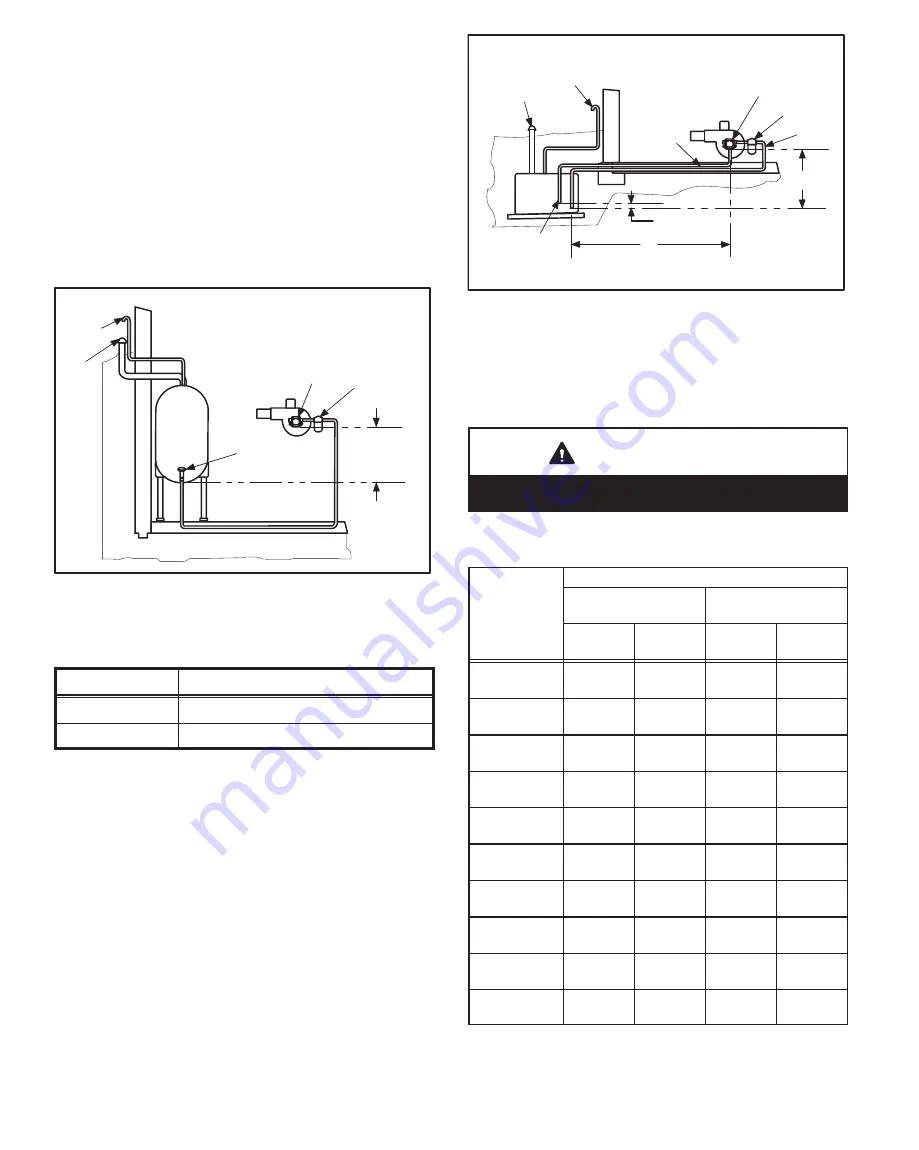
Page 14
One−Pipe System
When using a one−pipe system with the oil tank even above
the burner and a vacuum of 6" (152 mm) Hg or less, a single−
stage fuel pump with a supply line and no return line should be
adequate. See figure 16. Manual bleeding of the fuel pump is
required on initial start up. Failure to bleed air from the oil pump
could result in an air lock/oil starvation condition.
