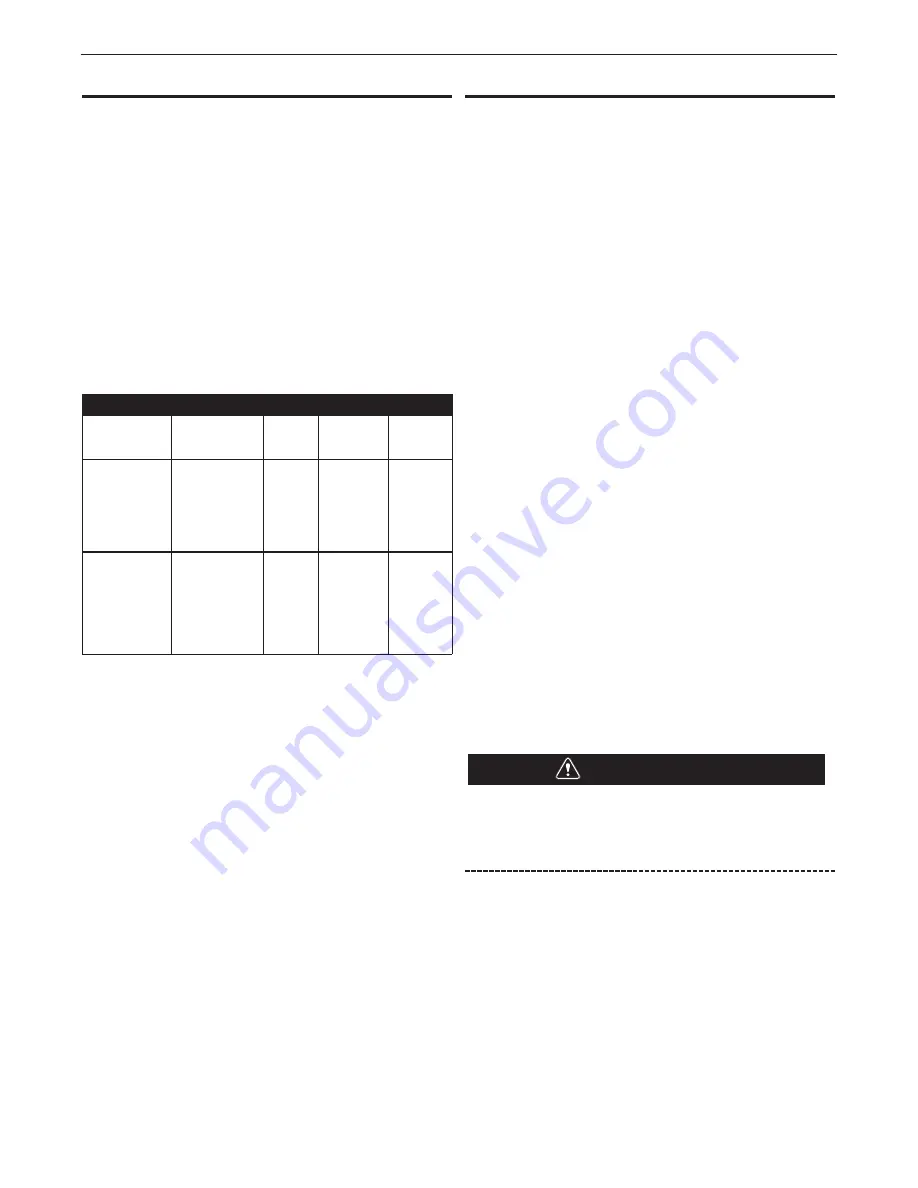
D-2
MAINTENANCE
PERIODIC MAINTENANCE
The product has been designed to function without problems for
many hours with minimal maintenance. In order to ensure this,
some simple, regular maintenance and cleaning activities are
required which are described in this section. If you observe the
necessary caution and carry out the maintenance at regular
intervals, any problems that occur will be detected and corrected
before they lead to a total breakdown.
The indicated maintenance intervals can vary depending on the
specific
working and ambient conditions. Therefore it is
recommended to thoroughly inspect the complete product once
every year other that the indicated periodic maintenance.
The maintenance activities in Table D.1 indicated by [*] can be
carried out by the user; other activities are strictly reserved for
well trained and authorized service engineers.
MAINTENANCE SCHEDULE
NOTE: * REQUIRES Lincoln Electric factory authorized service
technician.
AS NEEDED
•
Replace filters (See filter replacement instructions).
•
Inspect and test functionality of the filter media
cleaning system. *
•
Program and verify system performance. *
MONTHLY
•
Check particulate collection drum and dispose of
particulate if necessary.
•
Check and log filter pressure.
•
Check incoming pressure
EVERY 6 MONTHS
•
Ensure that the Cubic Feet per Minute (CFM) is
operating to the engineered specifications based on the
individual system *
UNIT HOUSING
•
Clean housing with a non-aggressive detergent.
•
Inspect and clean (with a non-aggressive detergent) the
fi
lter control box.
YEARLY
•
Inspect unit for proper operation and function, address
any issues found.
•
Fan motor temperature is within normal ranges, a hand
held IR temp meter is a good tool for this. High motor
temps indicate bearing or winding issues and predict a
failure. This can also apply to the electrical power
connections to the unit- elevated temps on junction
boxes and wire terminations are precursors to
problems.
MOTOR/FAN HOUSING
Observe safety precautions when working on the inside
of the fan box or control panel. Removing power and
observing LOTO (Lockout-Tagout) procedures as
required.
•
Check the integrity of the fan housing and tighten all
bolts and screws if necessary.
•
Clean housing with a non-aggressive detergent.
WARNING
TABLE D.1 – PERIODIC MAINTENANCE
COMPONENT
ACTION
EVERY
MONTH
EVERY 3
MONTHS
EVERY 6
MONTHS
Control Panel
*Clean inside
using an
industrial
vacuum
cleaner.
X
Drum
*Check levels
of dust and dirt
particulate.
Empty if
necessary.
X
X
X
*
Frequency depends on welding or cutting process.
PRISM
®
CIRCULATOR 4000
®