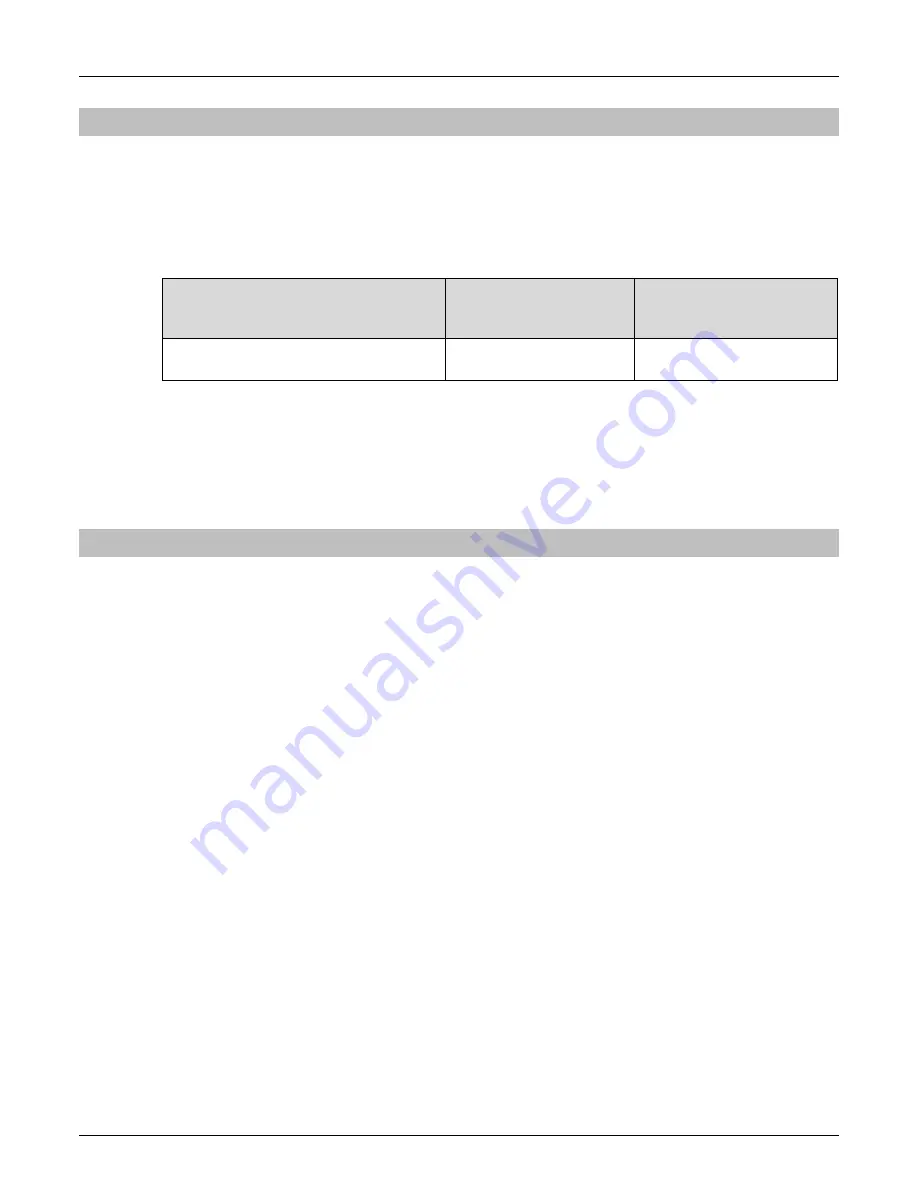
FineLine 300HD Plasma System
BK8053-000107 Rev A.01
This information is subject to the controls of the Export Administration Regulations [EAR]. This information shall not be provided to
non-U.S. persons or transferred by any means to any location outside the United States contrary to the requirements of the EAR.
Page 20 of 118
2.12 Airborne Noise Emissions
The System generates high noise levels while cutting. Depending on the size of the
cutting area, distance from the cutting torch, and arc current cutting level, acceptable
noise levels may be exceeded. Proper ear protection should be used as defined by
local or national codes. The following chart gives the noise levels generated by the
System when operating at 300 amps, 180 arc volts. The measurements were made
with a sound level meter.
Distance From Torch
A-Weighted Sound
Pressure Level
C-Weighted Sound
Pressure Level
1 meter horizontal / 1.6 meters
above the workpiece
108 dB
106 dB
The maximum noise level is 126 dB at a distance of 3 in. (76.2mm) from the torch
while cutting at 300 amps, 180 arc volts.
2.13 Electromagnetic Compatibility (EMC)
CE marked FineLine 300HD Systems are manufactured to comply with the
European standard EN 60974-10 (Electromagnetic compatibility (EMC) – Product
standard for arc welding equipment). Information about the EMC standard EN
60974-10 can be found in Appendix A.