NOTE − As an extra precaution, cycle heating on and off
ten times after bleeding air from the oil pump. This will
eliminate air in the gun assembly.
Figure 16
Oil Piping
ÎÎ
ÎÎ
ÎÎ
ÎÎ
ÎÎ
ÎÎ
ÎÎ
ÎÎÎÎÎÎÎÎÎÎÎ
ÎÎÎÎÎÎÎÎÎÎÎÎ
Î
Î
air vent
fill
pipe
Oil
Tank
fuel
pump
Aux
Filter
Shut off
Valve
8 ft (2.4 m)
Maximum
One Pipe Lift
One-Pipe System
Table 4
One−pipe Oil Sizing
Line Length
Pipe Diameter (OD Tubing)
0−50’ (15 m)
3/8" (10 mm)
51−100’ (15 m)
1/2" (12 mm)
Two−Pipe System
When using a two−pipe system with the oil tank below
the level of the burner, a single−stage fuel pump should
be used in lift conditions of up to 10 feet (3 m) and/or a
vacuum of 10" (254 mm) Hg or less. See figure 17. Use a
two−stage fuel pump when lift exceeds 10 feet (3 m) and/
or a vacuum of 10" (254 mm) Hg to 15" (381 mm) Hg. Both
conditions require that you use a two−pipe system, which con-
sists of a return line that purges the fuel pump of air by return-
ing it to the tank. To determine the run and lift for piping, refer to
table 5 .
To determine the length of the run for piping, refer to table 4 .
Figure 17
Oil Piping
ÎÎÎÎÎ
ÎÎÎÎÎ
ÎÎ
ÎÎÎÎÎÎÎÎÎÎ
ÎÎ
ÎÎ
ÎÎ
ÎÎ
ÎÎÎ
fuel
pump
Aux
Filter
Return
pipe
Fill
Pipe
Air Vent
Oil
Tank
Inlet
Return
pipe
H
3" 4"
(76 mm 102 mm)
R
outside tank fuel pump above bottom of tank.
Two-Pipe System
Use continuous lengths of heavy wall copper tubing or
steel pipe for oil supply pipe. Install oil supply pipe under
floor or near walls to protect it from damage. Avoid running
pipes along joists or reverberating surfaces. Always use
flare fittings. All fittings must be accessible. Do not use
compression fittings.
IMPORTANT
Both oil supply and return pipes must be submerged
in oil in the supply tank.
Table 5
Two−Pipe Maximum Pipe Length (H + R)
3450 RPM − 3 GPH (11.4 LPH)
Lift H"
3/8" (10 mm) OD
Tubing
1/2" (12 mm) OD
Tubing
Single
Stage
Two
Stage
Single
Stage
Two
Stage
0’
(0.0 m)
84’
(25.6 m)
93’
(28.3 m)
100’
(30.5 m)
100’
(30.5 m)
2’
(0.6 m)
73’
(22.3 m)
85’
(25.9 m)
100’
(30.5 m)
100’
(30.5 m)
4’
(1.2 m)
63’
(19.2 m)
77’
(23.5 m)
100’
(30.5 m)
100’
(30.5 m)
6 ’
(1.8m)
52’
(15.8 m)
69’
(21.0 m)
100’
(30.5 m)
100’
(30.5 m)
8’
(2.4 m)
42’
(12.8 m)
60’
(18.3 m)
100’
(30.5 m)
100’
(30.5 m)
10’
(3.0 m)
31’
(9.4 m)
52’
(15.9 m)
100’
(30.5 m)
100’
(30.5 m)
12’
(3.7 m)
21’
(6.4 m)
44’
(13.4 m)
83’
(25.3 m)
100’
(30.5 m)
14’
(4.3 m)
−−−
36’
(11.0 m)
41’
(12.5 m)
100’
(30.5 m)
16’
(4.9 m)
−−−
27’
(8.2 m)
−−−
100’
(30.5 m)
18’
(5.5 m)
−−−
−−−
−−−
76’
(23.2 m)