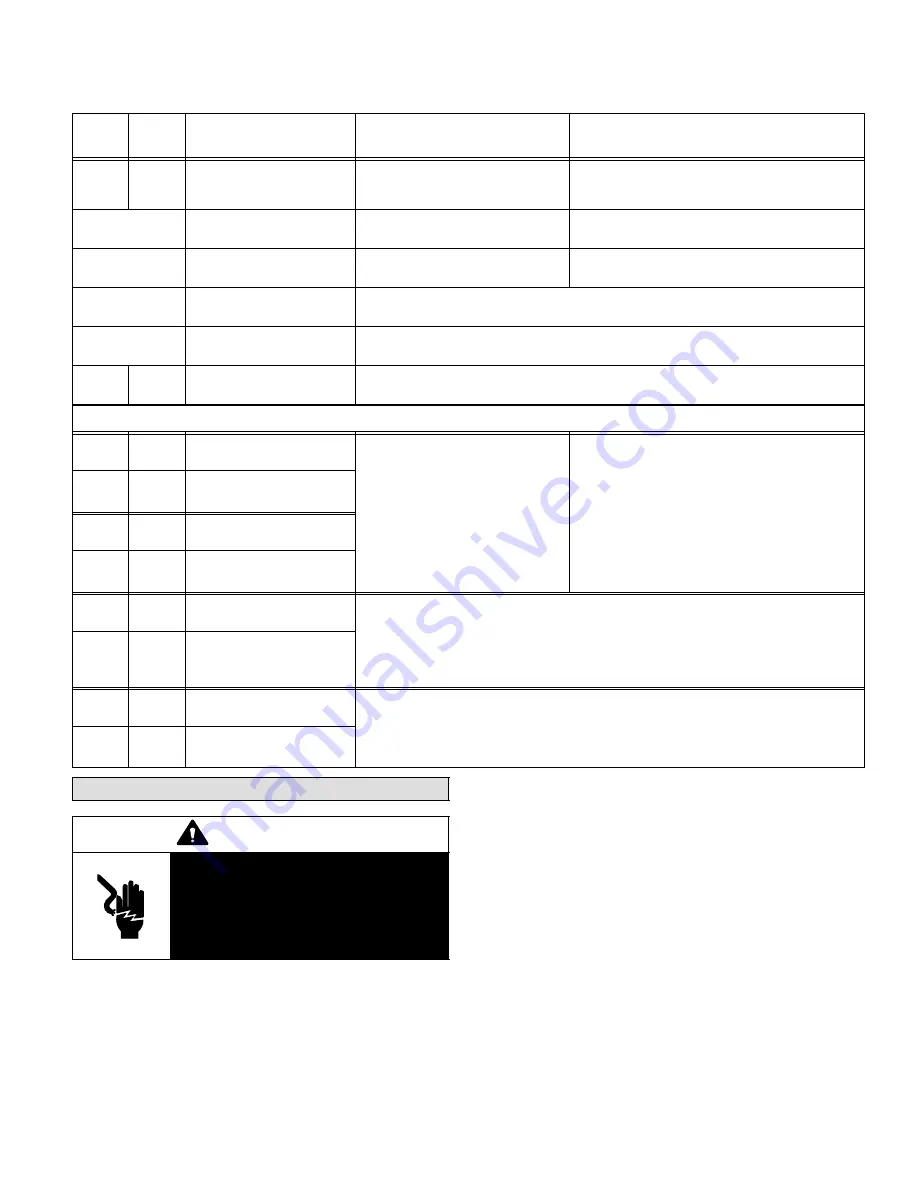
Page 29
XP19 SERIES
DCB DIAGNOSTICS
See Table 15 to determine DCB operational conditions and to diagnose cause and solution to problems.
Table 15. Defrost Control Board Diagnostic LEDs
DS2
Green
DS1
Red
Condition/Code
Possible Cause(s)
Solution
OFF
OFF
Power problem
No power (24V) to board terminals R
and C or board failure.
