size,
spray
angle,
& pattern
pump
PSIG
input
rating
BTU/HR
output
rating
BTU/HR
head
temp
rise
F°
−70
.50GPH−80° A
100
70,000
57,000
FB0
60−70
−105
.65GPH−80° B
140
105,000
84,000
FB3
65−75
−120
.75GPH−80° B
140
119,000
105,000
FB3
70−80
−140
.85GPH−80° B
140
140,000
112,000
FB6
65−75
−154
1.0GPH−80° B
140
154,000
125,000
FB6
70−80
C − Limit Control
Limit Control − Do not adjust it from factory setting.
D − Fan Control
The fan on time of 30 seconds is not adjustable. Fan off
time (time that the blower operates after the heat demand
has been satisfied) can be adjusted by moving the delay
switches on the fan control board. Fan off time will affect
comfort and is adjustable to satisfy individual applications.
See figure 19. Set the heat fan off delay switches to either
60, 90, 120, or 150 seconds. The factory setting is 90 sec-
onds.
150 sec
Figure 19
Fan Off Delay Switch Settings
120 sec
90 sec
60 sec
E − Burner Adjustment
The following instructions are essential to the proper op-
eration of O23 series oil furnaces. To prevent sooting,
these instructions must be followed in sequence:
1 − Draft
This test should be taken at the breach between the outlet
of the vent connector and the barometric draft control. Gen-
erally a 1/4" hole will need to be drilled for the draft gauge to
be inserted into the vent connector.
A minimum of 0.03 draft must be established without the
burner in operation. With the burner in operation, the draft
should be 0.04 to 0.05. This is VERY critical to the flame
retention head burners.
Oil furnace installations also require careful inspection to
make sure the chimney is in good shape and can accom-
modate the products of combustion. The temperature in
the unconditioned space will also affect the draft if long vent
connectors are allowed to get too cold.