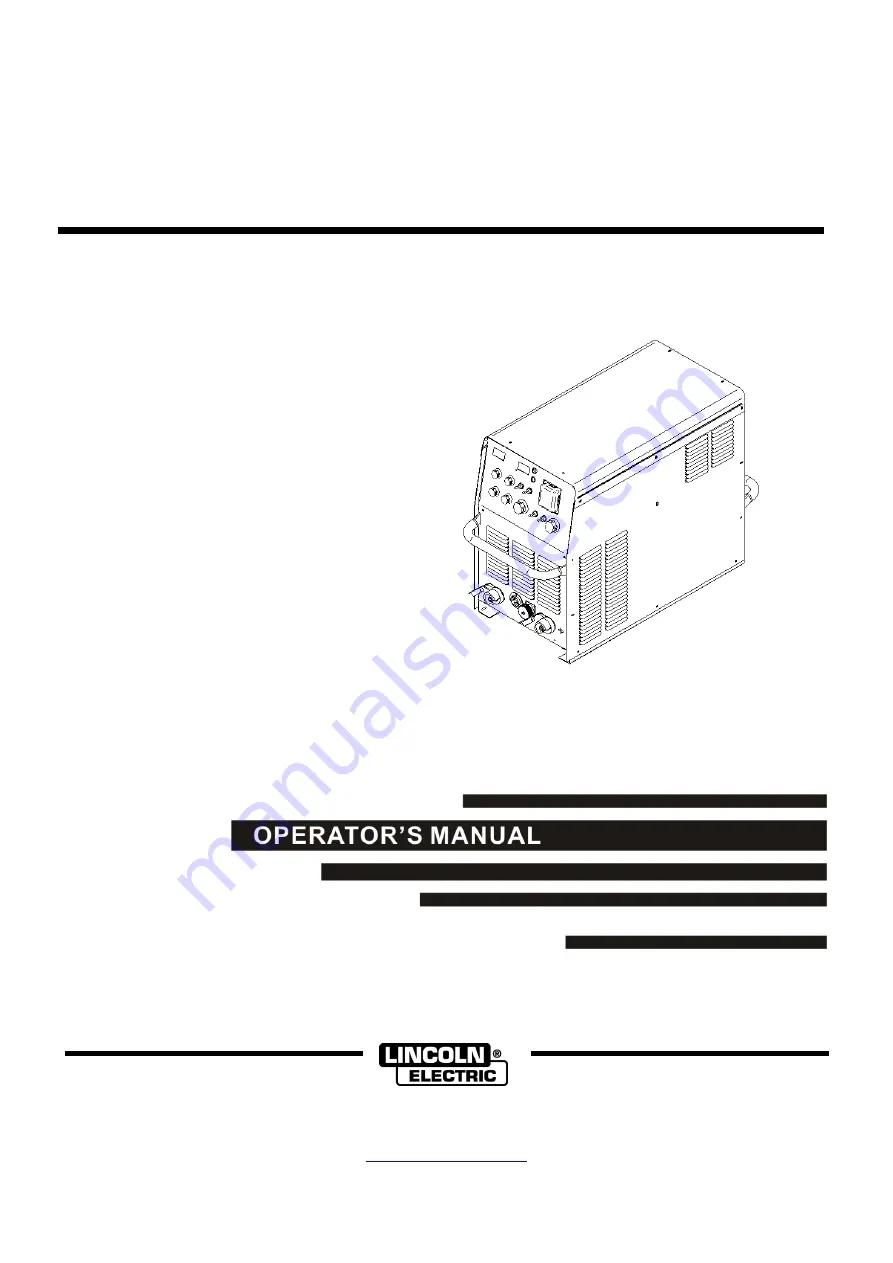
Rev. 03
IM7025-1
Feb, 2018
Rev. 03
OPTIMARC
®
CV/CC500
For use with machine Part Number K60128-1, Code 76341
• World’s Leader in Welding and Cutting•
THE SHANGHAI LINCOLN ELECTRIC COMPANY
No. 195, Lane 5008, Hu Tai Rd. Baoshan, Shanghai, PRC 201907
Copyright © 2018 The Shanghai Lincoln Electric Company
Safety Depends on You
Lincoln arc welding and cutting
equipment is designed and built
with safety in mind. However, your
overall safety can be increased by
proper installation and thoughtful
operation on you part.
DO NOT
INSTALL, OPERATE OR REPAIR
THIS EQUIPMENT WITHOUT
READING THIS MANUAL AND
THE SAFETY PRECAUTIONS
CONTAINED THROUGHOUT.
And, most importantly, think before
you act and be careful.