1
Check control transformer power (24V).
2
If power is available to board and LED(s) do not
light, replace board.
Simultaneous
SLOW Flash
Normal operation
Unit operating normally or in standby
mode.
None required.
Alternating SLOW
Flash
5−minute anti−short cycle
delay
Initial power up, safety trip, end of
room thermostat demand.
None required (Jumper TEST pins to override)
Simultaneous
FAST Flash
Ambient Sensor Problem
Sensor being detected open or shorted or out of temperature range. Board will revert to time/
temperature defrost operation. (System will still heat or cool).
Alternating
FAST Flash
Coil Sensor Problem
Sensor being detected open or shorted or out of temperature range. Board will not perform
demand or time/temperature defrost operation. (System will still heat or cool).
ON
ON
Circuit Board Failure
Indicates that board has internal component failure. Cycle 24 volt power to board. If code does
not clear, replace board.
FAULT and LOCKOUT CODES
(Each fault adds 1 strike to that code’s counter; 5 strikes per code = LOCKOUT)
OFF
SLOW
Flash
Low Pressure Fault
1
Restricted air flow over indoor or out-
door coil.
2
Improper refrigerant charge in sys-
tem.
3
Improper metering device installed or
incorrect operation of metering de-
vice.
4
Incorrect or improper sensor location
or connection to system.
1
Remove any blockages or restrictions from coils
and/or fans. Check indoor and outdoor fan motor for
proper current draws.
2
Check system charge using approach and subcool-
ing temperatures.
3
Check system operating pressures and compare to
unit charging charts.
4
Make sure all pressure switches and sensors have
secure connections to system to prevent refrigerant
leaks or errors in pressure and temperature mea-
surements.
OFF
ON
Low Pressure
Discharge
Sensor Lockout
SLOW
Flash
OFF
High Pressure Fault
ON
OFF
High Pressure
Discharge
Sensor Lockout
SLOW
Flash
ON
Discharge Line Temperature
Fault
This code detects shorted sensor or high discharge temperatures. If the discharge line
temperature exceeds a temperature of 300ºF (148ºC) during compressor operation, the board
will de−energize the compressor contactor output (and the defrost output if active). The
compressor will remain off until the discharge temperature has dropped below 225ºF (107ºC).
FAST
Flash
ON
Discharge Line
Temperature
Discharge
Sensor Lockout
OFF
Fast
Flash
Discharge Sensor Fault
The board detects open sensor or out of temperature sensor range. This fault is detected by
allowing the unit to run for 90 seconds before checking sensor resistance. If the sensor resist-
ance is not within range after 90 seconds, the board will count one fault. After 5 faults, the board
will lockout.
Fast
Flash
OFF
Discharge Sensor
Discharge Sensor Lockout
Maintenance23
WARNING
Electric shock hazard. Can cause inju-
ry or death. Before attempting to per-
form any service or maintenance, turn
the electrical power to unit OFF at dis-
connect switch(es). Unit may have
multiple power supplies.
Before the start of each heating and cooling season, the
following service checks should be performed by a
qualified service technician. First, turn off electrical power
to the unit prior to performing unit maintenance.
S
Inspect and clean the outdoor and indoor coils. The
outdoor coil may be flushed with a water hose.
NOTE It may be necessary to flush the outdoor coil
more frequently if it is exposed to substances which are
corrosive or which block airflow across the coil (e.g., pet
urine, cottonwood seeds, etc.)
S
Visually inspect the refrigerant lines and coils for leaks.
S
Check wiring for loose connections.
S
Check voltage at the indoor and outdoor units (with
units operating).
S
Check the amperage draw at the outdoor fan motor,
compressor, and indoor blower motor. Values should
be compared with those given on unit nameplate.
S
Check, clean (or replace) indoor unit filters.
S
Check the refrigerant charge and gauge the system
pressures.
S
Check the condensate drain line for free and
unobstructed flow; clean, if necessary.