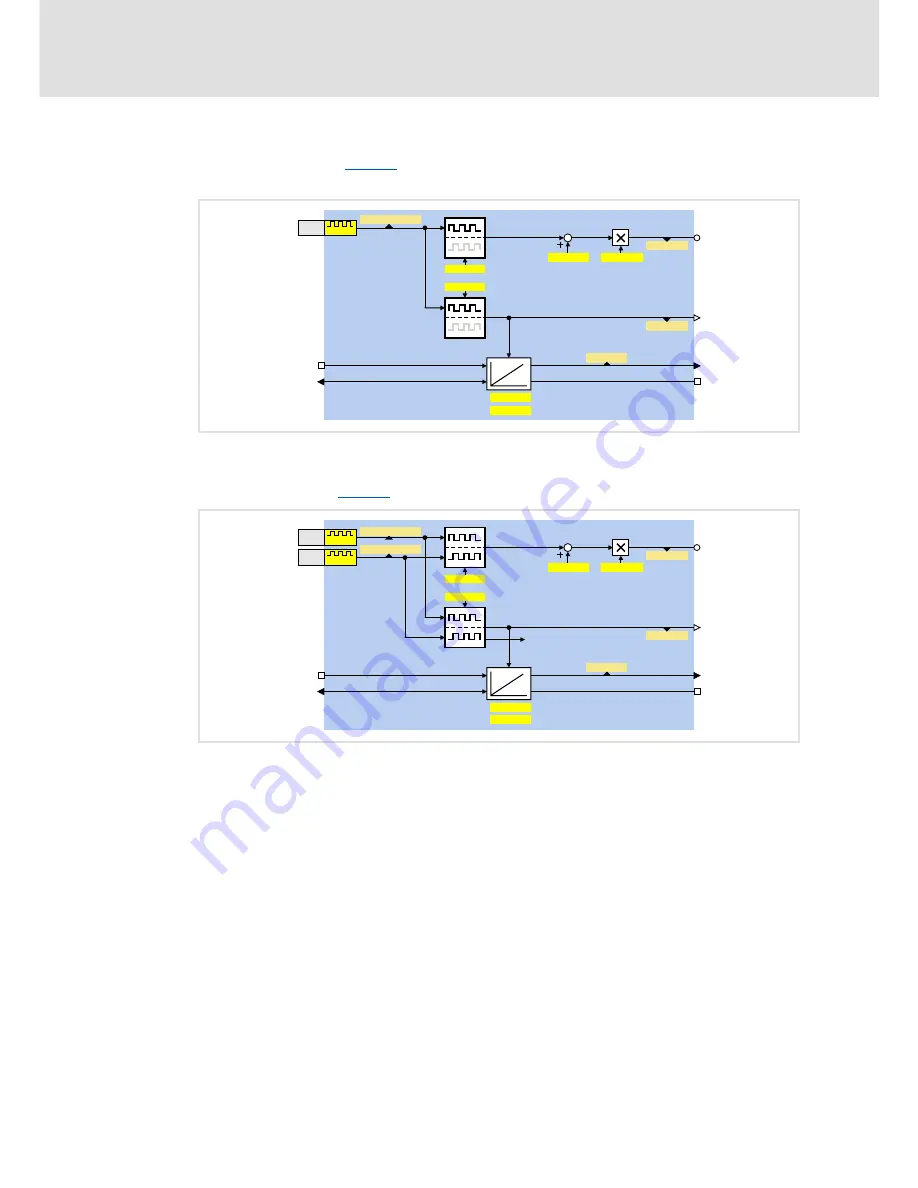
8400 StateLine C | Reference manual
I/O terminals
Digital terminals
260
L
Firmware
≤
11.00 - DMS 8.0 EN - 10/2011
Function assignment 1: DI1=FreqIn / DI2=In
Select this setting in
C00115
to configure input terminal DI1 as a frequency input. The
input terminal DI2 remains configured as a "normal" digital input.
Function assignment 2: DI1&DI2=FreqIn (2-track)
Select this setting in
C00115
to connect a two-track encoder to terminals DI1/DI2.
Q)UHT,QBD
2IIVHW
*DLQ
&
&
Q)UHT,QBY
&
&
&
&
',
N+]
&%LW
GQ3RV,QBS
&
&
&RPSDUHYDOXH
)XQFWLRQ
E3RV,QB6WDWH
E3RV,QB/RDG
GQ3RV,QB6HWBS
&
Q)UHT,QBD
2IIVHW
*DLQ
&
&
Q)UHT,QBY
&
&
&
&
',
',
N+]
N+]
&%LW
&%LW
GQ3RV,QBS
&
&
&RPSDUHYDOXH
)XQFWLRQ
E3RV,QB6WDWH
E3RV,QB/RDG
GQ3RV,QB6HWBS
&
0&75/B6SHHGIHHGEDFN
Phone: 800.894.0412 - Fax: 888.723.4773 - Web: www.clrwtr.com - Email: info@clrwtr.com