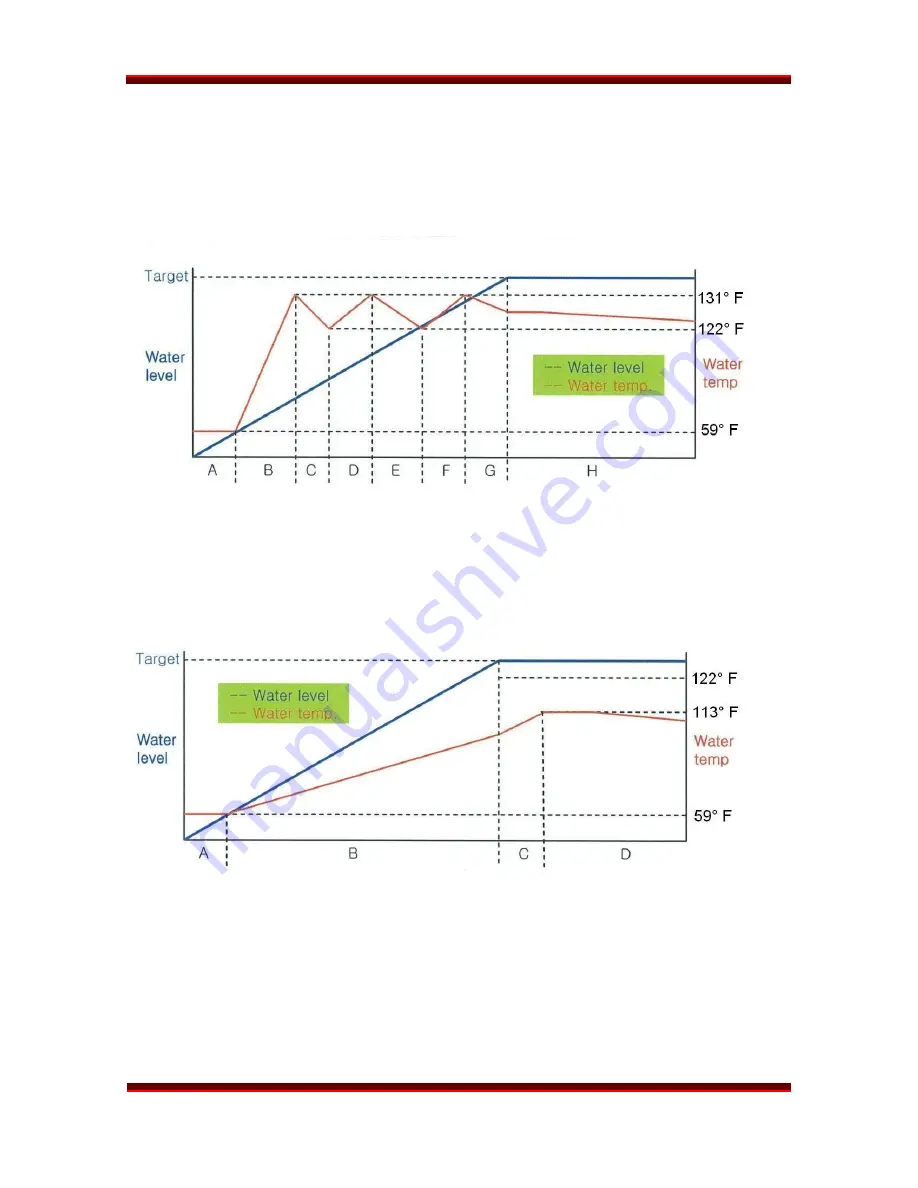
TRAINING MANUAL
WM0742HGA
WM0742HGA Page
26
TRAINING
MANUAL
A
Prewash valve opens, cold water is supplied.
B, D, and F
Hot valve opens to raise the water temperature to 131
°
F.
C, E, and G
Cold valve opens to lower the water temperature to 122
°
F.
H
No water is supplied because the water level reaches the target.
Example 1
In example 2, HOT / COLD temperatures are chosen for a NORMAL cycle. The prewash
valve is opened and cold water is supplied briefly, then the hot valve is opened and water
fills the tub to the target water level. This water never reaches the set point, so the
heater is energized. When the water temperature reaches 122
°
F, the heater is turned off.
A
Prewash valve opens, cold water is supplied.
B
Hot valve opens to raise the water temperature to 122
°
F.
C
No cold water is supplied because it has already reached the target level.
D
Heater turns off when the water reaches the target temperature of 122
°
F.
Summary of Contents for WM0742HGA
Page 1: ...LG TRAINING MANUAL LG TRAINING MANUAL Steam Washer WM0742H A Fall 2008 ...
Page 29: ...TRAINING MANUAL WM0742HGA WM0742HGA Page 27 TRAINING MANUAL WIRING DIAGRAM ...
Page 32: ...TRAINING MANUAL WM0742HGA WM0742HGA Page 30 TRAINING MANUAL DISPENSER HOSE CONNECTIONS ...
Page 57: ...TRAINING MANUAL WM0742HGA WM0742HGA Page 55 TRAINING MANUAL ERROR CODES continued ...
Page 70: ...TRAINING MANUAL WM0742HGA WM0742HGA Page 68 TRAINING MANUAL MAIN BOARD ...
Page 71: ...TRAINING MANUAL WM0742HGA WM0742HGA Page 69 TRAINING MANUAL EXPLODED VIEW CABINET ASSEMBLY ...
Page 72: ...TRAINING MANUAL WM0742HGA WM0742HGA Page 70 TRAINING MANUAL DRUM and TUB ASSEMBLY ...
Page 73: ...TRAINING MANUAL WM0742HGA WM0742HGA Page 71 TRAINING MANUAL DISPENSER ASSEMBLY ...
Page 81: ...TRAINING MANUAL WM0742HGA WM0742HGA Page 79 TRAINING MANUAL SERVICE BULLETINS ...
Page 82: ...TRAINING MANUAL WM0742HGA WM0742HGA Page 80 TRAINING MANUAL ...
Page 83: ...TRAINING MANUAL WM0742HGA WM0742HGA Page 81 TRAINING MANUAL ...
Page 84: ...TRAINING MANUAL WM0742HGA WM0742HGA Page 82 TRAINING MANUAL ...
Page 85: ...TRAINING MANUAL WM0742HGA WM0742HGA Page 83 TRAINING MANUAL ...
Page 86: ...TRAINING MANUAL WM0742HGA WM0742HGA Page 84 TRAINING MANUAL ...
Page 87: ...TRAINING MANUAL WM0742HGA WM0742HGA Page 85 TRAINING MANUAL ...
Page 88: ...TRAINING MANUAL WM0742HGA WM0742HGA Page 86 TRAINING MANUAL ...
Page 89: ...TRAINING MANUAL WM0742HGA WM0742HGA Page 87 TRAINING MANUAL ...
Page 90: ...TRAINING MANUAL WM0742HGA WM0742HGA Page 88 TRAINING MANUAL ...
Page 93: ......
Page 94: ...Steam Washer Fall 2008 ...