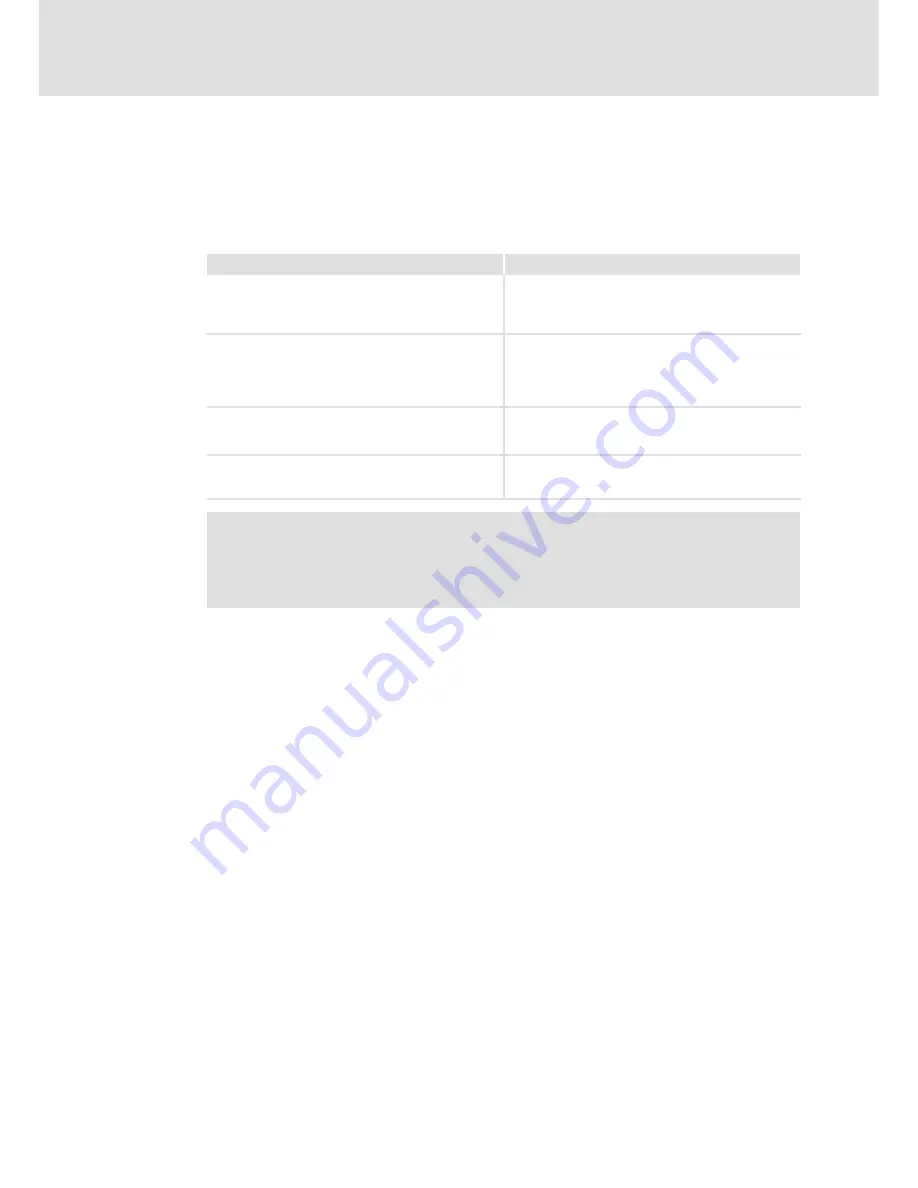
Commissioning
Speed control
Making the controller ready for operation
5
44
SW-HB 13.0002-EN EN 3.0
5.2.9
Making the controller ready for operation
After controller enable, the shaft must start rotating. Unless the motor shows this
behaviour, an error has occurred or the 931E servo positioning controller has not been
parameterised correctly. In the below table, you can find typical errors and information on
how to remove them.
Error
Remedy
The motor builds up a holding torque and ”snaps” in
different positions.
Pole pair number and/or phase sequence are wrong.
Select the correct pole pair number and/or change the
motor phases. Repeat the automatic identification. See
the chapter ”Motor data”.
134
The motor shaft vibrates and does not run smoothly.
The selected angle encoder offset and/or controller
parameters are not correct. See the chapter ”Speed
control”.
40
Repeat the automatic identification. See the chapter
”Angle encoder”.
136
The shaft does not rotate.
z
No DC-bus voltage.
z
The limit switches are active.
z
”Quick stop” (DIN 6) has not been assigned correctly.
The shaft does not rotate. The actual value window
displays the speed setpoint = ”0”.
The speed setpoint has not been configured correctly.
See the chapter ”Setpoint selection via setpoint
selectors”.
33
Stop!
When connecting the motor phases, please observe that the individual servo
motor manufacturers may define different phase sequences. If necessary,
change W and U phase.
efesotomasyon.com - Lenze