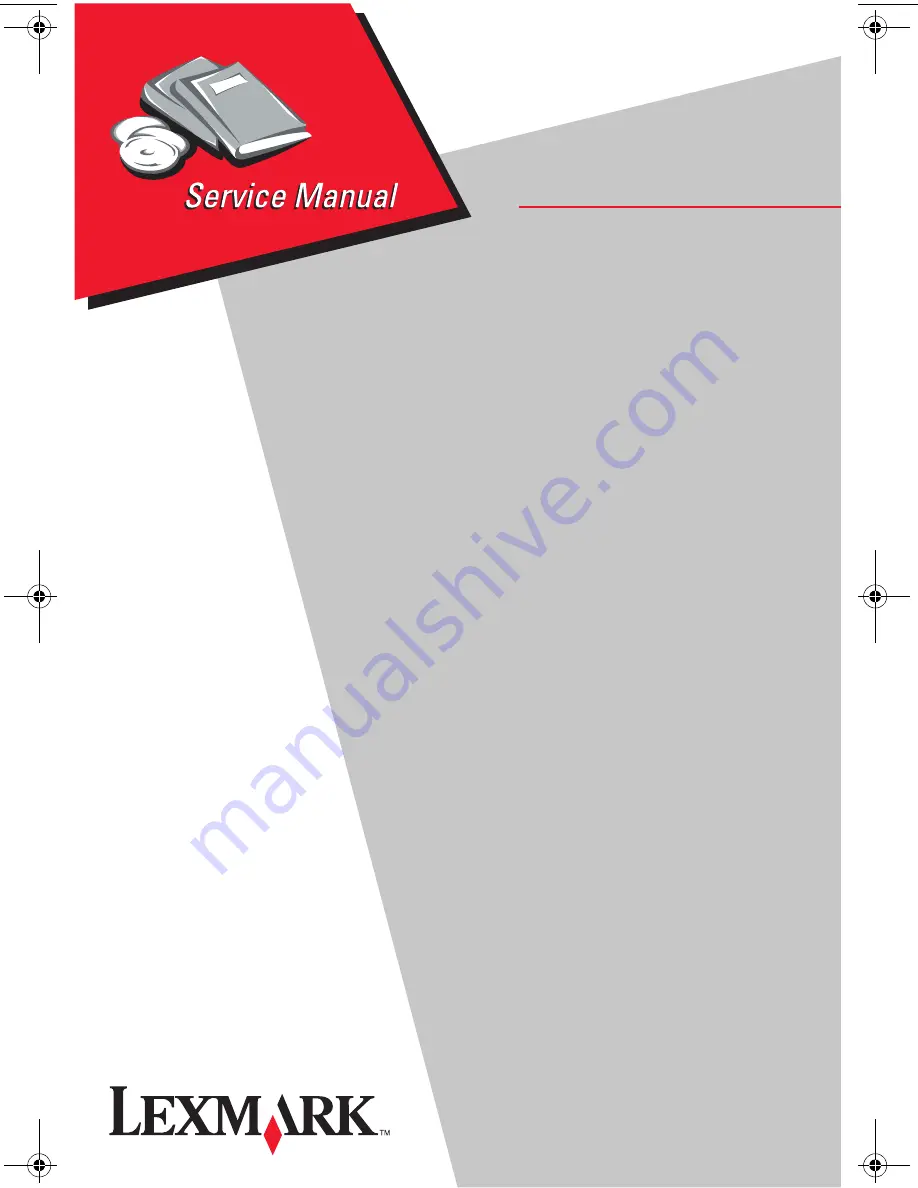
4102-P01
Lexmark and Lexmark with diamond
design are trademarks of Lexmark
International, Inc., registered in the
United States and/or other countries.
• Table of Contents
• Index
• Safety and Notices
• Trademarks
• Start Diagnostics
• Manuals Menu
Lexmark P122 Photo Jetprinter
Service.bk Page i Tuesday, February 13, 2001 2:40 PM
Summary of Contents for P122 Photo Jetprinter
Page 10: ...x Service Manual 4102 P01 ...
Page 16: ...1 6 Service Manual 4102 P01 ...
Page 32: ...2 16 Service Manual 4102 P01 ...
Page 54: ...5 2 Service Manual 4102 P01 ...
Page 58: ...6 2 Service Manual 4102 P01 ...
Page 60: ...7 2 Service Manual 4102 P01 Assembly 1 Covers ...
Page 62: ...7 4 Service Manual 4102 P01 Assembly 2 Carrier Assembly ...
Page 64: ...7 6 Service Manual 4102 P01 Assembly 3 Electronics ...
Page 66: ...7 8 Service Manual 4102 P01 Assembly 4 Frame Assembly ...