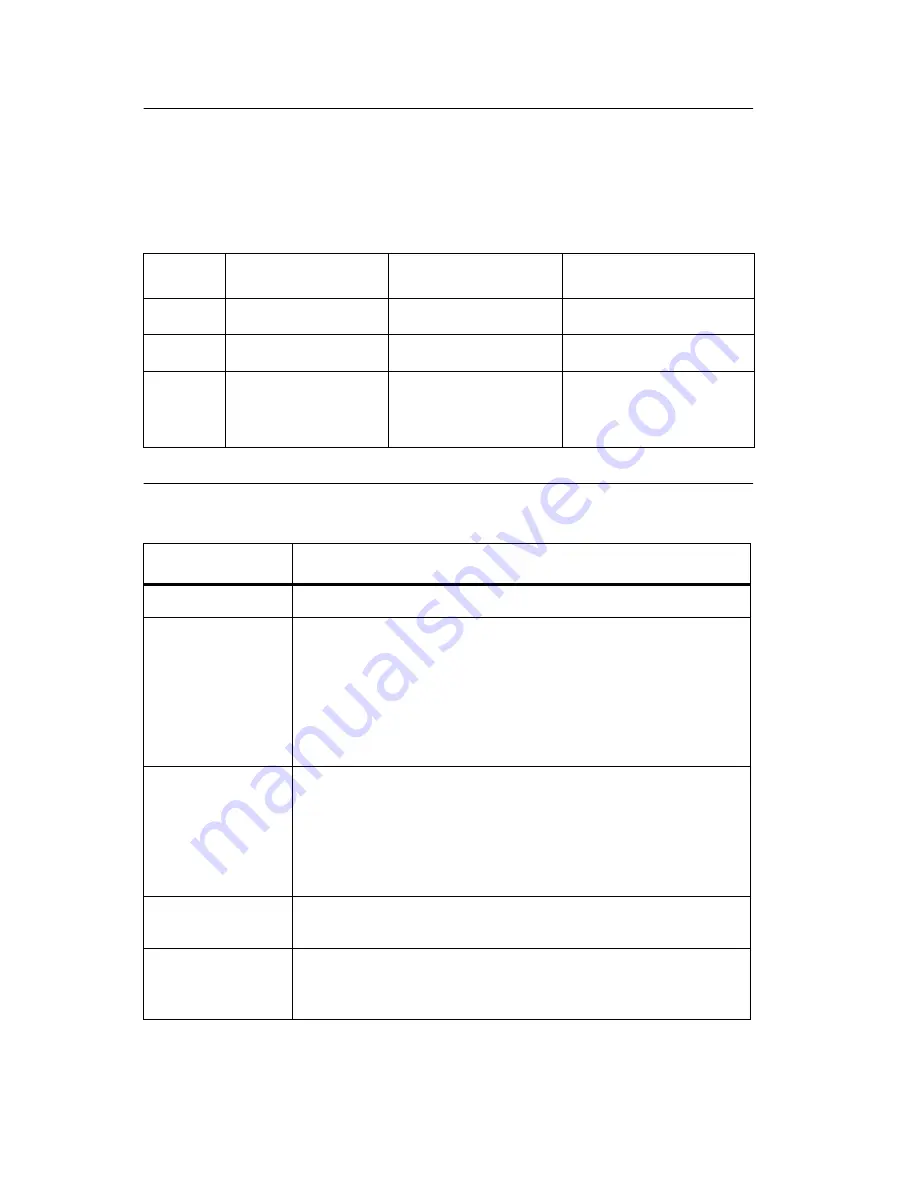
1-2
Service Manual
5016-001
Models
The 5016-001 printer is available in the following models:
Standard Features
Model
Memory
INA
Options
C710
32 MB
N/A
N/A
C710n
32 MB
10 Base 100T
N/A
C710dn
64 MB
10 Base 100T
• Additional 2x250
paper drawer
• Duplex
Feature
Description
Printing Process
Dry electrophotographic process using a laser diode.
Performance
• Monochrome, Letter or A4 - up to 16 ppm.
• Color, Letter or A4 - up to 3ppm.
• Color transparencies, Letter or A4 - up to 1.8 ppm.
• Monochrome duplexed pages, up to 10 impressions -
5 duplexed ppm.
• Color duplexed pages, up to 3 impressions - 1.5
duplexed ppm.
Special Features
• Automatic Duplex.
• Color Quality Enhancement Technology (CQET).
• Automatic color screening selection to optimize print
quality based on print type.
• 4 bit color capabilities.
• Color screens which optimize print quality.
Print
Addressability
600 x 600 dpi, 1200 x 1200 dpi
Maximum Print
Speed
(Mono/Color)
16/3 ppm (Letter and A4)
Summary of Contents for Optra C710
Page 17: ...Notices and Safety Information xvii 5016 001 Japanese Laser Notice Chinese Laser Notice ...
Page 18: ...xviii Service Manual 5016 001 Korean Laser Notice ...
Page 23: ...Notices and Safety Information xxiii 5016 001 Korean ...
Page 24: ...xxiv Service Manual 5016 001 ...
Page 44: ...1 20 Service Manual 5016 001 ...
