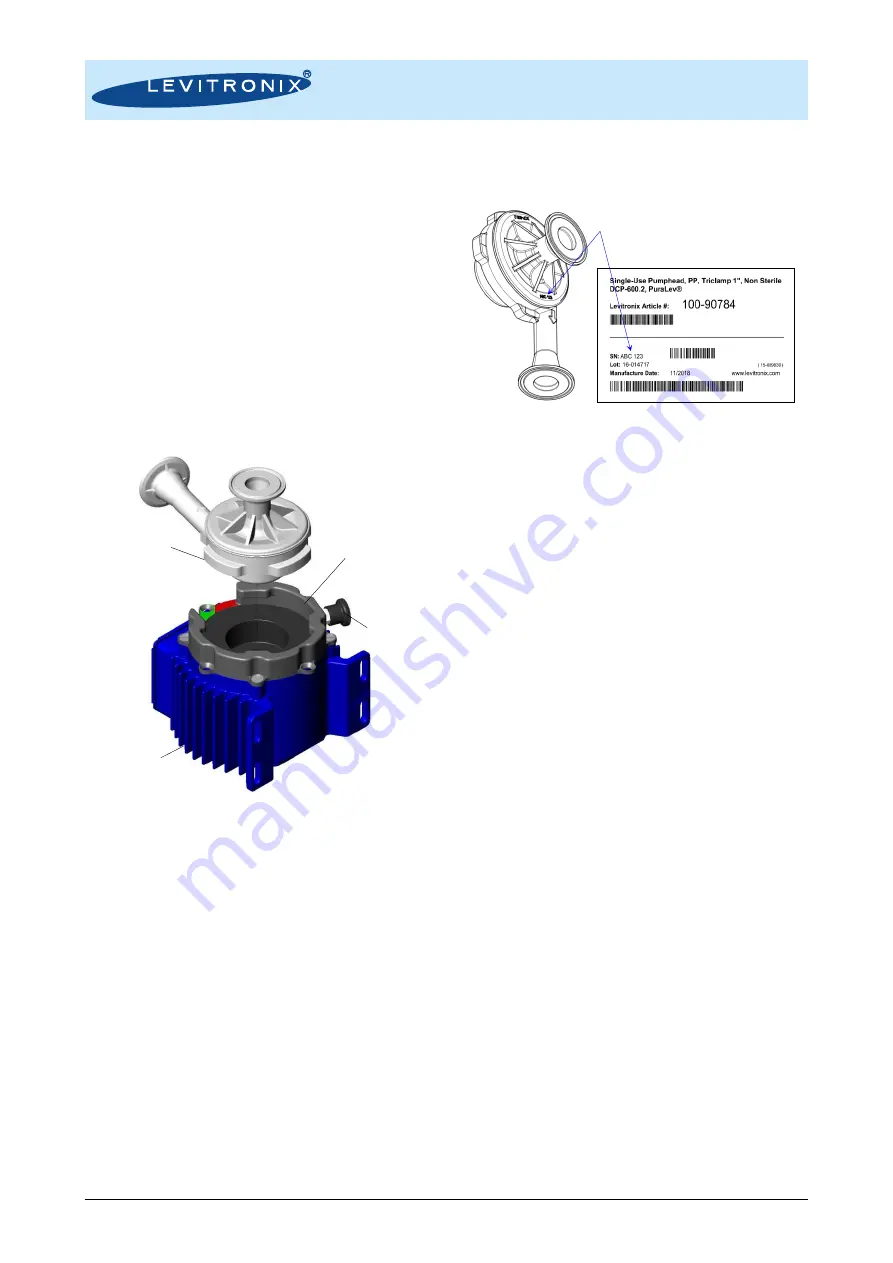
User Manual for PuraLev
®
600SU
www.levitronix.com
PL-4032-00, Rev06, DCO# 20-144
35
6
Instruction for Use of Pump Head
6.1 Description and Preparation
6.1.1 Description
The
DCP-600
pump heads are designed for single use
applications in the Life Science industries in connection
with the
PuraLev
®
600SU
pump system components.
The wetted parts are made out of biocompatible
materials (FDA, USP VI, Animal-Free), which can be
gamma sterilized.
The
Pump Head
is mounted to the
Bearingless Motor
(
MagLev
drive motor) via the
Pump Head Socket
. The
motor is connected to a controller generating the
currents for rotation and the levitation of the impeller.
Figure 36: Single-use pump head concept
Before using the
DCP-600
pump head make yourself
familiar with the following warnings, cautions and
instructions.
6.1.2 Inspection Prior to Use
The pump head should be inspected prior to use for any
damage. Do not use the pump head if any damage is
found. Contact
Levitronix
®
regarding return of any
suspected pump head.
6.1.3 Traceability for Troubleshooting
For full traceability of the pump head the 6 digit serial
number located on the top of the pump head. shall be
used. On the labels of the packaging and on the
biocompatibility declaration this serial number is the one
on
the
lid
(see
Single-Use
Pumphead
DCP-600
Pump Head Socket
(Bayonet type)
PHS-600
Locking Pin
Bearingless Motor
LPM-600.x