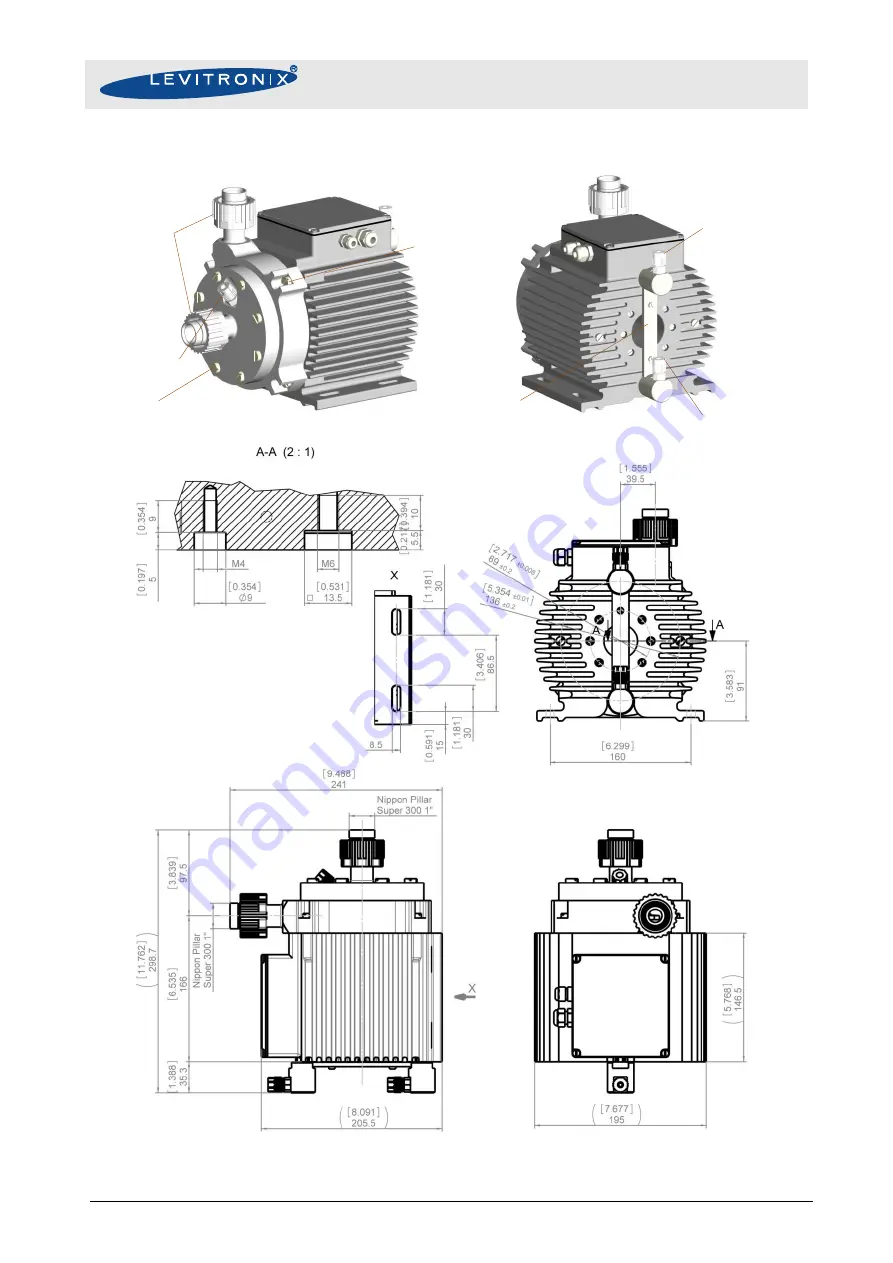
User Manual for BPS-4H (High Temp.)
www.levitronix.com
PL-2009-03, Rev04, DCO# 21-101
11
2.7 Basic Dimensions of Main Components
Figure 11:
Basic dimensions (mm/inch) of BSM-4.10 motor with pump head
CP-4.25
(Dimensions without motor housing coating of ~0.4 mm.)
Pump Head Screws
Stainless Steel + PTFE
8 pcs. M8x40 mm
Torque Spec.: 1.2 Nm
Pump/Motor Screws
Stainless Steel + PTFE
4 pcs. M8x30 mm
Torque Spec.: 1.2 Nm
Twisting protection to
prevent unscrewing
of cooling connections.
Inlet/Outlet Fittings
Pillar Super 300 1”
Suction Port
Pillar Super 300 ¼”
Cooling Circuit OUTLET
Pillar Super 300 ¼”
Cooling Circuit INLET
Pillar Super 300 ¼”