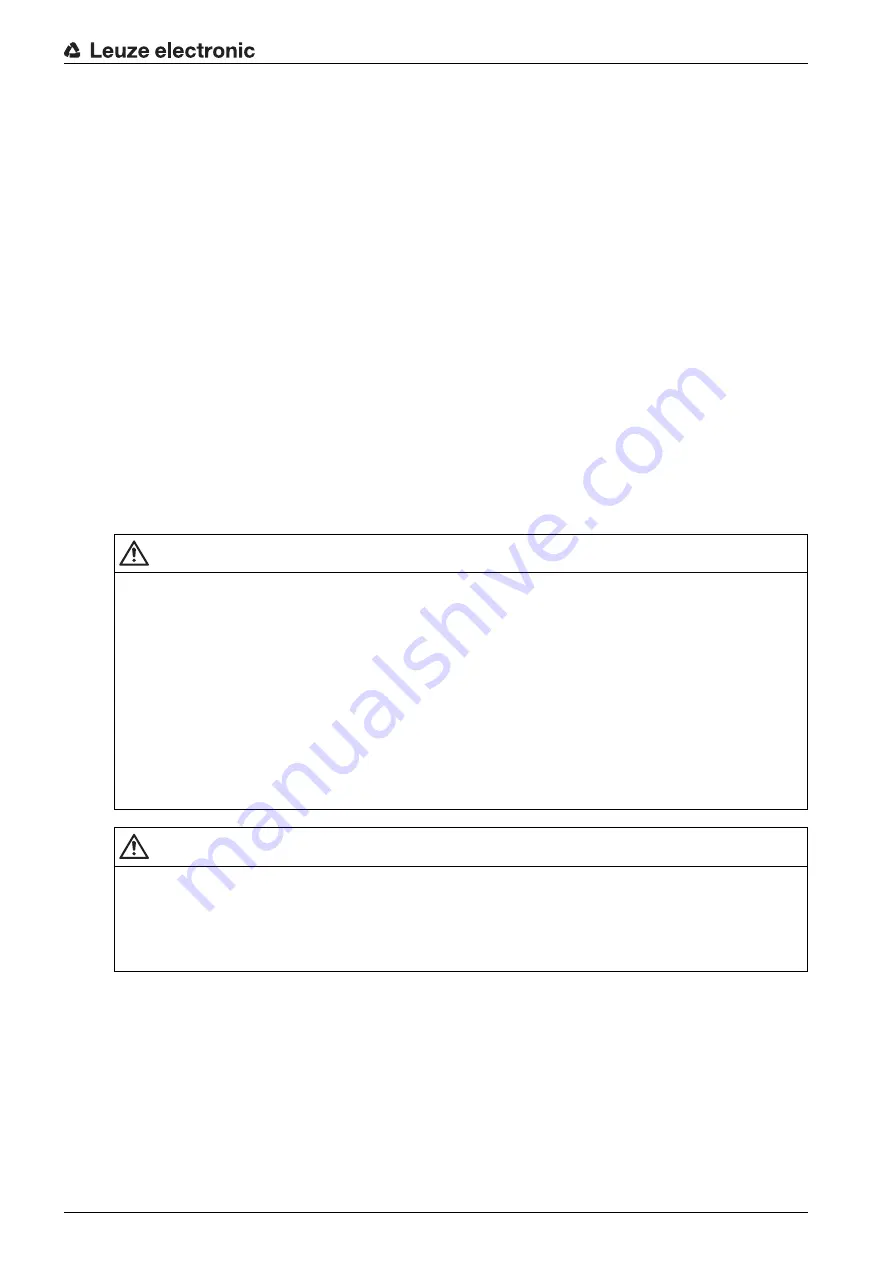
Configuring the safety sensor
Leuze electronic
RSL 410
62
9
Configuring the safety sensor
To start up the safety sensor in your application, the safety sensor must be individually adapted using the
software. All configuration data is defined using the configuration and diagnostics software.
General procedure for configuring safety sensor
Assessing the risk
• The system has been determined and its boundaries defined.
• The safety sensor has been selected as the safety component.
• The type of guarding has been determined (danger zone guarding, point of operation guarding,
access guarding).
Calculating safety distance
Shape and size of the protective and warning fields
Configuring the safety sensor
• Configuration and diagnostics software (see chapter 4 "Configuration and diagnostic software
• Determine the configuration project (see chapter 9.3 "Determining configuration project")
• Configure the protective function (see chapter 9.4 "Configuring protective function")
Checking function (see chapter 11 "Testing")
9.1
Defining safety configuration
WARNING
Serious accidents caused by incorrect safety configuration!
The protective function of the safety sensor is only ensured if the safety sensor is correctly configured for
the intended application.
Allow only competent persons to perform safety configuration.
Select the safety configuration so that the safety sensor can be used as intended (see chapter 2.1
Select the protective field dimensions and contours according to the safety distance calculated for the
application (see chapter 7.1.1 "Calculation of safety distance S").
Select the parameters of the safety configuration according to your risk analysis.
After start-up, check the function of the safety sensor (see chapter 11.1 "Before the initial start-up and
WARNING
Additional protection against manipulation when the monitoring time is increased!
If the monitoring time is increased to above 5 s or if manipulation protection is deactivated, the system
operator must introduce other measures to prevent manipulation.
For example, make sure that the distance range in which manipulation is possible cannot be accessed
by personnel under normal operating conditions.