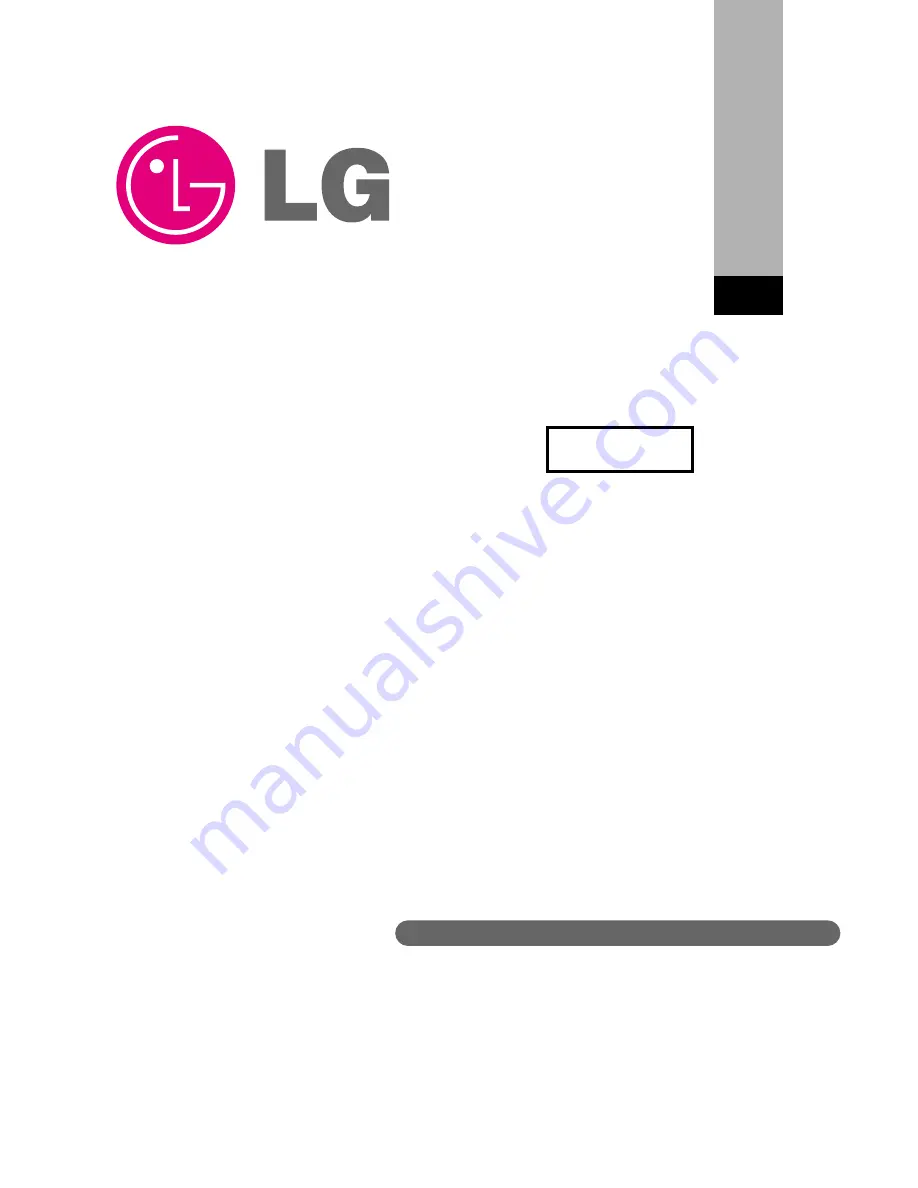
Operation & Maintenance Manual
LG
MODELS: RCAW - Compact (50Hz)
website http://www.lgservice.com
IMPORTANT
• Please read this Operation & Maintenance Manual
completely before Operating & Maintenance the product.
• Operating & Maintenance must be performed in
accordance with the national wiring standards by
authorized personnel only.
• Please retain this Operating & Maintenance for future
reference after reading it thoroughly.
R134a
Chiller
Air-cooled Screw