Page 198: ...2 132 Service Manual 5016 001 ...
Page 222: ...3 24 Service Manual 5016 001 ...
Page 232: ...4 10 Service Manual 5016 001 LVPS Assembly Removal ...
Page 250: ...4 28 Service Manual 5016 001 ...
Page 251: ...Connector Locations 5 1 5016 001 5 Connector Locations Engine Board ...
Page 260: ...5 10 Service Manual 5016 001 Electrical Components Sensor Switch Locations ...
Page 263: ...Connector Locations 5 13 5016 001 Printer Circuit Board Locations Fan Motor Locations ...
Page 264: ...5 14 Service Manual 5016 001 Solenoid Clutch Locations ...
Page 268: ...5 18 Service Manual 5016 001 ...
Page 270: ...6 2 Service Manual 5016 001 ...
Page 272: ...7 2 Service Manual 5016 001 Assembly 1 Fuser ...
Page 274: ...7 4 Service Manual 5016 001 Assembly 2 Fuser ...
Page 276: ...7 6 Service Manual 5016 001 Assembly 2 Cont Fuser ...
Page 278: ...7 8 Service Manual 5016 001 Assembly 3 Transfer ...
Page 280: ...7 10 Service Manual 5016 001 Assembly 4 Frames ...
Page 282: ...7 12 Service Manual 5016 001 Assembly 5 Frames Left Side ...
Page 284: ...7 14 Service Manual 5016 001 Assembly 5 Cont Frames Left Side ...
Page 286: ...7 16 Service Manual 5016 001 Assembly 6 Frames Right Side ...
Page 288: ...7 18 Service Manual 5016 001 Assembly 6 Cont Frames Right Side ...
Page 290: ...7 20 Service Manual 5016 001 Assembly 7 Frames Right Side 2 ...
Page 292: ...7 22 Service Manual 5016 001 Assembly 7 Cont Frames Right Side 2 ...
Page 294: ...7 24 Service Manual 5016 001 Assembly 8 Frames Right Side 3 ...
Page 296: ...7 26 Service Manual 5016 001 Assembly 9 Carriage Block ...
Page 298: ...7 28 Service Manual 5016 001 Assembly 10 Base Frame ...
Page 300: ...7 30 Service Manual 5016 001 Assembly 11 Front Cover Assembly ...
Page 302: ...7 32 Service Manual 5016 001 Assembly 11 Cont Front Cover Assembly ...
Page 304: ...7 34 Service Manual 5016 001 Assembly 12 Front Cover Assembly 2 ...
Page 306: ...7 36 Service Manual 5016 001 Assembly 12 Cont Front Cover Assembly 2 ...
Page 308: ...7 38 Service Manual 5016 001 Assembly 13 Feed Unit ...
Page 310: ...7 40 Service Manual 5016 001 Assembly 14 Laser Scanner Unit ...
Page 312: ...7 42 Service Manual 5016 001 Assembly 14 Cont Laser Scanner Unit ...
Page 314: ...7 44 Service Manual 5016 001 Assembly 15 Cassette ...
Page 316: ...7 46 Service Manual 5016 001 Assembly 16 Upper Covers ...
Page 318: ...7 48 Service Manual 5016 001 Assembly 16 Cont Upper Covers ...
Page 320: ...7 50 Service Manual 5016 001 Assembly 17 Covers ...
Page 322: ...7 52 Service Manual 5016 001 Assembly 18 Covers Frame 250 Tray Option ...
Page 324: ...7 54 Service Manual 5016 001 Assembly 18 Cont Covers Frame 250 Option ...
Page 326: ...7 56 Service Manual 5016 001 Assembly 19 Middle Roll Unit 250 Tray Option ...
Page 328: ...7 58 Service Manual 5016 001 Assembly 20 250 250 Tray Option Lower Unit ...
Page 330: ...7 60 Service Manual 5016 001 Assembly 21 Duplex Unit Option 2 ...
Page 332: ...7 62 Service Manual 5016 001 Assembly 21 Cont Duplex Unit Option 2 ...
Page 334: ...7 64 Service Manual 5016 001 Assembly 22 Cassette Upper Section ...
Page 336: ...7 66 Service Manual 5016 001 Assembly 23 Cassette Rear Section 1 ...
Page 338: ...7 68 Service Manual 5016 001 Assembly 24 Cassette Rear Section 2 ...
Page 340: ...7 70 Service Manual 5016 001 Assembly 25 Duplex Option Lower Section 1 ...
Page 342: ...7 72 Service Manual 5016 001 Assembly 25 Cont Duplex Lower Section 1 ...
Page 344: ...7 74 Service Manual 5016 001 Assembly 26 Duplex Option Lower Section 2 ...
Page 346: ...7 76 Service Manual 5016 001 Assembly 27 Duplex Option Lower Section 3 ...
Page 348: ...7 78 Service Manual 5016 001 Assembly 28 Cassette Lower Section 4 ...
Page 350: ...7 80 Service Manual 5016 001 Assembly 29 Duplex Option Lower Section 5 ...
Page 352: ...7 82 Service Manual 5016 001 Assembly 29 Cont Duplex Option Lower 5 ...
Page 367: ......
Page 368: ......
Page 369: ......