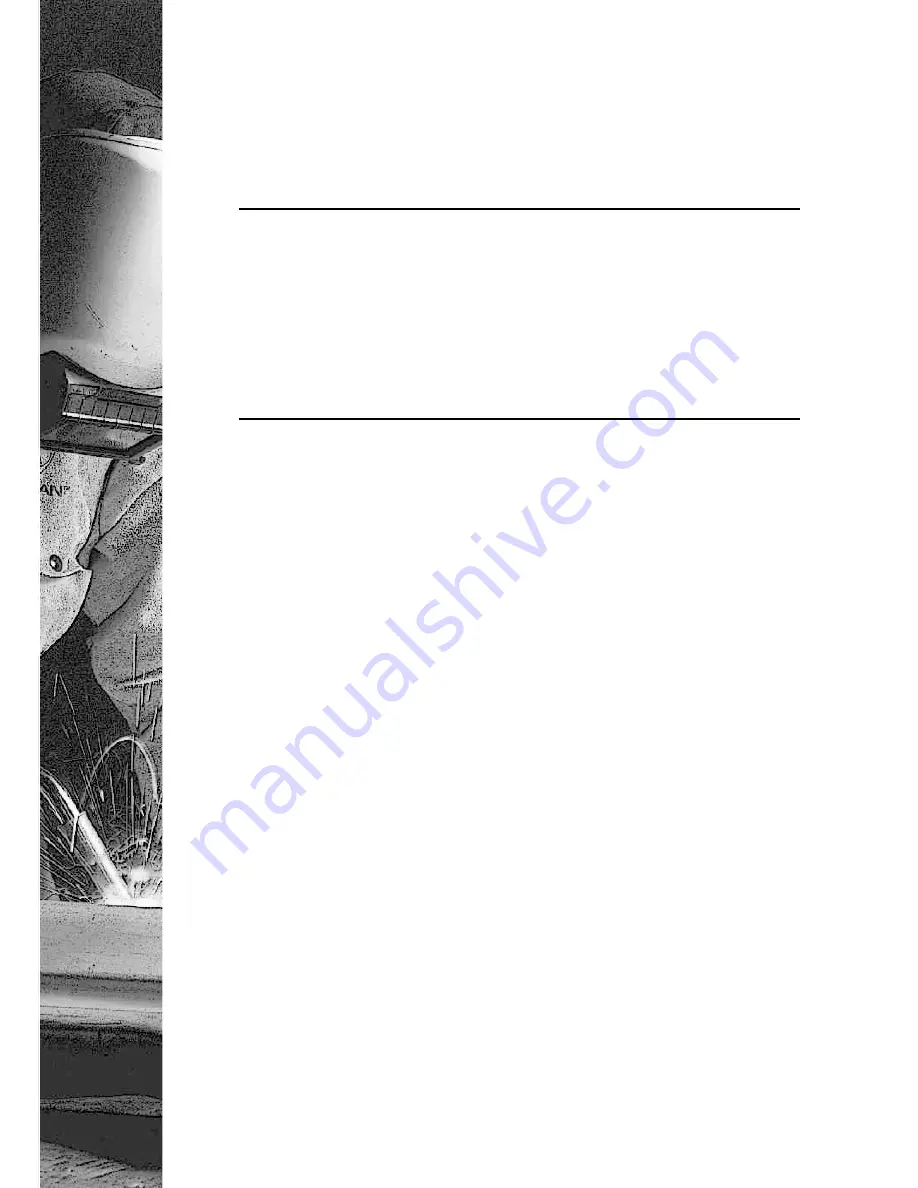
Page 25
Expressweld MasterMIG 250CT
10 Functions of Wire Feeder System
Wire drive system has the following functions:
Wire Feeding Speed Setting:
- It is possible to set the wire feeder speed between 1-20 m/min.
11 GMAW (MIG/MAG) Method
Warning!
While welding do not change the welding voltage! This may cause serious
damage.
Make sure that the welding machine is installed according to the explanations included
on Page 22.
By considering the desired welding current values, install the work cable to the
“Work
Cable Connector”
located in front of the welding machine by using the fitting screw at
the end of work cable.
Connect the work cable holder to the clean surface of the workpiece to be worked on.
Make sure that the contact between them is as good as possible.
Start the machine by turning the
“On/Off Switch”
located in the front panel of the
welding machine to "I” position. “Power Indicator” will light up.
Welding voltage value is approximately set with
“Welding Voltage Coarse Setting
Switch
” and precisely set with
“Welding Voltage Precise Setting Switch”
(Refer to
the table on Page 20). These switches are located in the front panel of welding machine.
Value of welding current directly depends on the wire feeding speed value. Choose
proper wire feeding speed with “Wire Feed Speed Setting Button” located in the front
panel of welding machine. Wire drive speed can be set between 1-20 m/min.
You can start welding procedure by following related rules.