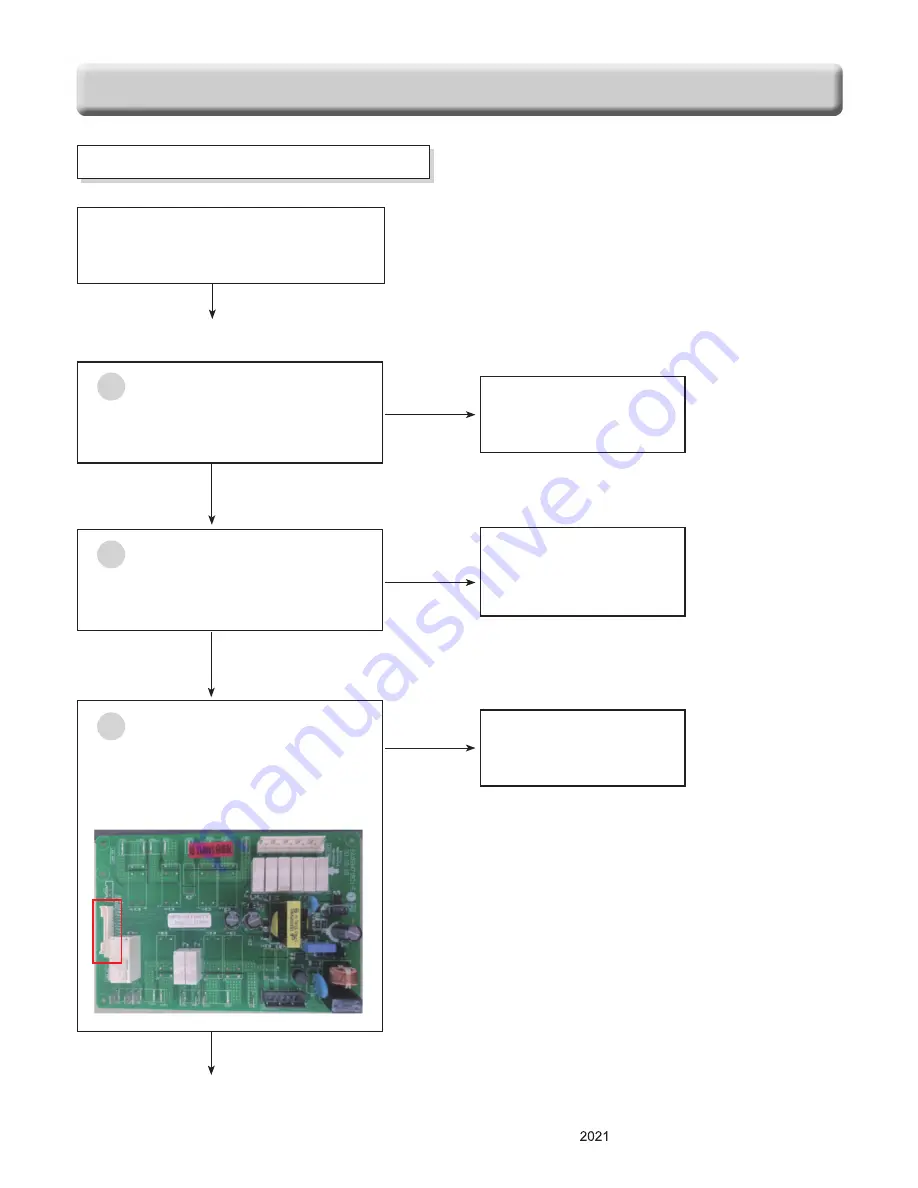
10-2
Copyright ©
LG Electronics Inc. All rights reserved.
Only training and service purposes
CHECKING FLOW CHART BY FAILURE
No display (No power)
Check the connection of Main PCB
(CN10), Power PCB (CN02)
Normal?
Yes
No
Yes
Plug the unit
Power Failed (Dead),
No display?
Check the button beep.
Touch the display key pad,
Can hear the beep sound?
Go to 7
(On the next Page)
No
Reconnect. If defective
harness, replace or fix
1
No
Yes
Check the connection of Power
Cord. Normal?
Reconnect.
If defective harness,
replace or fix
2
3
Summary of Contents for LSGL6337D
Page 88: ......