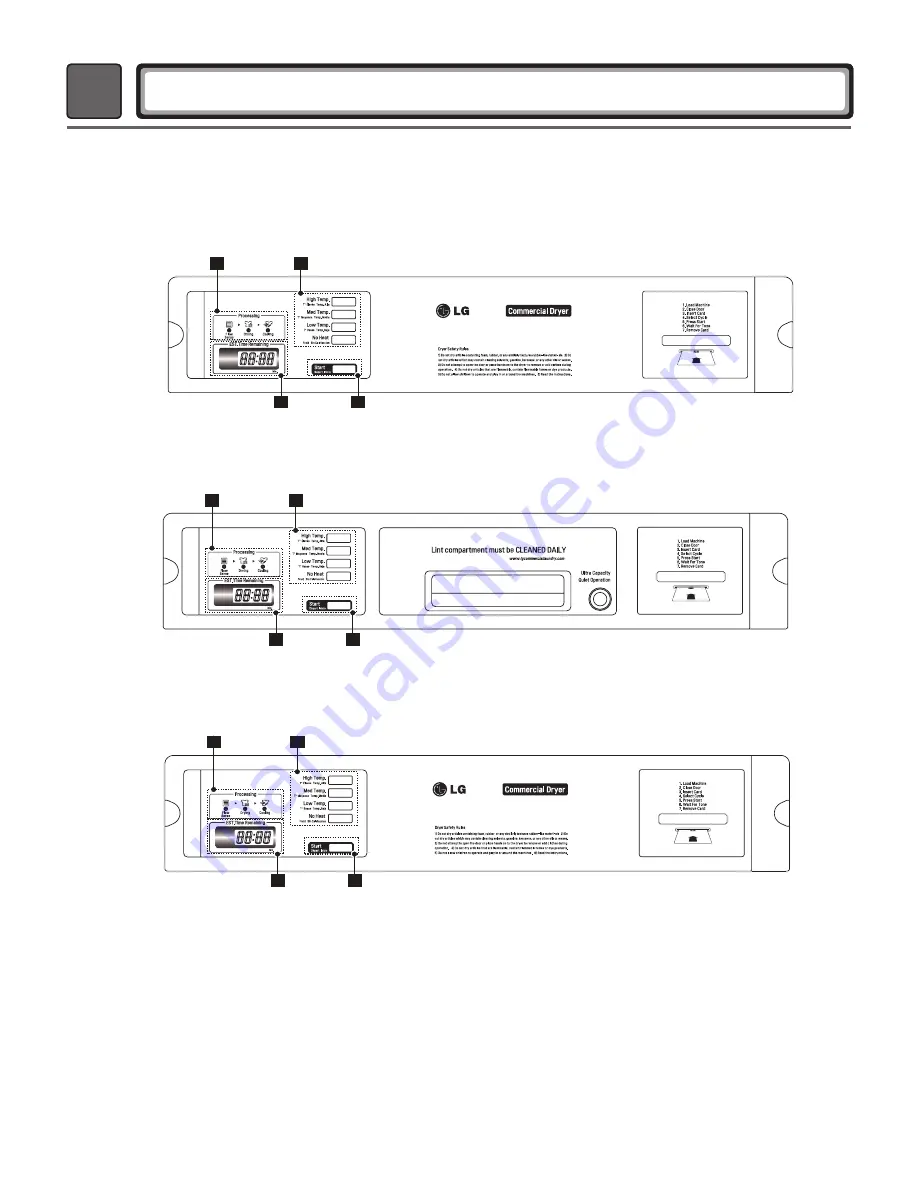
1
SPECIFICATIONS
12
3
FEATURES AND BENEFITS
1. DISPLAY LED
2. CYCLE BUTTON
3. START BUTTON
4. STATUS LED
■
COIN/OPL TYPE
- SIDE BY SIDE(TCD1870CGS)
■
STACK (TCD1870CGG)
- UPPER
- LOWER
1
4
3
2
1
4
3
2
1
4
3
2
1
4
3
2
1
4
3
2
1
4
3
2
1
3
4
2
1
3
4
2
1
3
4
2
1
3
4
2
1
3
4
2
1
3
4
2
1
4
3
2
1
4
3
2
1
4
3
2
1
4
3
2
1
4
3
2
1
4
3
2
1
3
4
2
1
3
4
2
1
3
4
2
1
3
4
2
1
3
4
2
1
3
4
2
1
4
3
2
1
4
3
2
1
4
3
2
1
4
3
2
1
4
3
2
1
4
3
2
1
3
4
2
1
3
4
2
1
3
4
2
1
3
4
2
1
3
4
2
1
3
4
2
Summary of Contents for TCD1870CGG
Page 5: ...5 ...
Page 6: ...6 ...
Page 7: ...7 ...
Page 8: ...8 ...
Page 9: ...9 Gw G G G G G Gz G Gj G G G G G G G G G G UG G G G U ...
Page 14: ...14 4 INITIAL STEPS FOR INSTALLING YOUR DRYER ...
Page 18: ...18 z lwG GConnection of Gas Supply z lwG GElectrical Plug Connection ...
Page 31: ...31 11 MOTOR DIAGRAM AND SCHEMATIC ...
Page 32: ...12 CONTROL LAY OUT 32 PWB ASSEMBLY DISPLAY LAY OUT PWB ASSEMBLY LAY OUT ...
Page 33: ...33 PWB ASSEBMBLY SUB LAY OUT ...
Page 36: ...36 Test 1 Thermistor Test Measure with Power Off ...